Selecting the right material for CNC parts is crucial for ensuring the performance, durability, and cost-effectiveness of your final product. With so many material options available, it can be overwhelming to make the best choice. In this blog, we’ll provide you with three essential tips to help you navigate this decision-making process.
1. Understand the Material Properties
The first step in choosing the right material for your CNC parts is to understand the inherent properties of different materials. This foundational knowledge allows you to match the material to the specific requirements of your application, ensuring optimal performance, durability, and cost-effectiveness.
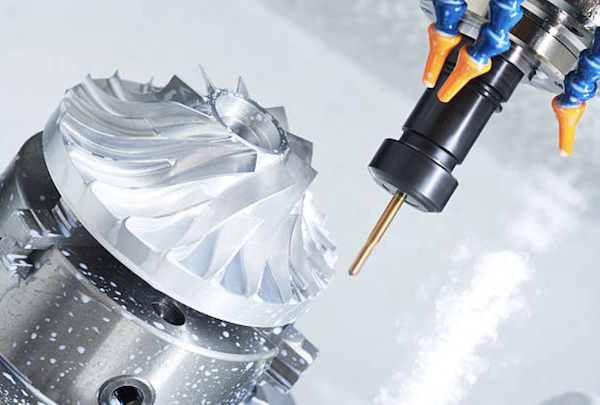
1.1 Metal Alloys: Strength and Durability
Metal alloys, such as aluminum, steel, and titanium, are renowned for their high strength and durability. These materials are ideal for parts that need to withstand heavy loads and harsh conditions.
- Aluminum: Known for its excellent strength-to-weight ratio, aluminum is easy to machine and has good thermal and electrical conductivity. It’s widely used in the aerospace, automotive, and electronics industries. However, aluminum can be prone to corrosion without proper surface treatment.
- Steel: Offering exceptional strength and toughness, steel is perfect for components exposed to high stress and impact. Various grades, such as stainless steel and tool steel, provide different levels of hardness and corrosion resistance. The downside is that steel can be heavier and harder to machine than other metals.
- Titanium: Titanium combines high strength, lightweight, and excellent corrosion resistance, making it suitable for aerospace, medical, and marine applications. It’s more expensive and challenging to machine but offers unparalleled performance in demanding environments.
Understanding the advantages and limitations of these common metal alloys helps you make an informed decision, ensuring your CNC parts meet the necessary strength and durability requirements.
1.2 Plastics: Versatility and Cost-Effectiveness
Plastics are widely used in CNC machining due to their versatility and cost-effectiveness. These materials offer a range of properties that can be tailored to various applications, from lightweight components to chemical-resistant parts.
- ABS: Acrylonitrile Butadiene Styrene (ABS) is a popular plastic known for its strength, toughness, and ease of machining. It’s commonly used in automotive parts, consumer products, and toys. ABS is also relatively inexpensive, making it a cost-effective choice for many projects.
- Nylon: Nylon is valued for its high mechanical strength, wear resistance, and low friction properties. It’s often used in gears, bearings, and other moving parts. Nylon is also resistant to many chemicals, making it suitable for industrial applications.
- PEEK: Polyether Ether Ketone (PEEK) is a high-performance plastic with excellent chemical resistance, thermal stability, and mechanical properties. It’s used in demanding applications such as aerospace, medical implants, and oil and gas components. PEEK is more expensive but offers superior performance in extreme conditions.
By understanding the specific benefits and applications of different plastics, you can choose the best material for your CNC project, balancing performance and cost.
1.3 Composites: Specialized Applications
Composite materials, such as carbon fiber and fiberglass, are designed for specialized applications where high strength-to-weight ratios and specific performance characteristics are required.
- Carbon Fiber: Carbon fiber composites offer exceptional strength, stiffness, and lightweight properties. They are widely used in aerospace, automotive, and sporting goods industries. Carbon fiber components can withstand high stresses and loads while maintaining a low weight, making them ideal for performance-critical applications. However, machining carbon fiber requires specialized tools and techniques due to its abrasive nature.
- Fiberglass: Fiberglass composites are known for their high strength, corrosion resistance, and affordability. They are used in a variety of applications, including marine, automotive, and construction. Fiberglass is less expensive than carbon fiber but still offers excellent mechanical properties and durability.
Composites provide a unique combination of properties that can be tailored to meet specific performance requirements. Whether you need lightweight components with high strength or parts that can withstand harsh environmental conditions, composites offer versatile solutions for CNC machining projects.
By thoroughly understanding the properties of metal alloys, plastics, and composites, you can make informed decisions that ensure your CNC parts are optimized for their intended applications. This knowledge allows you to balance performance, durability, and cost, achieving the best possible outcomes for your projects.
2. Evaluate the Application Requirements
When it comes to CNC machining, selecting the right material isn’t just about knowing your options—it’s about understanding the specific demands of your application. Each project has unique requirements that influence material choice, and by carefully evaluating these factors, you can ensure your parts perform optimally under real-world conditions.
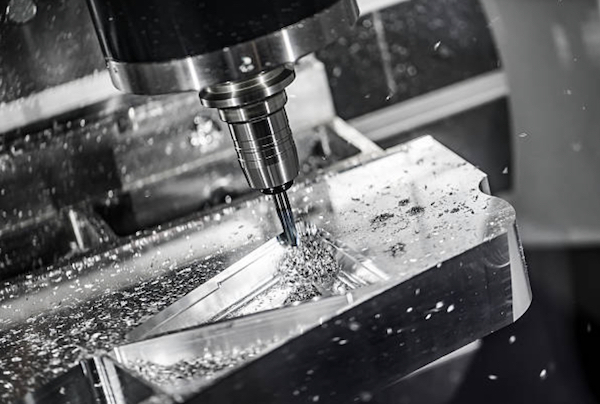
2.1 Load and Stress Considerations
Imagine you’re designing a critical component that must endure significant mechanical loads and stresses. If the material isn’t up to the task, the part could fail, leading to costly downtime and repairs. To avoid such issues, it’s essential to understand the mechanical loads your CNC part will face.
Think about this: What kind of forces will your part encounter? Is it subject to heavy loads, high impacts, or constant wear and tear? For example, choosing a robust material like steel for parts exposed to heavy stress ensures they can handle the pressure without deforming or breaking. On the other hand, for applications where weight is a concern, aluminum might be the perfect balance of strength and lightness.
By analyzing load and stress considerations, you can match the material’s properties to the demands of your application, ensuring reliability and longevity.
2.2 Environmental Factors: Corrosion and Temperature
Now, consider the environment in which your CNC part will operate. Environmental factors such as corrosion resistance and temperature tolerance are crucial in material selection. Picture your part being exposed to harsh chemicals or extreme temperatures. Without the right material, it might corrode, degrade, or fail prematurely.
For instance: If your part is used in a marine environment, stainless steel or titanium, known for their excellent corrosion resistance, would be ideal choices. Alternatively, for high-temperature applications, materials like PEEK or certain metal alloys that maintain their integrity under extreme heat should be considered.
Choosing materials that can withstand environmental challenges ensures your CNC parts remain functional and efficient, even in the most demanding conditions.
2.3 Tolerances and Precision Needs
Precision is key in CNC machining. The tighter the tolerances, the more critical the material choice becomes. High-precision parts must meet exact specifications, and the material’s properties can significantly impact the machining accuracy and stability.
Consider this scenario: You’re producing a component for a medical device that requires extremely tight tolerances. The material must not only be machinable to high precision but also stable under operating conditions. Materials like certain grades of aluminum or specialized plastics such as PEEK are known for their excellent machinability and stability, making them suitable for high-precision applications.
By understanding and evaluating the precision and tolerance needs of your parts, you can select materials that enhance machining accuracy and ensure your parts meet the stringent quality standards required for critical applications.
3. Consider the Cost and Availability
When embarking on a CNC project, one of the most pivotal aspects to consider is the cost and availability of materials. Striking the right balance between staying within your budget and ensuring high-quality materials is crucial for the success of your project. Let’s dive into how you can effectively manage this balancing act.
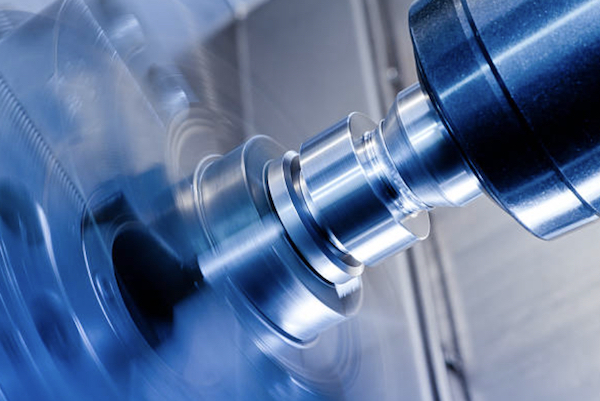
3.1 Material Cost Analysis
Imagine you’re excited to kickstart a new project, but as you begin sourcing materials, you realize the costs are spiraling out of control. This is where a thorough material cost analysis comes into play.
Now, think about the frustration of having your project delayed because the materials you need are out of stock or have long lead times. Supply chain issues can derail even the most well-planned projects.
Consider this scenario: You’ve carefully chosen a high-quality material, but its availability is limited, causing significant delays. We’ll discuss strategies to navigate these challenges, such as working with reliable suppliers, considering alternative materials, or planning for longer lead times in your project schedule. By being proactive and understanding the supply chain dynamics, you can ensure a smooth workflow and timely project completion.
3.2 Supply Chain and Lead Times
Now, think about the frustration of having your project delayed because the materials you need are out of stock or have long lead times. Supply chain issues can derail even the most well-planned projects.
Consider this scenario: You’ve carefully chosen a high-quality material, but its availability is limited, causing significant delays. We’ll discuss strategies to navigate these challenges, such as working with reliable suppliers, considering alternative materials, or planning for longer lead times in your project schedule. By being proactive and understanding the supply chain dynamics, you can ensure a smooth workflow and timely project completion.
3.3 Balancing Quality and Budget
Balancing quality and budget is akin to walking a tightrope—one misstep can lead to overspending or compromising on performance. However, achieving this balance is not only possible but also essential for a successful CNC project.
Envision this: You’re tasked with producing a part that must be both affordable and high-quality. How do you proceed? We’ll offer practical tips on evaluating material properties against your budget constraints. For example, choosing a slightly more expensive material with superior durability can save costs in the long run by reducing maintenance and replacement needs. Understanding the trade-offs and making informed decisions ensures that you get the best value for your money without sacrificing the quality and performance of your CNC parts.
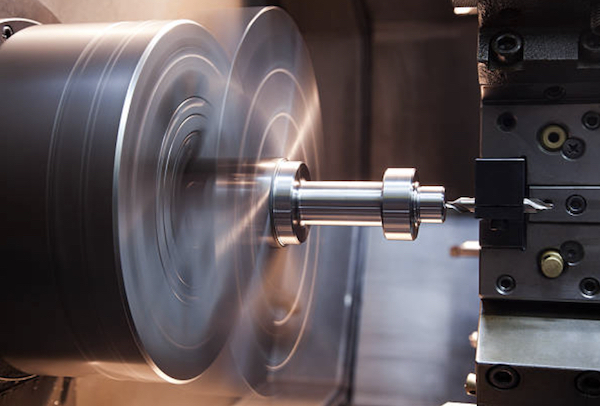
Conclusion
Selecting the right material for CNC parts isn’t just about picking what’s available—it’s about making informed decisions that guarantee the success of your projects. By understanding material properties, evaluating application requirements, and considering cost and availability, you can ensure your CNC parts are optimized for performance, durability, and budget.
Ready to elevate your CNC projects? Contact RALLY today for expert guidance and top-quality materials!
FAQs
What are the most common materials used in CNC machining?
How do I determine the best material for my CNC part?
What factors should I consider for high-precision CNC parts?
How does material choice impact CNC machining costs?
Can I use multiple materials for a single CNC part?
What are the advantages of using composites in CNC machining?
Work with RALLY for CNC Machining Parts
Request a quote for new project today! No minimum order quantity and free samples available!