Are you in the market for efficient, cost-effective solutions for low-volume production? Look no further. At RALLY, we specialize in providing top-tier 3D printed molds tailored for small batch manufacturing. Whether you’re in the automotive, medical, or consumer electronics industry, our advanced 3D printing technology ensures high-quality, precise molds that meet your exact specifications. Discover how 3D printed molds can revolutionize your production process, save costs, and reduce lead times. Join us as we explore the benefits, technical insights, and problem-solving capabilities of 3D printed molds for low-volume manufacturing.
1. What is a 3D printed mold?
3D printing molds are molds made using 3D printing technology to produce parts made of plastic, metal and other materials. Compared with traditional molds, 3D printed molds have the advantages of short production cycle, low cost and flexible design. Through additive manufacturing technology, 3D printed molds can easily achieve complex geometries and detailed designs, and are widely used in small batch production and prototyping.
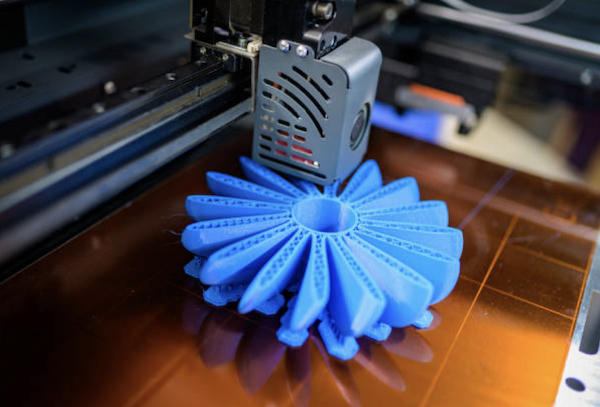
3D printed molds are fast becoming an effective and cost-efficient solution in low-volume manufacturing. Compared to traditional mold manufacturing methods, 3D printing technology not only dramatically reduces production time and costs, but also offers greater design freedom and flexibility. It allows companies to quickly create and modify molds, thereby accelerating product development cycles.
In addition, 3D printed molds are particularly suitable for projects with high customization needs and small production batches, which can accurately meet customers’ special needs and enhance product quality and market competitiveness.
2. Why choose 3D printed molds for low volume manufacturing?
For low volume production, there are several key advantages to using 3D printed molds:
Cost Effectiveness:
For low volume production (typically 10-1000 parts), 3D printed molds can cost 50%-90% less than traditional injection molding. This is because 3D printed molds avoid the cost of manufacturing expensive metal molds, which can cost thousands of dollars each.
Rapid Production Cycle:
3D printing technology allows for rapid production of molds, greatly reducing the production cycle. This is especially important for projects that require rapid prototyping or short production runs.
Flexibility and Iterability:
3D printed molds allow for easier and more economical design modifications. If design adjustments need to be made, new molds can be printed quickly without the need for expensive metal mold remakes.
Ideal for complex designs:
3D printing allows for the creation of very complex shapes and structures that may be difficult to achieve through traditional manufacturing methods. This provides designers with greater freedom.
Reduces material waste:
As an additive manufacturing process, 3D printing uses only the necessary materials to build the molds, resulting in better material utilization and less waste.
Suitable for customized production:
3D printing is ideal for customized production in small batches and can cost-effectively produce customized parts in a single run.
3. Finding the Right Service Provider
When choosing a service provider for your 3D printing molds, it is critical to find an experienced, technologically advanced partner that offers quality support, and RALLY is a trusted choice. Here are a few key reasons to choose RALLY as your 3D printing mold service provider:
1. Experienced
RALLY has many years of experience in the manufacturing industry and has successfully provided countless high-quality 3D printed mold solutions to various industries around the world. We understand the unique needs of each customer and are able to provide customized advice and services based on specific projects.
2. Advanced Technology
RALLY utilizes the most advanced 3D printing technologies, including FDM, SLA and SLS, and is capable of working with a wide range of materials such as plastics, resins and metals. Our equipment and technology ensure that each mold has the highest precision and quality.
3. Quality Support
We offer a full range of customer support services, from initial consultation to design optimization, to production and delivery, every step of the way, our professional team is there for you. Our goal is to ensure that your project runs smoothly and achieves the desired results.
4. Cost-effective
RALLY is committed to providing cost-effective solutions for our customers. Our 3D printed molds are not only reasonably priced, but also help customers save time and cost and improve productivity.
Reasons to recommend RALLY
Comprehensive service: one-stop solution for all your needs, from design to manufacturing.
Fast delivery: shorten production cycle and accelerate time-to-market.
Flexibility: Adapt to different sizes and types of projects, providing highly customized services.
Get Your CNC Parts Into Production Today
Your Global Partner for Quality CNC Machining Services in China!
4. Technical Insights into 3D Printing Molds
4.1 3D printing technologies: FDM, SLA, SLS
In the production of 3D printed molds, different technologies offer unique advantages and are suited for various applications. Here is an overview of some common 3D printing technologies:
1. FDM (Fused Deposition Modeling)
Principle: FDM technology works by heating and extruding thermoplastic materials, depositing them layer by layer to build up the final 3D object. Materials: Common materials include PLA, ABS, and Nylon. Advantages:
- Low Cost: Equipment and materials are relatively inexpensive.
- Ease of Use: User-friendly and suitable for rapid prototyping.
- Diverse Material Options: Suitable for various thermoplastic materials. Applications: Ideal for creating quick prototypes, functional parts, and low-cost models.
2. SLA (Stereolithography)
Principle: SLA uses UV lasers to cure photopolymer resin layer by layer, forming highly detailed 3D structures. Materials: Primarily photopolymer resins. Advantages:
- High Precision: Capable of producing very fine details and complex geometries.
- Smooth Surface Finish: High-quality surface finish of the printed parts.
- Rapid Prototyping: Suitable for applications requiring high precision and surface quality. Applications: Ideal for producing high-precision molds, intricate prototypes, and models.
3. SLS (Selective Laser Sintering)
Principle: SLS technology uses a laser to sinter powdered materials layer by layer, creating solid 3D objects. Materials: Common materials include Nylon, Polyamide, and metal powders. Advantages:
- High Strength: Parts have excellent mechanical properties.
- No Support Structures Needed: Suitable for complex geometries.
- Wide Material Selection: Includes both plastic and metal materials. Applications: Ideal for functional parts, low-volume production, and end-use products.
Choosing the Right Technology
The choice of 3D printing technology depends on the specific requirements and priorities of the project:
- FDM: Suitable for quick, low-cost prototyping.
- SLA: Suitable for projects requiring high precision and surface quality.
- SLS: Suitable for applications needing high strength and complex structures.
Comparison Table of 3D Printing Technologies: FDM, SLA, SLS
Feature | FDM (Fused Deposition Modeling) | SLA (Stereolithography) | SLS (Selective Laser Sintering) |
---|---|---|---|
Working Principle | Heats and extrudes thermoplastic material, depositing it layer by layer | Uses UV laser to cure photopolymer resin layer by layer | Uses laser to sinter powdered materials layer by layer |
Common Materials | PLA, ABS, Nylon, and other thermoplastics | Photopolymer resins | Nylon, Polyamide, Metal powders |
Precision | Medium | High | High |
Surface Quality | Medium | Very smooth | Medium to high |
Cost | Low | Medium to high | High |
Speed | Fast | Fast | Medium |
Advantages | – Low cost<br>- Easy to use<br>- Versatile material options | – High precision<br>- Excellent surface quality<br>- Suitable for complex geometries | – High strength<br>- No support structures needed<br>- Wide material selection |
Applications | – Rapid prototyping<br>- Functional parts<br>- Low-cost models | – High-precision molds<br>- Intricate prototypes<br>- Visual models | – Functional parts<br>- Low-volume production<br>- End-use products |
4.2 Material options: plastic, resin and metal.
1. Plastics
Common Types: PLA, ABS, Nylon, PETG, TPU Advantages:
- Versatility: Suitable for a wide range of applications.
- Ease of Use: Generally easy to print with, making it ideal for rapid prototyping.
- Cost-Effective: Relatively inexpensive compared to other materials. Applications:
- PLA (Polylactic Acid): Ideal for prototyping and educational purposes due to its ease of printing and environmental friendliness.
- ABS (Acrylonitrile Butadiene Styrene): Suitable for functional prototypes and parts requiring impact resistance and toughness.
- Nylon: Used for parts requiring high strength, flexibility, and durability, such as gears and bearings.
- PETG (Polyethylene Terephthalate Glycol): Known for its good balance of strength, flexibility, and chemical resistance.
- TPU (Thermoplastic Polyurethane): Used for flexible parts like gaskets, seals, and custom footwear.
Feature | Plastics | Resins | Metals |
---|---|---|---|
Common Types | PLA, ABS, Nylon, PETG, TPU | Standard, Tough, Flexible, High-Temperature, Dental | Aluminum, Stainless Steel, Titanium, Inconel, Copper |
Advantages | – Versatile<br>- Easy to use<br>- Cost-effective | – High detail and smooth finish<br>- Specialized properties | – High strength and durability<br>- Heat resistance<br>- Conductivity |
Applications | – Prototyping<br>- Functional parts<br>- Low-cost models | – High-precision molds<br>- Intricate prototypes<br>- Models requiring fine details | – End-use parts<br>- Functional prototypes<br>- High-performance applications |
Typical Uses | – PLA: Prototyping, educational purposes<br>- ABS: Functional prototypes, parts needing toughness<br>- Nylon: Gears, bearings<br>- PETG: Strong, flexible parts<br>- TPU: Gaskets, seals, custom footwear | – Standard Resin: General-purpose prototypes<br>- Tough Resin: Functional prototypes needing impact resistance<br>- Flexible Resin: Bendable parts like seals and grips<br>- High-Temperature Resin: Molds for injection molding<br>- Dental Resin: Accurate, biocompatible dental models | – Aluminum: Aerospace, automotive, consumer electronics<br>- Stainless Steel: Medical instruments, kitchenware<br>- Titanium: Aerospace, medical implants<br>- Inconel: Turbine blades, exhaust systems<br>- Copper: Electrical components, heat exchangers |
2. Resins
Common Types: Standard, Tough, Flexible, High-Temperature, Dental Advantages:
- High Detail and Smooth Finish: Excellent for parts requiring fine details and a smooth surface finish.
- Specialized Properties: Different resins offer various properties such as flexibility, toughness, and temperature resistance. Applications:
- Standard Resin: Ideal for general-purpose prototypes and visual models.
- Tough Resin: Suitable for functional prototypes requiring impact resistance and mechanical strength.
- Flexible Resin: Used for parts that need to bend and flex, like seals and grips.
- High-Temperature Resin: Suitable for parts that need to withstand high temperatures, such as molds for injection molding.
- Dental Resin: Used in dental applications for making accurate and biocompatible dental models and appliances.
3. Metals
Common Types: Aluminum, Stainless Steel, Titanium, Inconel, Copper Advantages:
- High Strength and Durability: Metals offer excellent mechanical properties and are suitable for end-use parts and functional prototypes.
- Heat Resistance: Capable of withstanding high temperatures and harsh environments.
- Conductivity: Certain metals like copper and aluminum are excellent conductors of heat and electricity. Applications:
- Aluminum: Used in aerospace, automotive, and consumer electronics for its lightweight and high strength-to-weight ratio.
- Stainless Steel: Suitable for parts requiring corrosion resistance and strength, such as medical instruments and kitchenware.
- Titanium: Ideal for high-performance applications in aerospace and medical implants due to its strength, light weight, and biocompatibility.
- Inconel: Used in high-temperature applications such as turbine blades and exhaust systems.
- Copper: Ideal for electrical components and heat exchangers due to its excellent conductivity.
5. Case Studies: Examples of 3D Printed Molds Solving Practical Problems
Case Study 1: Rapid Prototyping in the Automotive Industry
Problem: A leading automotive manufacturer needed to rapidly prototype new design components for their latest vehicle model. Traditional mold-making processes were time-consuming and costly, leading to delays in the product development cycle.
Solution: The manufacturer turned to 3D printed molds using FDM technology with ABS plastic. This approach allowed them to quickly produce and test multiple design iterations at a fraction of the cost and time of traditional methods.
Outcome:
- Speed: Reduced prototyping time from weeks to days.
- Cost Savings: Significant reduction in prototyping costs.
- Flexibility: Enabled rapid design changes and iterations.
Case Study 2: High-Precision Molds for Medical Devices
Problem: A medical device company required high-precision molds to produce custom surgical instruments. The traditional mold-making process did not offer the necessary detail and surface finish required for these sensitive medical tools.
Solution: The company utilized SLA technology with high-precision photopolymer resins to create molds with intricate details and smooth surfaces. This method ensured the production of high-quality, biocompatible surgical instruments.
Outcome:
- Precision: Achieved fine details and high surface quality.
- Compliance: Met stringent medical industry standards.
- Customization: Produced patient-specific instruments.
Case Study 3: Functional Parts for Aerospace Applications
Problem: An aerospace company needed to produce functional parts for testing and evaluation under extreme conditions. The parts required high strength, durability, and resistance to high temperatures.
Solution: The company employed SLS technology with nylon and metal powders (such as Inconel) to create parts that could withstand the rigorous demands of aerospace applications.
Outcome:
- Durability: Produced parts with high mechanical strength and durability.
- Heat Resistance: Parts capable of operating in high-temperature environments.
- Performance: Improved performance in functional testing scenarios.
These case studies illustrate how 3D printed molds can effectively solve practical problems across various industries, from automotive and medical to aerospace and consumer products. By leveraging the unique advantages of FDM, SLA, and SLS technologies, companies can achieve faster production times, lower costs, higher precision, and greater flexibility. RALLY is equipped to provide customized 3D printed mold solutions to address your specific challenges and improve your manufacturing processes.
6. Conclusion
In summary, 3D printed molds have proven to be a versatile and cost-effective solution for various manufacturing challenges across industries like automotive, medical, aerospace, and consumer electronics. By leveraging advanced technologies such as FDM, SLA, and SLS, companies can achieve rapid prototyping, high precision, and robust functionality, all while reducing costs and production times. These case studies highlight the transformative potential of 3D printed molds in solving real-world problems and driving innovation.
Ready to revolutionize your manufacturing process with 3D printed molds? Contact RALLY today to learn how our expertise and cutting-edge technology can meet your specific needs. Reach out now for a consultation or to request a quote.
Work with RALLY for CNC Machining Parts
Request a quote for new project today! No minimum order quantity and free samples available!