Introduction:
A radiator is a device used for heat dissipation and cooling, and its main function is to conduct and distribute the heat generated by the heat source to the surrounding environment, so as to maintain the normal operating temperature of the equipment or system. Heat sinks are widely used in electronic equipment, automobiles, and industrial machinery to ensure system reliability and performance.
1. Material Selection for CNC Machined Heat Sinks
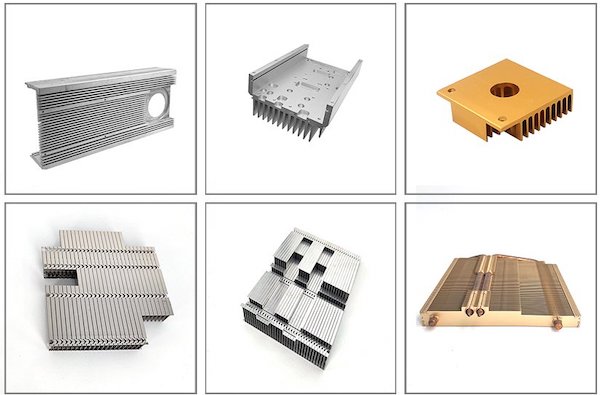
Aluminum
- Characteristics: Lightweight, good thermal conductivity, and strong corrosion resistance.
- Applications: Widely used in electronic devices, LED lighting, automotive industry, etc.
Copper
- Characteristics: Excellent thermal conductivity, but heavier and more expensive.
- Applications: Often used in high-performance heat sinks, such as those for computers and servers.
Other Materials
- Brass: Good thermal conductivity and corrosion resistance, suitable for specialized applications.
- Stainless Steel: High strength and corrosion resistance, but lower thermal conductivity.
- Ceramics: Good electrical insulation and high-temperature resistance, used in specialized electronic equipment.
Performance Comparison of Various Materials
Material | Thermal Conductivity (W/m·K) | Density (g/cm³) | Cost | Advantages | Disadvantages |
---|---|---|---|---|---|
Aluminum | 205 | 2.7 | Low | Lightweight, good thermal conductivity, easy to process | Lower strength |
Copper | 385 | 8.96 | High | Excellent thermal conductivity, antimicrobial properties | Heavy, high cost |
Brass | 109 | 8.4 | Medium | Corrosion resistance, easy to process | Lower thermal conductivity |
Stainless Steel | 16 | 7.8 | Medium | Corrosion resistance, high strength | Poor thermal conductivity |
Ceramics | 30-120 | 3.5-6 | High | Good electrical insulation, high-temperature resistance | Fragile, difficult to process |
2. How to Choose the Right Material
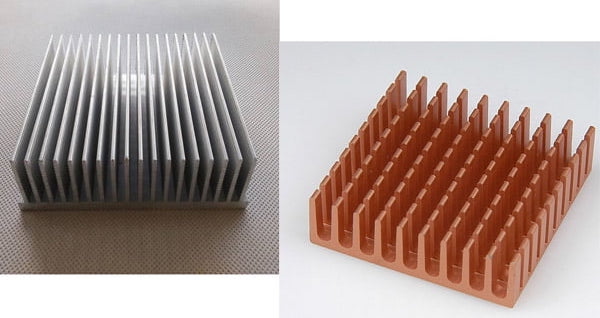
Thermal Performance
- Select materials with appropriate thermal conductivity based on cooling requirements. For high-performance needs, such as computer heat sinks, copper is ideal; for general electronic devices, aluminum suffices.
Weight
- For applications with strict weight constraints, such as aerospace or portable devices, aluminum is the best choice due to its lightweight nature.
Cost
- Cost is a significant factor. When budget is limited, aluminum offers a high cost-performance ratio. Although copper provides superior performance, it comes at a higher cost.
Environmental Conditions
- Consider the working environment of the heat sink. For corrosive environments, materials like stainless steel or brass with strong corrosion resistance are suitable. For high-temperature conditions, ceramics are a viable option.
Processing Difficulty
- Different materials have varying degrees of processing difficulty. Aluminum and copper are easier to process, while ceramics and stainless steel are more challenging. For complex geometries or high-precision requirements, choosing easily machinable materials can improve production efficiency.
3. Design Principles of CNC Machined Heat Sinks
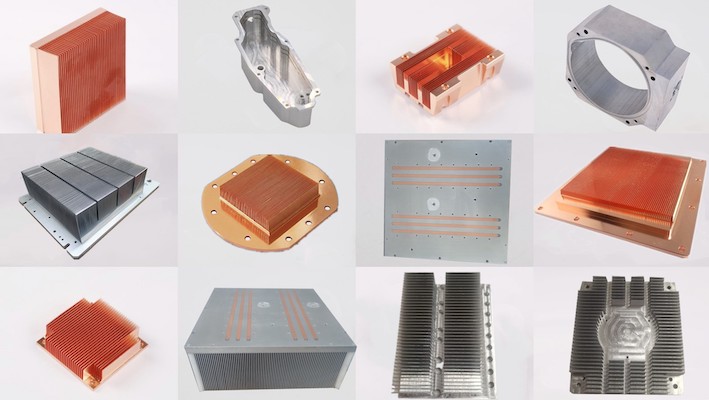
Thermal Management
- Heat Dissipation Efficiency: The primary function of a heat sink is to dissipate heat effectively. Design should maximize the surface area in contact with the air to improve thermal transfer.
- Material Selection: Choose materials with high thermal conductivity, such as aluminum or copper, to enhance heat dissipation.
Structural Integrity
- Mechanical Strength: Ensure the heat sink design can withstand physical stresses and maintain structural integrity under operational conditions.
- Durability: Consider environmental factors like corrosion, wear, and thermal cycling to ensure long-term durability.
Manufacturability
- Ease of CNC Machining: Design features should be compatible with CNC machining capabilities to ensure efficient and cost-effective production.
- Complexity: Avoid overly complex designs that may increase machining time and cost without significantly improving performance.
Compatibility
- Component Integration: The heat sink design must fit seamlessly with the electronic components or systems it is intended to cool.
- Mounting and Installation: Include features for easy mounting and secure installation, such as screw holes or clips.
Get Your CNC Parts Into Production Today
Your Global Partner for Quality CNC Machining Services in China!
4. Manufacturing Process of CNC Machined Heat Sinks
CNC Programming and Machining Steps
CNC Programming
- CAM Software: Use CAM (Computer-Aided Manufacturing) software to convert CAD drawings into CNC machine instructions (G-code).
- Toolpath Optimization: Optimize toolpaths for efficient material removal, minimizing machining time while ensuring high precision.
- Simulation: Run simulations to verify the CNC program, checking for potential errors or collisions before actual machining.
Machining Steps
- Setup: Secure the raw material on the CNC machine using designed fixtures and align it correctly.
- Rough Machining: Perform rough machining to quickly remove excess material and shape the heat sink to near-final dimensions.
- Finishing Machining: Conduct finishing machining operations to achieve the final dimensions and surface quality, including precise cuts and detailed features.
- Deburring: Remove any burrs or sharp edges left from machining to ensure smooth surfaces and safe handling.
Surface Treatment Techniques
Anodizing
- Process: Anodizing involves electrochemical oxidation, creating a protective oxide layer on the aluminum surface.
- Benefits: Enhances corrosion resistance, surface hardness, and can provide an aesthetically pleasing finish with various color options.
Sandblasting
- Process: Sandblasting uses high-pressure abrasive particles to clean and texture the surface of the heat sink.
- Benefits: Improves surface roughness for better paint or coating adhesion, and can create a uniform matte finish.
Other Treatments
- Chemical Polishing: Smooths and brightens the surface by chemical means, improving reflectivity and appearance.
- Powder Coating: Applies a durable, protective powder layer, available in a wide range of colors and finishes.
Quality Control and Inspection
Dimensional Inspection
- CMM (Coordinate Measuring Machine): Use CMM to measure the dimensions and geometrical features of the heat sink with high precision.
- Manual Gauges: Employ calipers, micrometers, and other manual measuring tools for spot-checking critical dimensions.
Surface Quality Inspection
- Surface Roughness Tester: Measure the surface roughness to ensure it meets the specified requirements.
- Visual Inspection: Check for surface defects such as scratches, dents, or inconsistent finishes.
Thermal Performance Testing
- Thermal Analysis: Test the heat sink’s thermal performance in real or simulated operational conditions to verify it meets the required specifications.
- Stress Testing: Conduct stress tests to ensure the heat sink can withstand the operational thermal cycles and mechanical loads.
Final Quality Audit
- Documentation Review: Ensure all manufacturing and inspection records are complete and accurate.
- Sample Testing: Randomly select finished heat sinks for detailed testing and validation before mass production approval.
5. Advantages of CNC Machining for Heat Sinks
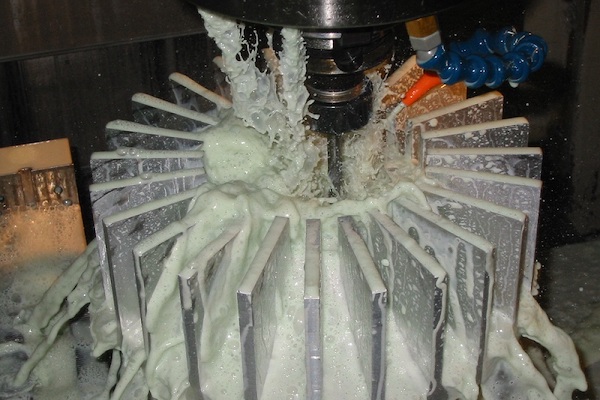
CNC (numerical control) machining has a number of significant advantages in the production of radiators:
High precision machining
CNC machining utilizes a computer-controlled system that enables high-precision machining. This ensures that the individual components of the radiator are dimensionally accurate, contributing to improved thermal efficiency and overall performance.
Consistent machining quality
CNC machining is able to maintain stable machining quality, and the finished product has a clear surface texture, strong metallic texture, flat and smooth, no scratches, and no missing corners. This not only improves the aesthetics of the radiator, but also ensures product consistency.
High efficiency production
In the case of multi-species, small batch production, CNC machining has a high production efficiency. It reduces the time spent on production preparation, machine tool adjustments and process inspections, thus improving overall productivity.
Ability to machine complex shapes
CNC machining technology is capable of machining complex radiator shapes, which provides greater flexibility in radiator design to optimize heat dissipation on demand.
6. CNC Machining Processes for Heat Sinks
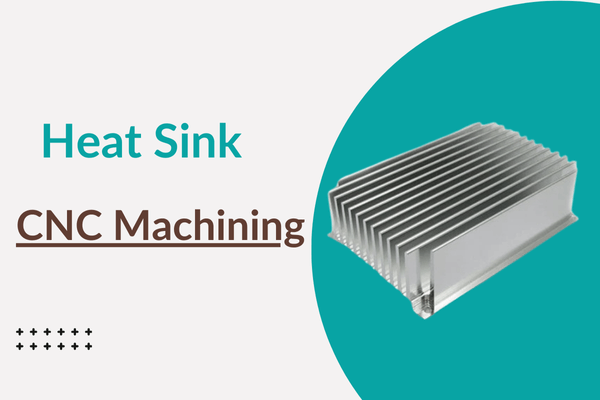
CNC machining provides a variety of manufacturing processes by incorporating 3-axis and 5-axis CNC machines to make high-precision heat sinks with simple and complex designs.
Milling:
This operation involves removing material from a workpiece with a rotating instrument or cutting tool. Milling is used in heat sink fabrication to shape heat sink base, create fin surfaces and make complex cooling channels. Different milling cutters such as end mills, ball-nose mills are used for desired geometries.
Turning:
In CNC turning, the workpiece rotates while the cutting tool remains stationary and this helps to remove material. While less common for heat sink bases, turning can be used to create cylindrical components like mounting studs or threaded holes.
Drilling and tapping:
Heat sink’s manufacturing requires drilling holes through which mountings, fluid channels and other elements could be installed. Drilling is critical for creating circular holes; while tapping involves making threads for fasteners.
Tool selection:
It is crucial to select the right cutting tools to obtain good performance in machining with the required surface finish. Some of these factors include material, cutting speed, feed rate, and desired surface quality. In heat sink machining high-speed steel (HSS) and carbide tools are commonly incorporated.
Coolant strategies:
Using coolant in heat sink CNC machining is essential. This strategy helps in preventing tool wear. Coolants also improve machine efficiency and improve surface finishes. Coolants control heat during the machining process, improve chip evacuation, and also reduce friction. There are different coolant types such as flood coolant and mist coolant, which can be used based on machining conditions and material.
Workholding:.
Ensuring proper clamping of the workpiece is essential during its machining. It is good to achieve dimensional accuracy and prevents any chatter. Examples of such devices are vise jaws, clamps and fixtures which hold the heat sink in place during machining operations.
7. Advanced Techniques for Complex Heat Sinks
With every passing day, new machines are being developed which require high-performance thermal power management systems. To meet the demands of complex design heat sinks, CNC machining provides advanced manufacturing methods listed below.
5-axis machining:
With 5-axis machining, you can conveniently control the workpiece 5 simultaneous directions. Hence, making complex heat sinks is pretty easy. For manufacturing heat sinks, 5-axis machining is essential in the production of complex cooling channels with undercuts and variable fin geometries that enhance heat transfer efficiency.
High-speed machining (HSM):
This method involves using high spindle speeds and feed rates to rapidly remove materials. HSM is particularly useful for cutting hard materials and achieving fine surface finishes. To manufacture heat sinks, implementing HSM can reduce machining time as well as enhance part quality.
Metal skiving:
It is a process whereby a rotating cutter with multiple cutting edges continuously makes chips by removing material. Hence, it offers high material removal rates and excellent surface finish necessary in making thin walled heat sinks having intricate patterns.
Multitasking CNC machines:
They combine more than one operation such as milling, turning and drilling in one setup. This reduces set-up times, improves accuracy and produces complex fins with minimal handling.
8. Applications of CNC Machined Heat Sinks
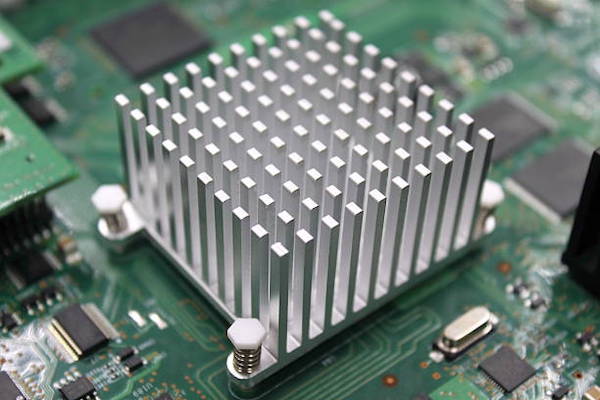
Electronics Industry
- Computers and Servers
- CPU and GPU Cooling: CNC machined heat sinks are critical for dissipating heat from central processing units (CPUs) and graphics processing units (GPUs), ensuring stable performance and preventing overheating.
- Data Centers: High-performance heat sinks are used in servers and data centers to manage the significant heat generated by densely packed electronic components.
- Consumer Electronics
- Smartphones and Tablets: Compact heat sinks help manage the heat from processors and other components in smartphones and tablets, enhancing performance and battery life.
- LED Lighting: Efficient heat sinks are essential for maintaining the longevity and performance of LED lights by managing the heat they generate.
Automotive Industry
- Electric Vehicles (EVs)
- Battery Cooling: CNC machined heat sinks are used to cool battery packs, improving their efficiency and lifespan.
- Power Electronics: Heat sinks are critical for cooling inverters, converters, and other power electronics components in EVs.
Aerospace Industry
- Avionics
- Flight Control Systems: CNC machined heat sinks are used to cool avionics systems, which are critical for the safe operation of aircraft.
- Satellite Components: Heat sinks are used in satellites to dissipate heat from electronic components in the vacuum of space.
- Aircraft Systems
- Engine Control Units: Heat sinks help manage the heat in engine control units, ensuring they operate efficiently under various conditions.
Telecommunications
- Base Stations
- Transmitter Cooling: Heat sinks are essential for cooling transmitters in telecommunications base stations, maintaining signal quality and reliability.
- Network Equipment
- Routers and Switches: Efficient cooling solutions are necessary for network equipment to handle the heat generated by high-speed data processing and transmission.
9. Conclusion
CNC machined heat sinks are essential components for efficient thermal management across various industries, from electronics to renewable energy. By understanding the key design principles, selecting the right materials, and following a meticulous manufacturing process, you can ensure optimal performance and reliability. Addressing common issues such as thermal performance, mechanical strength, and surface finish is crucial for maintaining high standards.
Ready to enhance your thermal management solutions with precision-engineered heat sinks? Contact us today to discuss your specific needs and discover how our CNC machining expertise can benefit your projects.
Work with RALLY for CNC Machining Parts
Request a quote for new project today! No minimum order quantity and free samples available!