1. What are machined parts?
Machined parts are high-precision components created through machining processes such as cutting, milling, and drilling. By removing excess material from raw stock, these parts are shaped to meet specific design requirements.
With the advancement of CNC technology, machining has become more automated, significantly improving both production efficiency and precision. One key feature of machined parts is their high accuracy and customization, making them ideal for industries requiring complex designs and tight tolerances.
Additionally, these parts often undergo refined surface treatments to ensure they not only function optimally but also meet the highest aesthetic standards.
2. Common Machining Processes
Machining involves a series of processes used to machine a variety of materials to produce parts that are precise and meet design requirements. Here are some common machining processes:
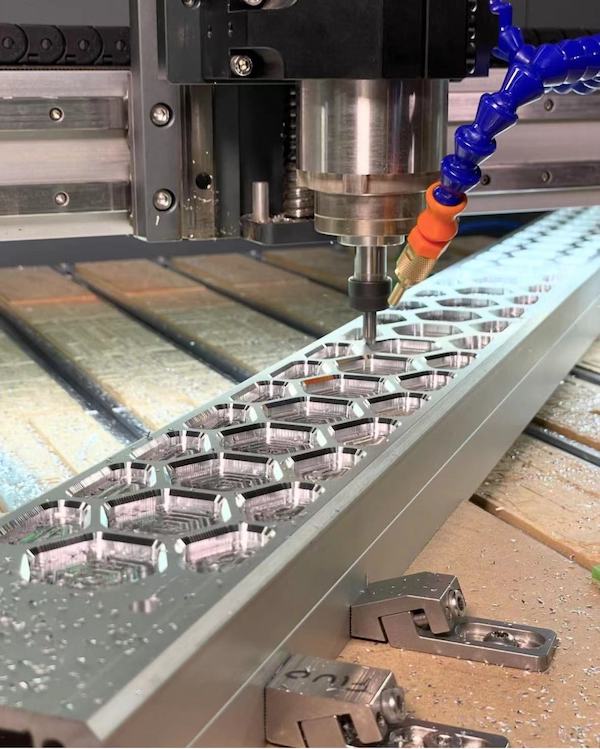
CNC Machining:
CNC machining is one of the most widely used modern processes. By controlling the machine tool through computer programming, CNC machining is able to automate operations such as cutting, milling and turning, ensuring high accuracy and consistency.
Turning:
A machining process performed on a lathe by rotating the workpiece and using a tool to remove excess material, commonly used to create cylindrical parts such as shafts, threads and gears.
Milling:
The milling process uses a rotating tool to remove material and is capable of machining flat, bevelled or complex shapes. Milling machines are often used to machine moulds, flat surfaces and grooves in workpieces.
Drilling:
Drilling is the process of punching holes in a material by means of a rotating drill and is often used to create precise holes for bolt holes or holes for fitting connections.
Grinding:
Grinding uses abrasives such as grinding wheels to remove material and is often used to machine parts that require very high surface accuracy, providing a smooth surface finish and high dimensional accuracy.
3. Applications of Machined Parts
Machined parts are widely used across various industries due to their precision and ability to be customized. From aerospace to consumer electronics, machining ensures the accuracy, performance, and reliability of components essential to each field.
Aerospace:
The aerospace industry relies heavily on high-precision machined parts. Critical components such as turbine assemblies and airframe connectors require exacting tolerances to ensure the safety and stability of aircraft operating at high altitudes.
Automotive Manufacturing:
Machined parts play a key role in automotive manufacturing, particularly in engine components, transmission systems, and other vital mechanical parts. The precision of these components ensures that vehicles operate reliably under demanding conditions.
Medical Devices:
In the medical field, surgical tools, prosthetic components, and implants depend on high precision and smooth surfaces. Machining processes can meet the stringent requirements for safety and durability in medical equipment.
Consumer Electronics:
Many core components in consumer electronics—such as smartphones, tablets, and smartwatches—are produced through machining. The technology enables the creation of complex, small parts while ensuring the performance and longevity of these devices in daily use.
4. Prototyping with Machined Parts
Prototypes are crucial tools in product development, used to validate the function and performance of a design. They play a key role in design evaluation, helping engineers identify issues and optimize the product, ensuring that the final version meets all necessary requirements and standards.
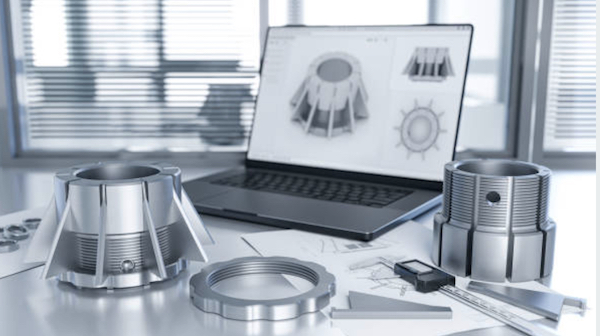
Advantages of Machined Prototypes:
Rapid Iteration: Machining allows for quick modifications and reproduction of prototypes when design changes occur. This flexibility enables design teams to swiftly test adjustments and further refine the product based on the results.
High Precision: Machined prototypes offer exceptional precision, ensuring that every design detail is fully realized. This accuracy is particularly important for complex structures or components that require tight tolerances, providing reliable design validation.
Cost Control: Compared to mass production, machining is more cost-effective for small-batch or single-unit manufacturing, especially in the early development stages. By controlling production costs, companies can develop and test prototypes without committing to large-scale manufacturing resources.
Get Your CNC Parts Into Production Today
Your Global Partner for Quality CNC Machining Services in China!
5. Machined Part Materials
Machined parts are made from a wide range of different materials to suit many different applications. The process is versatile and can work on a wide range of metals and plastics with excellent results. The following are some of the most commonly used materials.
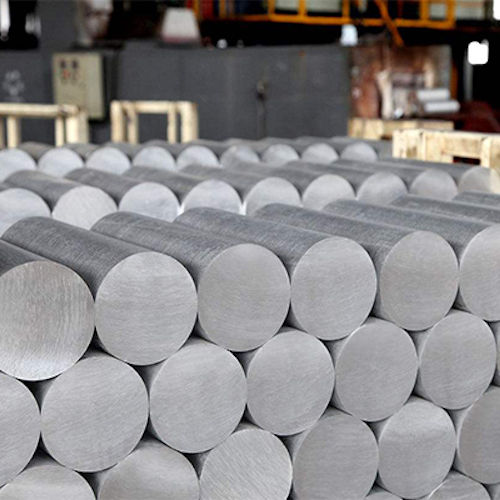
Metal Materials
Material | Properties | Application Areas |
---|---|---|
Stainless Steel | Corrosion-resistant, high strength | Medical, food processing industries |
Brass | Strong conductivity | Electronics, precision instruments |
Aluminum | Lightweight, good thermal conductivity | Automotive, aerospace |
Titanium | High temperature resistance, corrosion-resistant | Aerospace, medical implants |
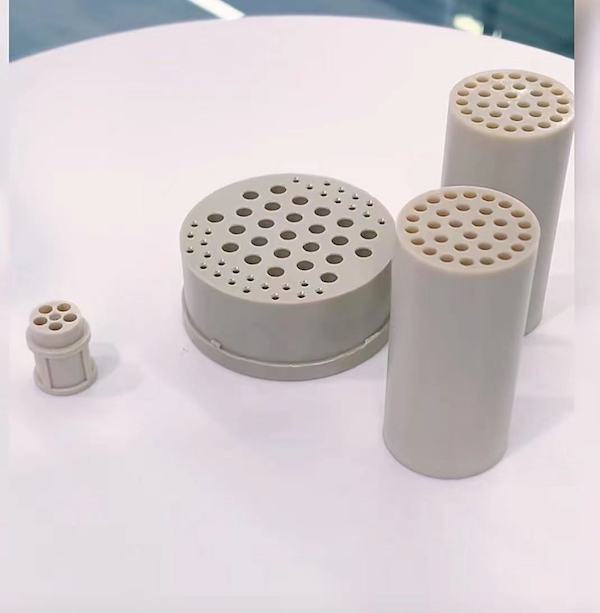
Plastic Materials
Material | Properties | Application Areas |
---|---|---|
PEEK | High strength, chemical resistance | Medical, electronics industries |
Nylon | Suitable for friction parts like gears and bearings | Gears, bearings |
PVC and ABS | Low cost, high strength | Consumer electronics housings |
6. Machined parts production process
Step 1: Technical Drawings
During the design phase, the customer provides detailed CAD drawings, specifying precision, tolerances, and surface finish requirements. These drawings form the foundation of the production process, ensuring that all design details are clear and accurate.Step 2: Prototype Development
Based on the drawings, a prototype of the product is developed to test and verify the design. The prototype helps identify potential issues and allows for necessary adjustments before full-scale production.Step 3: Technology Selection
The appropriate machining process is chosen based on the material and design requirements. Common processes include CNC milling, turning, and drilling, ensuring that the parts are machined with precision and efficiency.Step 4: Machining
In the production stage, CNC machines are used to remove material and manufacture parts according to the design specifications. The precise control offered by CNC technology ensures high-quality and consistent machining results.Step 5: Quality Control
After machining, strict quality checks are conducted, including dimensional measurements and surface inspections, to ensure that the finished product meets the required precision and appearance standards. These controls guarantee that each part conforms to the design specifications and performs as expected.
7. How to Choose the Right Machining Factory
Choosing the right machining factory is crucial for ensuring product quality and timely delivery. Look for a factory equipped with advanced CNC machines to guarantee precision and efficiency.
The factory should have experience working with a variety of materials, from metals to plastics, to meet different project requirements.
Strong quality control processes and necessary certifications are essential to ensure that parts meet industry standards.
Additionally, prioritize factories with excellent customer service and reliable global logistics, as timely communication and delivery are key to maintaining a successful partnership.
Choose RALLY for precision machining with advanced CNC technology and exceptional service. Contact us today for a custom solution tailored to your needs!
Work with RALLY for CNC Machining Parts
Request a quote for new project today! No minimum order quantity and free samples available!