Brass CNC Machining
Offers custom-made precision brass components for any application.
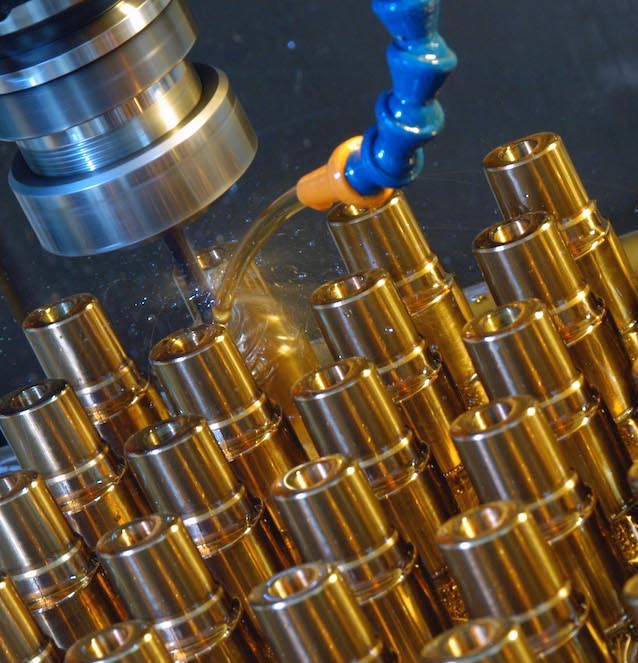
Expert Brass CNC Machining Service
RALLY offers robust brass CNC machining capabilities backed by extensive experience, delivering customized solutions tailored to your requirements. You can select from various brass grades to suit your specific needs.
Equipped with a range of advanced CNC machining center and CNC lathes, we are prepared to meet all your brass CNC machining demands, ensuring top-quality parts with quick turnaround times.
CNC Brass Machined Parts
Our facility offers a full range of CNC machining services focused on brass components. We work with top-grade brass C360, which is perfect for products requiring high strength, outstanding corrosion resistance, excellent electrical conductivity, and low friction. Our advanced equipment, including diverse CNC mills and turning centers, enables us to manufacture both simple, “as-machined” items and complex designs with strict tolerances. Clients can choose from up to six post-machining treatments such as sandblasting, powder coating, smooth finishing, and polishing to improve the appearance and performance of the final products.
- Bushing, Gear, Valve Body
- Heat Sinks, Nozzles
- Knobs and Handles
- Shaft Components
- Electrical Connectors
- Screws and Fasteners
- Fixtures and Fittings
- Pump and Compressor Parts
Brass Parts Manufacturer In China
As a leading brass parts manufacturer in China, we specialize in precision CNC machining to produce high quality brass parts. Our expertise spans a wide range of industries, including automotive, aerospace, and electronics, where the need for durable and precision parts is critical. We utilize advanced CNC technology and a variety of brass alloys, such as C36000 and C38500, to produce functional and aesthetically pleasing parts.
Our machining capabilities include turning, milling, and drilling to handle projects ranging from simple to complex geometries. We also offer a variety of finishing options, such as plating and polishing, to enhance the durability and appearance of your products. Our commitment to quality and customer satisfaction ensures that we meet specific industry standards and customer expectations.
Brass CNC Machining Processes
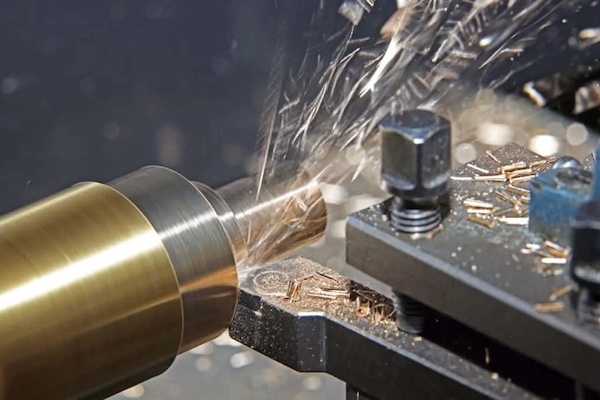
Brass Turning for Cylindrical Parts
Turning turns brass into precision cylindrical parts, ideal for applications requiring smooth surfaces and tight tolerances, such as shafts and bushings.
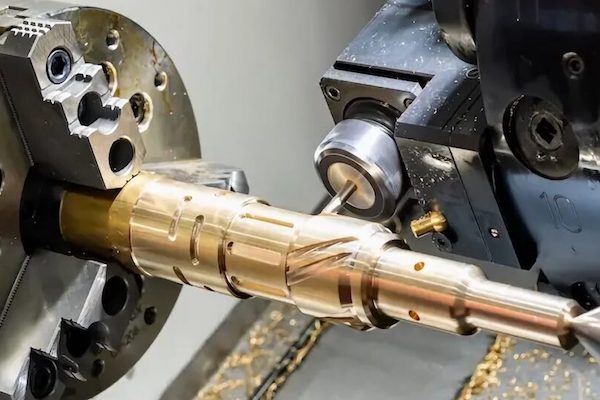
Brass Milling for Complex Features
Complex features including slots, contours and intricate geometries are machined into components to produce parts with unique shapes and fine features.
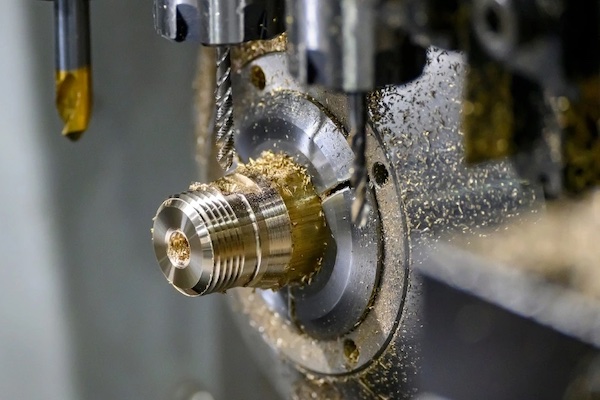
Brass Drilling for Holes
Drilling in brass machining focuses on producing accurate, clean holes, which is critical for parts that require precise hole sizes and locations, such as nozzles and connectors.
CNC Brass Parts We Offer
Explore our showcase of CNC machined brass parts, where precision meets craftsmanship. Our product display features a variety of components crafted from high-quality brass, each tailored to meet specific industry standards.
Connector Part
Choke Flange
Brass Flange
Connector Part
Brass Flange
Brass Parts
Module Body
Square Flange
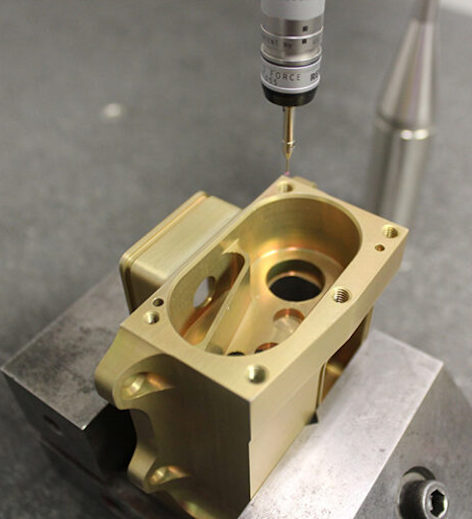
QUALITY INSPECTION
At RALLY, we hold every machining operation to exacting tolerances. Our factories are equipped with state-of-the-art inspection tools and precision measuring equipment to ensure top-notch quality control of all CNC machined parts. Parts are randomly inspected throughout the production process and fully evaluated by our quality assurance team upon completion.
Our comprehensive quality assurance protocols include the use of Coordinate Measuring Machines (CMMs), Optical Comparators and Surface Roughness Testers. In addition, all tools, equipment and components are calibrated and documented according to ISO 9001:2015 standards.
Get a Quick Quote for Free Samples
Request a quick quote now and receive free samples of our precision CNC machining parts tailored to your specifications!
Why Use Our Brass Machining Service
Perfect Precision
Offering 3, 4, and 5-axis CNC machining with tight tolerances up to ±0.01mm.
Free Samples
Provide free samples before mass production to ensure that your requirements are met.
Fast Turnaround
Sample production in 3-5 days, with bulk orders completed within 10-20 days.
Extensive Material Options
Capable of machining in over 100+ different metal and plastic materials.
Unlimited Capabilities
No restrictions on the size, speed, or complexity of parts.
Proven Experience
More than 20 years in the industry, with CNC operators averaging 10 years of expertise.
FAQ for Brass Machining
1. What is the machining accuracy range of brass?
2. What types of machining processes are suitable for brass?
3. What are the typical applications of brass machined parts?
4. How do you ensure the quality of brass machined parts?
5. Can you handle small batch production orders?
6. What is the standard lead time for brass machining orders?
7. What surface treatments are available for brass parts?
8. Do you provide technical support during the design and production process?
Get in Touch
Ready to get started? Contact us today for a free quote!
Metal Material
Aluminum, Brass, Stainless Steel, Carbon Steel, Copper, Titanium, etc.
Plastic Material
Acetal (Delrin), PTFE (Teflon), Acrylic (PMMA), PEEK, Nylon, ABS, PC, PP, POM, HDPE, PVC.
Surface Finishing
Anodizing, Powder Coating, Plating, Passivation, Bead Basting, Polishing, etc.
Inquiry Form
Let’s Start A New Project Today, Get Free Samples!
All You Need To Know About Brass Machining
Table of Contents
CNC Machining Brass Materials
Brass is a popular material for CNC machining due to its machinability, aesthetic appeal, and corrosion resistance.
Here are some common brass grades frequently used in CNC machining, each chosen for their unique properties and suitability for different applications:
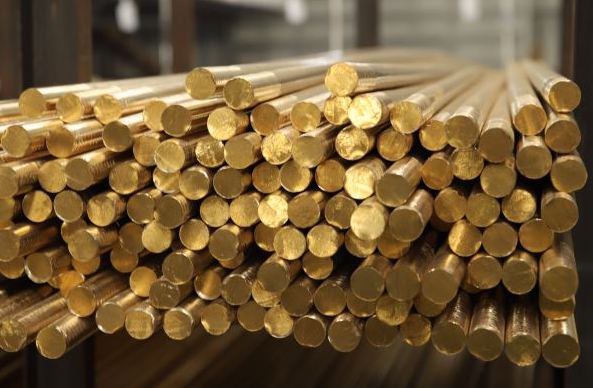
Material Name | Key Characteristics | Applications |
---|---|---|
C28000 (Brass 59) | Excellent machinability, suitable for hot and cold working | Plumbing fittings, nuts, bolts, mechanical parts |
C27200 (Brass 62) | Good strength and corrosion resistance, excellent conductivity | Pipeline equipment, automotive parts, instruments |
C26800 (Brass 65) | Good ductility and wear resistance, suitable for cold working | Electronic components, connectors, decorative parts |
C26000 (Cartridge Brass) | Excellent corrosion resistance and plasticity, superior thermal conductivity | Precision instruments, heat exchangers, cartridge cases |
C36000 (Free-Cutting Brass) | Outstanding machinability, ideal for high-precision machining | Valves, gears, bushings, electrical components |
C37700 (Forging Brass) | Suitable for hot forging, high corrosion resistance | Pipe fittings, valve bodies, connectors, pump components |
C38500 (Architectural Brass) | Excellent formability and corrosion resistance | Architectural decorations, locks, handrails, light fixtures |
Is brass easier to machine than aluminum?
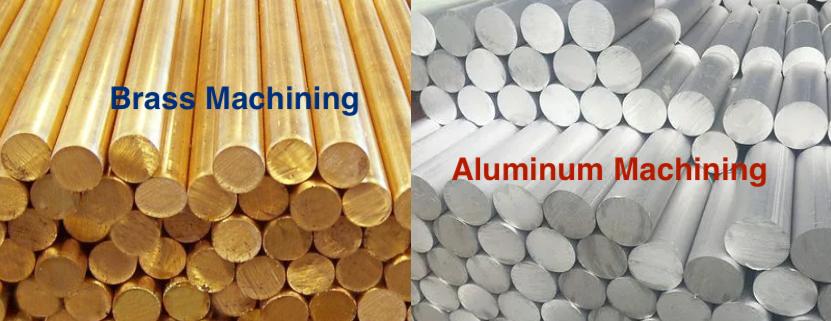
Brass and aluminum are both popular materials in machining due to their excellent machinability, but each has distinct properties that affect the ease of machining. In general, brass is considered easier to machine than aluminum for several reasons.
One key factor is that brass produces small, manageable chips during machining, reducing the risk of tool clogging. This allows for more efficient cutting, even with complex geometries. Additionally, brass causes minimal tool wear compared to aluminum, making it ideal for precision parts and minimizing downtime for tool maintenance. Brass also provides superior surface finishes right off the machine, often eliminating the need for extensive post-processing or polishing.
In comparison, aluminum is softer and more prone to chip adhesion, which can lead to tool clogging, especially during high-speed machining. While aluminum can be machined quickly due to its lightweight nature, it often requires more cooling to avoid heat buildup. Additionally, achieving a premium surface finish with aluminum may require anodizing or polishing.
However, aluminum has advantages in applications that prioritize weight reduction and cost efficiency, such as aerospace or automotive industries. While brass is easier to machine overall, the choice between these materials depends on the project’s specific requirements. If precision, tool longevity, and smooth finishes are essential, brass is likely the better option. For lightweight parts and rapid prototyping, aluminum may be more suitable.
Commonly Machined Brass Parts
Brass is a highly machinable material, making it a preferred choice for various industries. Below are some commonly machined brass parts along with their applications:
Brass Parts | Applications | Industries |
---|---|---|
Bushings | Reduces friction between rotating parts | Automotive, Machinery, Robotics, Marine |
Gears | Used in low-load mechanical systems for smooth operation | Clocks, Appliances, Precision Instruments |
Valve Bodies | Controls flow and pressure in plumbing and fluid systems | HVAC, Plumbing, Marine, Chemical Processing |
Heat Sinks | Dissipates heat efficiently in electronic systems | Electronics, Telecommunications, Power Systems |
Nozzles | Provides precision control of fluid or gas flow | Spraying Equipment, Firefighting, Fuel Systems |
Knobs and Handles | Offers durability, corrosion resistance, and aesthetics | Furniture, Musical Instruments, Machinery |
Shaft Components | Transmits torque between motors and equipment | Automotive, Robotics, Machinery |
Electrical Connectors and Terminals | Ensures reliable electrical connections | Telecommunications, Automotive, Electronics |
Screws and Fasteners | Provides corrosion-resistant fastening solutions | Electrical Assemblies, Marine, Aerospace |
Pump and Compressor Parts | Ensures smooth operation in fluid systems | Oil & Gas, Marine, HVAC |
Fixtures and Fittings | Secures connections in plumbing and gas pipelines | Plumbing, Gas Distribution, Construction |
What are the Differences Between Brass Machining and Other Metal Machining?
Category | Brass | Aluminum | Stainless Steel |
---|---|---|---|
Machinability | Excellent machinability, fast cutting, minimal tool wear | Easy to machine but may need coatings for corrosion resistance | Hard to machine, higher tool wear, requires specialized tools |
Corrosion Resistance | Naturally resistant to water corrosion, ideal for marine and plumbing | Good corrosion resistance, needs anodizing for durability | Excellent resistance, suitable for harsh environments |
Electrical & Thermal Conductivity | High conductivity, used in connectors and heat exchangers | Good conductivity, but less than brass | Low conductivity, limited use in electrical applications |
Strength & Durability | Balanced strength and flexibility, wear-resistant | Lightweight but less strong than brass | Highly durable and strong, suitable for heavy-duty applications |
Surface Finish | Smooth, polished finish easily achievable | Requires anodizing or polishing for better finish | Can be polished but requires more effort than brass |
What types of brass are best for CNC machining?
Several brass alloys are ideal for CNC machining due to their excellent machinability and diverse properties. C360 brass (free-cutting brass) is the top choice, known for its superior machinability, smooth finishes, and reduced tool wear, making it perfect for precision parts like gears and connectors. C385 brass (architectural brass) offers good machinability with a decorative appearance, ideal for knobs and fittings.
For applications requiring corrosion resistance, C230 brass (red brass) performs well in plumbing and marine environments, while C464 brass (naval brass) is suited for harsh saltwater conditions. C280 brass (Muntz metal) provides strength and wear resistance, making it suitable for mechanical components.
Each alloy caters to specific needs, from decorative parts to marine applications, ensuring reliable performance in CNC machining projects.
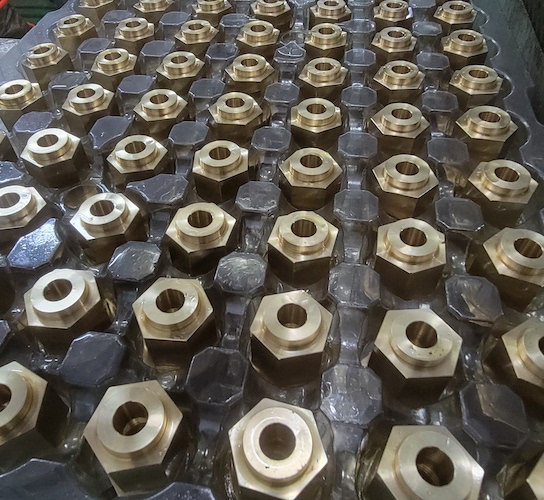
Surface Treatment Processes for Brass Machined Parts
Brass components often require surface treatments to enhance their performance, durability, and appearance. Each process offers specific benefits such as corrosion resistance, improved aesthetics, or enhanced wear protection.
The following table provides a detailed overview of common surface treatment techniques for brass machined parts.
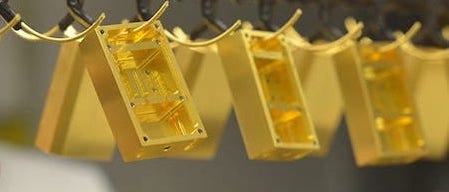
Process | Steps | Application |
---|---|---|
Electroplating | 1. Cleaning: Ultrasonic cleaning or acid wash 2. Activation: Apply chemical solution 3. Plating: Submerge in electrolyte bath (e.g., nickel, chrome, gold) 4. Rinsing & Drying | Used in electrical connectors, decorative parts, and valves |
Polishing | 1. Grinding: Remove machining marks with coarse abrasives 2. Polishing: Use finer abrasives for smoother surfaces 3. Buffing: Final shine with soft cloth wheels | Common for handles, fittings, and decorative components |
Anodizing | 1. Cleaning & Etching: Prepare surface with acid solutions 2. Oxidation: Create controlled oxide layer 3. Dyeing/Sealing: Add color or seal for durability (optional) | Suitable for aesthetic components and specialized finishes |
Powder Coating | 1. Pre-treatment: Clean and etch surface 2. Powder Application: Spray electrostatic powder evenly 3. Curing: Bake in oven to solidify coating | Ideal for industrial and decorative applications |
Passivation | 1. Cleaning: Remove contaminants from the surface 2. Chemical Treatment: Submerge in passivation solution (e.g., citric acid) 3. Rinsing & Drying: Thorough rinse and drying to prevent residue | Used for components exposed to moisture or harsh environments |
What are the Key Processes for CNC Machining Brass?
CNC Turning of Brass
CNC turning is ideal for creating cylindrical components like bushings, shafts, and connectors. Here are the key technical requirements for brass turning:
- Tool Selection: Use carbide or high-speed steel tools with sharp cutting edges to maintain precision and prevent burrs.
- Cutting Speed: Brass allows for higher cutting speeds (up to 200-300 meters/min) due to its excellent machinability.
- Feed Rate: A moderate feed rate (0.1-0.3 mm/rev) ensures smooth surfaces without compromising tool life.
- Coolant Usage: Brass machining does not require heavy coolant since the material dissipates heat effectively, but light lubrication can improve surface finish.
- Chip Control: Brass produces small, easy-to-handle chips, reducing downtime for chip removal.
Applications: CNC turned brass parts include bushings, electrical connectors, valve bodies, fasteners, and pump parts.
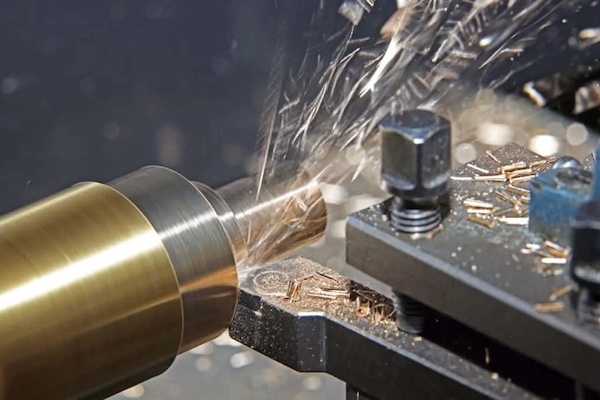
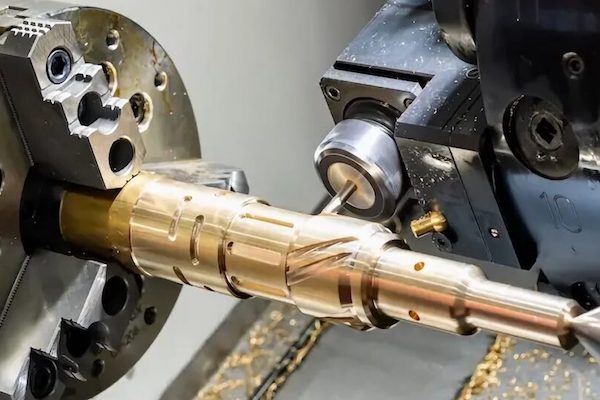
CNC Milling of Brass
CNC milling is used to create complex shapes, pockets, and features with high precision. Here are the technical aspects to ensure optimal brass milling:
- Cutting Tools: Carbide end mills with sharp cutting edges provide excellent results. For high precision, smaller-diameter tools may be used for intricate features.
- Spindle Speed: High spindle speeds (8,000–12,000 RPM) improve cutting efficiency and surface finish when milling brass.
- Feed Rate and Depth of Cut: A balanced feed rate (0.1–0.2 mm per tooth) and a moderate depth of cut help prevent tool deflection and ensure smooth machining.
- Workholding: Brass parts require secure clamping to prevent movement and maintain tight tolerances during machining.
- Surface Finish Optimization: Light finishing passes are often used to achieve smooth surfaces, minimizing the need for post-processing.
Applications: CNC milled brass parts include heat sinks, manifolds, gears, housings, and decorative components.
Work with RALLY for Brass Machining
Request a quote for new project today! No minimum order quantity and free samples available!