CNC Aluminum Parts
Precision Aluminum Parts Manufactured According to Your Drawings
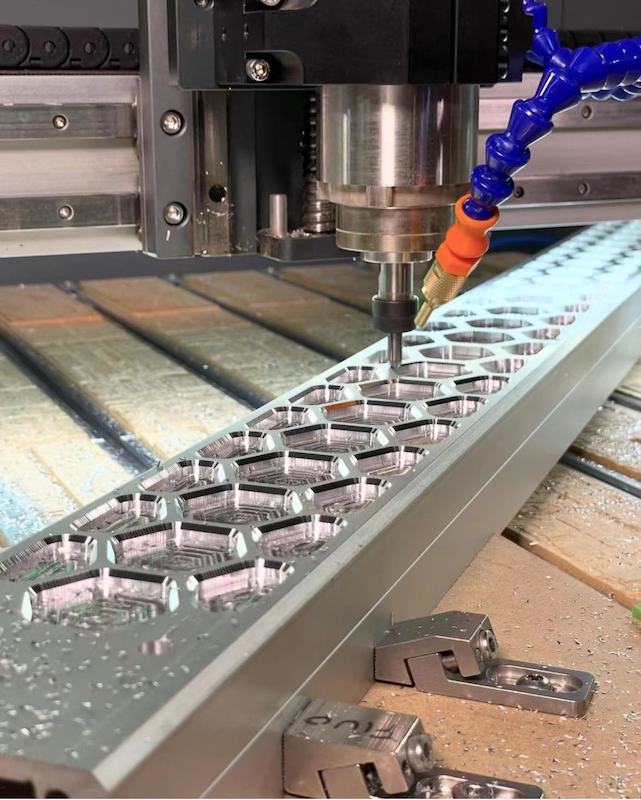
Custom CNC Aluminum Machined Parts
RALLY specializes in custom CNC aluminum parts, providing tailored solutions to meet a variety of industrial requirements. Utilizing advanced CNC technology, we are skilled at crafting components from aluminum-a material known for its light weight, strength, and resistance to corrosion. Our custom machining services are ideally suited for industries ranging from aerospace to consumer electronics, where precision and reliability are critical.
At RALLY, we understand that every project is unique. That’s why we offer customized services to fit your specific needs, whether you require complex geometries, mass production, or one-off prototypes. Our commitment to quality and precision ensures that every part we produce meets the highest standards, helping to improve the performance and reliability of your product.
CNC Aluminum Parts We Offer
At RALLY, we offer a wide range of CNC aluminum parts, including custom components for aerospace, automotive, and electronics. Our state-of-the-art CNC technology ensures precision, durability, and a perfect fit for any project requirement.
Camera Lock Finger Grip
Quick Release Plate
Mounting Frame
Waveguide Component
Aluminum Air Inlet Flange
6061 Aluminum Hinge
Aluminum Waveguide Shim
Waveguide Choke Flange
Electronic Enclosure
CNC Aluminum Enclosure
CNC Aluminum Bike Stem
CNC Bicycle Aluminum Parts
CNC Aluminum Prototype
RALLY specializes in manufacturing high-quality CNC aluminum prototypes that utilize the versatile properties of aluminum to meet the demanding requirements of a wide range of industries. Utilizing state-of-the-art CNC machining technology, your design concepts are quickly and accurately transformed into practical, functional prototypes.
Whether it’s automotive, aerospace, or consumer electronics, RALLY’s prototypes help bridge the gap between initial design and mass production for comprehensive testing and design optimization.RALLY is committed to providing not only fast turnaround times, but also high-precision prototypes to ensure that every product meets stringent quality standards.
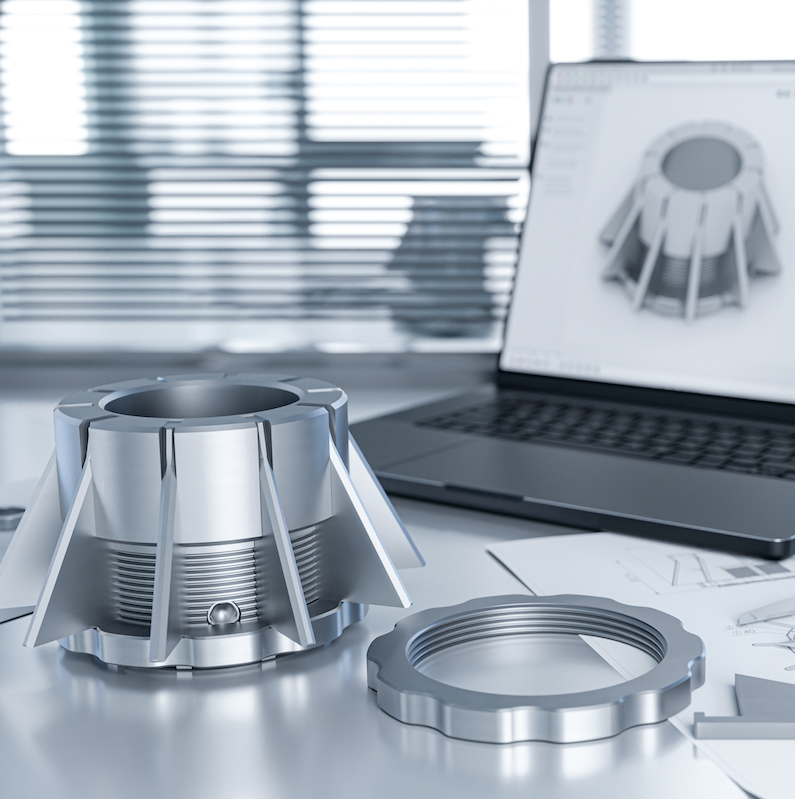
Get a Quick Quote for Free Samples
Request a quick quote now and receive free samples of our precision CNC aluminum parts tailored to your specifications!
6061 Aluminum Alloys Material Characteristics
6061 aluminum alloy is one of the widely used aluminum alloys, its characteristics include:
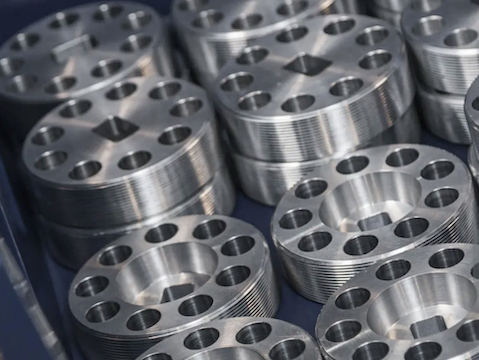
Excellent mechanical properties:
– 6061 aluminum alloy has good strength and hardness, especially after heat treatment (e.g. T6 treatment).
Good machinability:
– The alloy has good cutting performance and can be precision machined by CNC machining, which is suitable for manufacturing complex parts.
Excellent corrosion resistance:
– 6061 aluminum alloy has excellent corrosion resistance to atmosphere and water, so it is widely used in outdoor and marine environments.
Good welding properties:
– 6061 aluminum alloy can be welded by a variety of welding methods, and the strength and performance after welding are relatively stable.
Good formability:
– The alloy has good plasticity in the annealed state and can be formed and processed by extrusion, stretching and stamping.
Lightweight:
– Aluminum alloys have low densities, and 6061 aluminum alloy is no exception. Its light weight makes it suitable for application scenarios where weight reduction is required, such as the aerospace and automotive industries.
Heat Resistance:
– 6061 aluminum alloy can maintain certain mechanical properties at high temperatures, making it suitable for certain high-temperature applications.
What are the mechanical properties of CNC aluminum alloys?
CNC aluminum alloys have excellent mechanical properties and are widely used in a variety of industrial applications. Its main advantages include high strength, light weight and excellent corrosion resistance. Aluminum alloys are often enhanced by the addition of elements such as copper, magnesium and zinc to increase their strength and hardness, while maintaining good machinability and toughness.
Aluminum alloys exhibit excellent machinability during CNC machining, enabling the manufacture of parts with high precision and complex geometries. 6061 aluminum alloy is one of the most commonly used alloys, with medium strength and excellent fatigue resistance, making it ideal for use in aerospace, automotive, and electronic equipment.
Additionally, aluminum alloys have excellent thermal performance, making them suitable for applications that require high thermal conductivity, such as heat sinks and electronic device housings. Overall, CNC aluminum alloys are important materials in industrial manufacturing for their efficient machining characteristics and excellent mechanical properties.
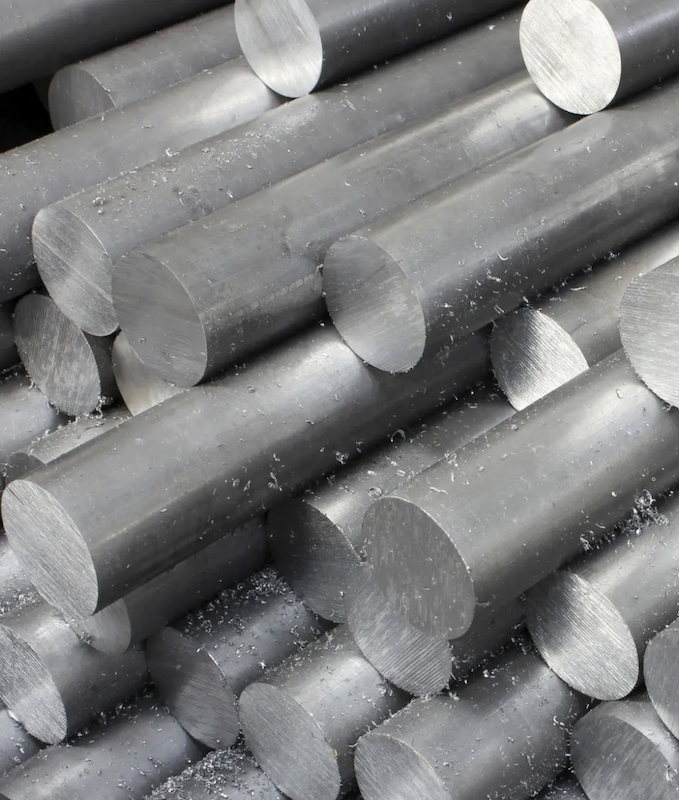
What is the difference between 6061 and 7075 types of aluminum alloys?
6061 Aluminum Alloy
- Composition: 6061 aluminum alloy contains mainly magnesium and silicon, giving it good overall performance.
- Strength: 6061 aluminum alloy has medium strength, making it suitable for applications that require some strength but not extremely high strength.
- Corrosion resistance: 6061 aluminum alloy has excellent corrosion resistance and is suitable for parts exposed to wet or corrosive environments.
- Machinability: 6061 aluminum alloy has excellent machinability and is easy to CNC machine, weld and form.
- Applications: Commonly used in structural engineering, aerospace, automotive industry and consumer electronics such as radiators and mechanical components.
7075 Aluminum Alloy
- Composition: Aluminum alloy 7075 is alloyed with zinc as the primary alloying element and contains small amounts of magnesium and copper to provide extremely high strength.
- Strength: 7075 Aluminum Alloy is one of the strongest aluminum alloys, offering very high strength and hardness for high stress environments.
- Corrosion Resistance: 7075 aluminum alloy has poor corrosion resistance and requires protective treatments when exposed to corrosive environments.
- Machinability: The machinability of 7075 aluminum alloy is relatively poor, but excellent mechanical properties can be obtained through precision machining and heat treatment.
- Applications: Widely used in aerospace, military equipment, high-performance bicycles and racing car parts where extremely high strength is required, such as aircraft structural components, high-pressure valves and sports equipment.
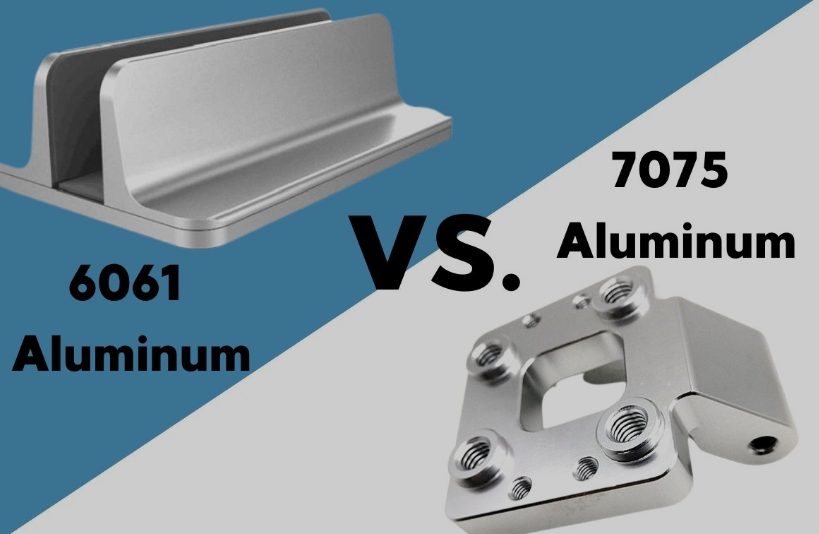
Properties of aluminum alloy 6061:
Chemical Composition
– Aluminum (Al): 95.8 – 98.6%
– Magnesium (Mg): 0.8 – 1.2%
– Silicon (Si): 0.4 – 0.8%
– Copper (Cu): 0.15 – 0.4%
– Chromium (Cr): 0.04 – 0.35%
– Other minor elements like iron, manganese, titanium, zinc
Physical Properties
– Density: 2.7 g/cm³ (0.098 lb/in³)
– Melting Point: 582 – 652°C (1080 – 1205°F)
– Thermal Conductivity: 151 – 167 W/m-K (1050 – 1160 BTU-in/hr-ft²-°F)
– Electrical Conductivity: 37% IACS
– Coefficient of Thermal Expansion: 23.6 μm/m-°C (13.1 μin/in-°F)
The mechanical properties vary based on the temper designation:
6061-O (Annealed)
– Tensile Strength: 125 MPa (18 ksi)
– Yield Strength: 55 MPa (8 ksi)
– Elongation: 25%
6061-T4 (Naturally Aged)
– Tensile Strength: 241 MPa (35 ksi)
– Yield Strength: 145 MPa (21 ksi)
– Elongation: 22%
6061-T6 (Artificially Aged)
– Tensile Strength: 310 MPa (45 ksi)
– Yield Strength: 276 MPa (40 ksi)
– Elongation: 12%
Other Properties:
– Shear Strength: 207 MPa (30 ksi)
– Fatigue Strength: 96.5 MPa (14 ksi)
– Hardness (Brinell): 95
– Modulus of Elasticity: 68.9 GPa (10,000 ksi)
Properties of aluminum alloy 7075:
Chemical Composition
– Zinc (Zn): 5.1 – 6.1%
– Magnesium (Mg): 2.1 – 2.9%
– Copper (Cu): 1.2 – 2.0%
– Chromium (Cr): 0.18 – 0.28%
– Iron (Fe): Max 0.5%
– Silicon (Si): Max 0.4%
– Manganese (Mn): Max 0.3%
– Titanium (Ti): Max 0.2%
– Other minor elements like lead, bismuth, etc.
Physical Properties
– Density: 2.81 g/cm³ (0.102 lb/in³)
– Melting Range: 477 – 635°C (891 – 1175°F)
– Thermal Conductivity: 130 – 173 W/m-K (900 – 1200 BTU-in/hr-ft²-°F)
– Coefficient of Thermal Expansion: 23.4 μm/m-°C (13.0 μin/in-°F)
– Electrical Resistivity: 51.5 nΩ.m
The mechanical properties vary significantly based on the temper designation:
7075-O (Annealed)
– Tensile Strength: 228 MPa (33 ksi)
– Yield Strength: 103 MPa (15 ksi)
– Elongation: 16%
7075-T6 (Solution Heat Treated and Artificially Aged)
– Tensile Strength: 572 MPa (83 ksi)
– Yield Strength: 503 MPa (73 ksi)
– Elongation: 11%
– Shear Strength: 331 MPa (48 ksi)
– Hardness: 87 HRB
7075-T73 (Overaged)
– Tensile Strength: 505 MPa (73.2 ksi)
– Yield Strength: 435 MPa (63.1 ksi)
What are the applications of aluminum parts in automotive, aerospace and electronics?
Automotive Industry
Engine components:
- Cylinder head: Aluminum’s light weight and heat dissipation properties make it an ideal material for cylinder heads.
- Pistons: Aluminum pistons offer excellent strength and heat resistance.
- Radiator: Aluminum radiator tubes and fins improve heat dissipation efficiency.
Body and chassis components:
- Door Frame: Aluminum’s light weight helps reduce the weight of the doors and improves fuel economy.
- Suspension Parts: Aluminum suspension arms and mounts reduce weight while providing strength.
- Wheels: Aluminum wheels are lighter than conventional steel wheels, reducing unsuspended mass and improving handling.
Aerospace Industry
Structural parts:
- Wings: aluminum alloy wing structure provides high strength and light weight.
- Fuselage Frame: Aluminum frame provides the backbone of the aircraft structure, ensuring strength and durability.
- Support beams: Aluminum alloy support beams reduce weight while providing support.
Precision Parts:
- Aircraft engine components: such as turbine blades and compressor housings, aluminum’s high strength-to-weight ratio allows it to perform well in high-stress environments.
- Fuel system components: Aluminum alloys are used in fuel tanks and piping for corrosion resistance and light weight.
- Hydraulic system components: Aluminum for hydraulic cylinder blocks and valve blocks, ensuring reliability and durability under high pressure.
Electronics Industry
Enclosure:
- Laptops: Aluminum enclosures offer the perfect combination of lightweight and durability with excellent heat dissipation.
- Tablets: Aluminum housings are both attractive and robust, enhancing the overall structural strength of the device.
- Smartphones: Aluminum housings and frames provide superior feel and heat dissipation.
Heat dissipation components:
- Heat sinks: Heat sinks for laptops, desktop computers and servers effectively improve heat dissipation efficiency.
- Cooling Plate: Used in cooling systems for high-performance electronic devices, aluminum cooling plates have good thermal conductivity.
- Thermal Conductive Base: Aluminum alloy thermal conductive base is used for high power LED lamps and provides a reliable thermal solution.
Internal Components:
- Capacitor Housings: Aluminum housings protect electronic components and provide electromagnetic shielding.
- Connectors: Aluminum connectors provide high conductivity while reducing device weight.
- Brackets and Fixtures: Aluminum brackets and fixtures are used to secure and support internal circuit boards and components.
Which CNC machining techniques are suitable for aluminum alloys?
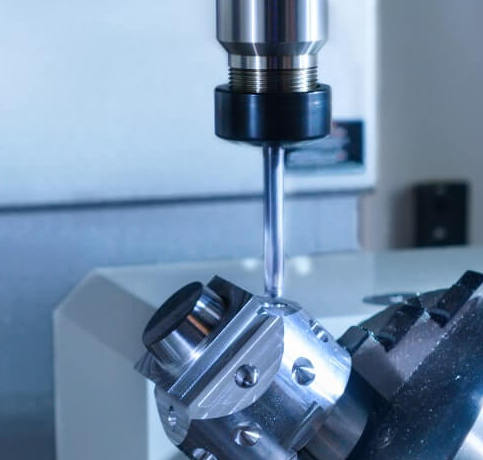
CNC Milling
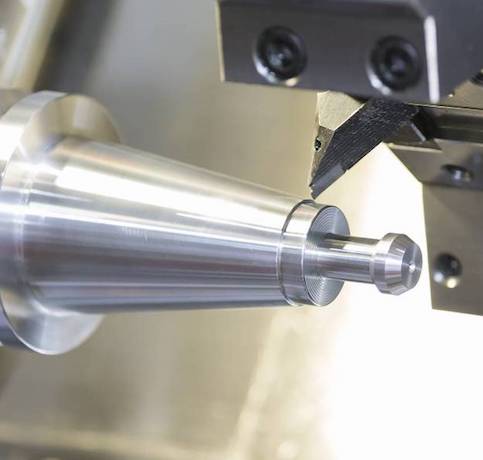
CNC Turning
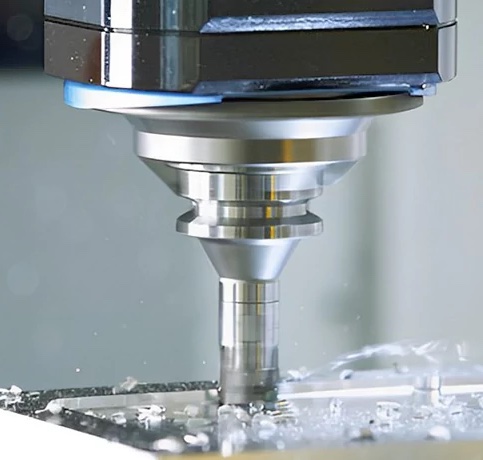
CNC Drilling
Tolerances of CNC aluminum parts
CNC machining of aluminum alloy components can be achieved with high precision, with tolerance levels that usually depend on the specific machining process and the capabilities of the equipment.
Conventional tolerances are typically between ±0.05mm and ±0.1mm. This level of tolerance is suitable for most industrial applications such as machine parts, brackets and housings.
This level of tolerance meets the accuracy requirements of most application scenarios while maintaining reasonable production costs and machining efficiencies. For many mechanical and structural components, this tolerance is sufficient for proper function and assembly of the part.
High precision tolerances range from ±0.01mm to ±0.05mm. These types of tolerances are used for parts that require higher accuracy, such as components for aerospace, medical equipment and high precision instruments. In these applications, the accuracy of the part directly affects the performance and reliability of the equipment.
For example, aircraft engine components, medical implants and high-precision measuring instruments all require high-precision tolerances to ensure consistent and reliable performance under demanding conditions.
Ultra-high precision tolerances can reach ±0.005mm or even less. This level of tolerance is often used in special applications such as precision instruments, moulds and demanding research equipment. Ultra-high precision tolerances ensure that parts remain extremely accurate and consistent under extreme conditions.
For example, in semiconductor manufacturing equipment, optical instruments and scientific research projects, extremely tight tolerances are required on parts to ensure accuracy and repeatability in experimental and production processes.
Surface finish of CNC aluminum parts
The surface finish (Ra value, indicating surface roughness) of CNC aluminum alloy parts can reach a high level to meet the surface quality requirements of different applications. Surface finish is an important indicator of the smoothness of the machined surface, which directly affects the function, aesthetics and performance of the part.
Conventional surface finishes have Ra values between 1.6 and 3.2 microns. This level is suitable for most industrial applications and ensures that the surface of the part is sufficiently smooth, but extreme finishes are not required.
This type of surface finish is suitable for general purpose parts such as machine parts, brackets and housings. Conventional finish machining is less expensive and more efficient for most industrial production needs.
High surface finish with Ra values between 0.8 and 1.6 microns. It is suitable for parts that require better surface quality, such as automotive parts, aerospace components and some consumer electronics. This surface finish can significantly improve the look and feel of a part while reducing friction and wear.
For example, in the automotive industry, high finish engine components and interior trim not only improve vehicle performance, but also enhance aesthetics and the user experience. In the aerospace industry, high surface finishes help to reduce air drag and improve fuel efficiency and flight performance.
Ultra-high surface finishes can have Ra values of 0.2 to 0.8 microns or even less. This type of surface finish is suitable for parts with high precision and aesthetic requirements, such as optical instruments, medical devices and high-end consumer electronics housings. Ultra-high surface finishes ensure that parts maintain optimal performance in rigorous operating environments.
In medical devices, the surface finish of implants and surgical instruments directly impacts their safety and effectiveness. In consumer electronics, such as smartphones and laptops, high finish aluminum alloy housings not only enhance the look and feel of the product, but also increase durability and heat dissipation.
How do CNC aluminum parts ensure quality control during machining?
In order to ensure the quality control of CNC aluminum alloy parts in the machining process, it is crucial to take the following key measures:
1. Raw material selection and inspection: Detailed physical and chemical property inspections are carried out before the material enters production.
2. Precise machining equipment: High-precision CNC machines are used for machining. These machines are able to accurately control cutting parameters, such as speed, feed rate, and depth of cut, to reduce machining errors and improve the consistency and accuracy of components.
3. Advanced software applications: Utilising the latest computer-aided design (CAD) and computer-aided manufacturing (CAM) software ensures component design accuracy from the design stage.
4. Strict production process management: Detailed production work instructions and quality control procedures are developed to ensure that every step of the operation is carried out according to standards, thus reducing human error and process variation.
5. Periodic quality inspection: Conduct regular inspections at key stages of the machining process, including tests on dimensional accuracy, surface finish and mechanical properties. Precision measuring tools and equipment, such as CMMs and hardness testers, are used to ensure that each part meets technical specifications.
Through the above measures, the machining quality of CNC aluminum alloy parts can be effectively controlled to ensure that the final products can meet or even exceed customers’ expectations.
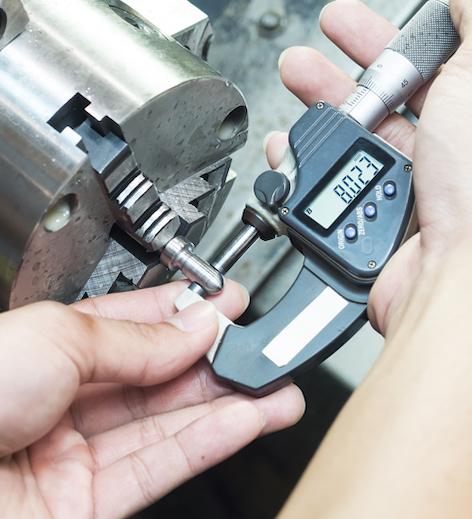
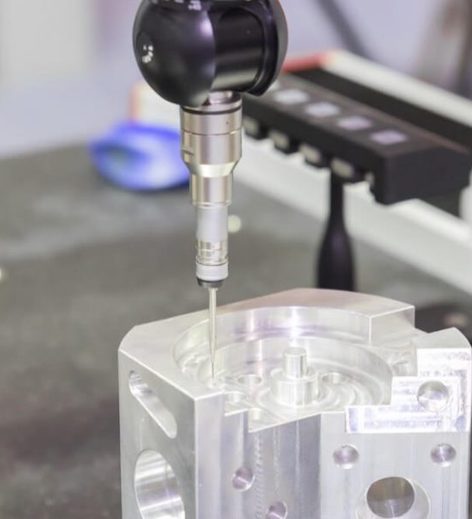
What are the surface treatments for CNC machining aluminium parts?
There are a variety of options for surface treatments for CNC machined aluminum parts that enhance the aesthetics, corrosion resistance, wear resistance and functionality of the part. The following are some common surface treatments:
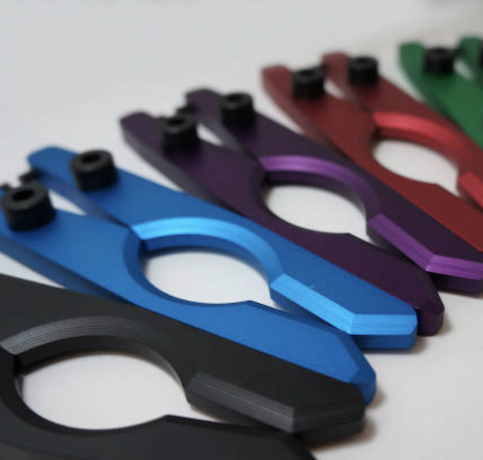
Anodizing
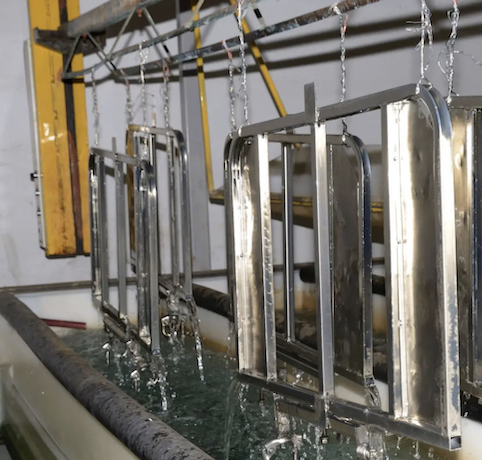
Electroplating
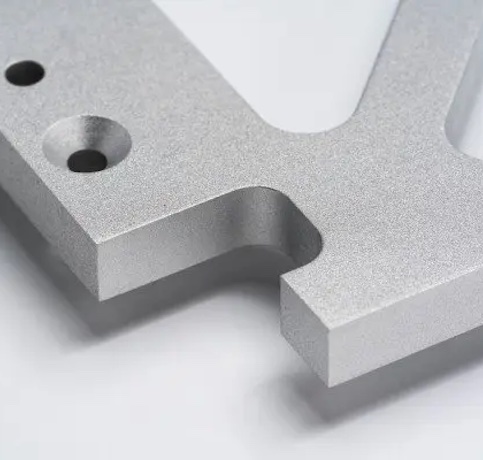
Sandblasting
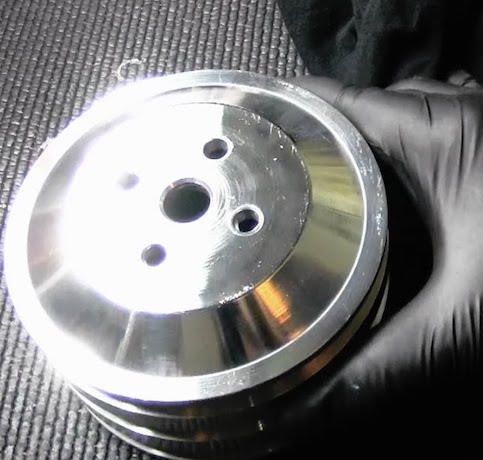
Polishing
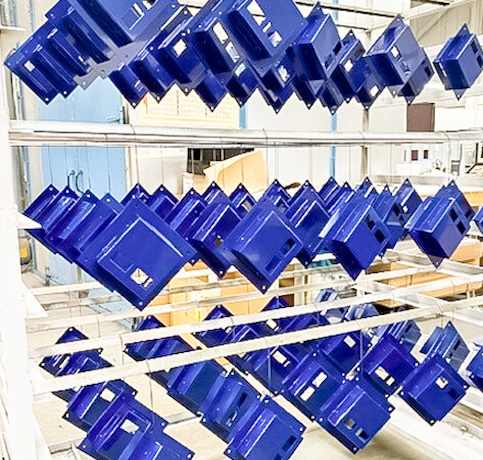
Coating
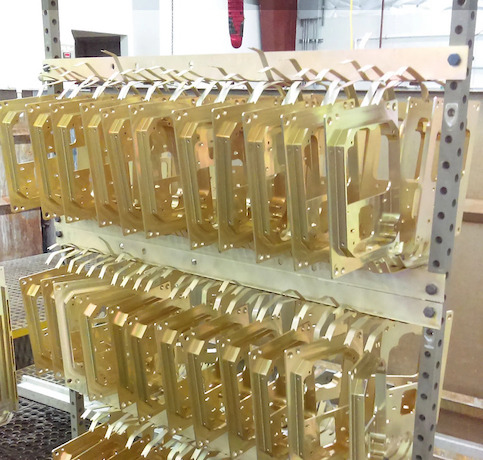
Chemical Conversion Coating
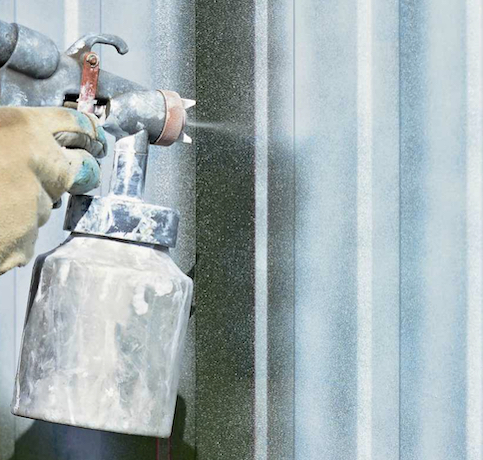
Painting
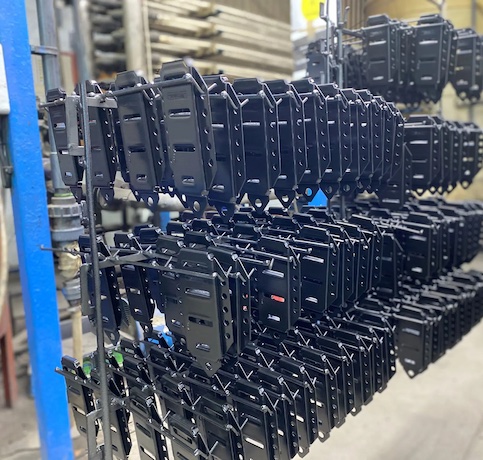
Electrophoretic Coating
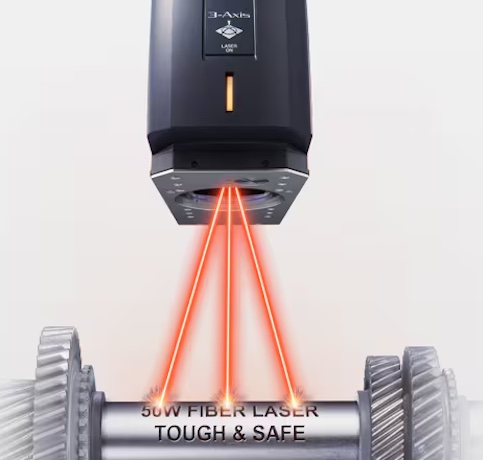
Laser Marking
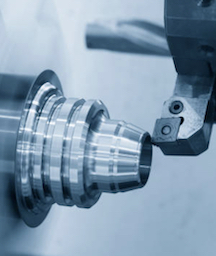
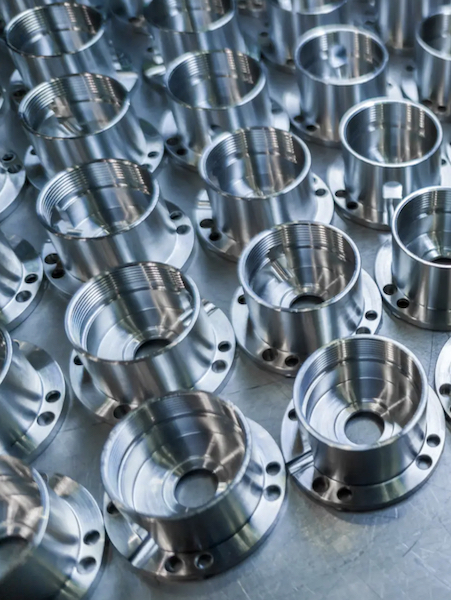
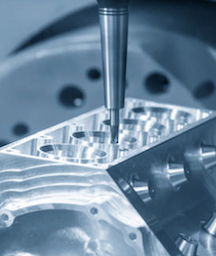
Does CNC aluminum alloy parts support custom production?
CNC aluminium alloy parts support custom production
CNC aluminum alloy parts are fully supported by customised production. the high degree of flexibility and precision of CNC (Computer Numerical Control) technology makes it possible to manufacture according to technical drawings and specifications provided by the customer. This means that whether it is a simple geometry or a complex 3D structure, CNC machining can be adapted to meet the individual needs of the customer.
Flexible mass production
Custom production of CNC aluminium alloy parts is not limited to single piece or small batch manufacturing, but is also suitable for high volume production.CNC machining allows for rapid adjustment of production schedules to meet urgent customer needs while maintaining high consistency and repeatability. This flexibility makes CNC machining ideal for prototyping, low-volume production and mass manufacturing.
High precision and surface finish
Custom-produced CNC aluminum alloy parts can be machined to high precision, with tolerances ranging from ±0.01mm or less. In terms of surface finishes, CNC machining supports a variety of processes such as anodising, electroplating, sandblasting and polishing to further enhance the appearance and performance of the part.
How to choose a reliable CNC aluminum machining supplier?
Choosing a reliable CNC aluminum machining supplier is critical to ensuring the quality and performance of the final product. Here are six key factors to consider when selecting a supplier:
Qualifications and certifications
Choose suppliers with industry-recognised certifications such as ISO 9001 quality management systems. These certifications show that the supplier follows industry standards and is committed to maintaining high-quality manufacturing processes.
Technology and equipment
Examine the machinery and technology used by the supplier. Advanced CNC machines and software can improve productivity and part accuracy. Suppliers should be able to demonstrate how they maintain competitiveness through technology upgrades.
Experience and expertise
Prefer suppliers with extensive experience, especially those with specific experience in your industry or similar applications. Find out about the supplier's past projects and their ability to handle complex manufacturing issues.
Quality control processes
Check the supplier's quality control processes. A good supplier will have rigorous quality inspection steps to ensure that each product meets technical requirements. Ask them how they conduct material testing, finished product inspection and dimensional measurements.
Stability of the supply chain
A supplier's ability to manage its supply chain can have a direct impact on production lead times and delivery times. Examine how the supplier manages raw material inventory, the speed of order processing and its responsiveness to urgent demands.
Technical support
Good customer service and technical support are key to long-term co-operation. Evaluate whether suppliers provide design and technical consulting services and how efficiently they solve problems.
4 Steps to Fast Custom CNC Aluminum Parts
1. Upload Files
Submit technical drawings (2D &3D) of the part with purchase quantities and material requirements, all files support NDA.
2. Quotation
Within 12 hours we will provide a manufacturability design analysis and an accurate quote.
3. Manufacturing
Once the design and materials have been selected, CNC machines machine the raw materials into the exact part required.
4. Delivery
Once all parts pass quality assurance, they are securely packaged and shipped to you via DHL/UPS.
CNC Aluminum FAQs
How to CNC Aluminum Parts?
CNC machining aluminum parts involves a series of steps from design to finishing. The following is a detailed description of how to CNC machine an aluminum part.
1. Design the part
-CAD Modelling: Start by creating a detailed 3D model of the part using CAD (Computer Aided Design) software. The model should include all critical dimensions and tolerances.
2. Preparing the CNC machine
-Material Selection: Select the appropriate aluminum alloy for the required properties and application of the part.
– Tool Selection: Select suitable aluminum alloy tools such as carbide or diamond coated tools to provide better durability and accuracy.
– Machine setup: Secure the aluminum workpiece to the CNC machine using a jig or vise to ensure stability during machining.
3. CNC Machine Programming
– CAM SOFTWARE: Use CAM (Computer Aided Manufacturing) software to convert a CAD model into a g-code programme which provides instructions for the movement of the machine.
– Toolpath: Defining the toolpath controls where and how the tool interacts with the aluminum. This includes setting the cutting speed, feed and depth of cut.
4. Machining Parts
– Cutting: Starts the CNC machine and monitors the cutting process. Aluminum is usually machined at high speeds with a suitable lubricant or coolant to prevent sticking and overheating.
– MILLING: Perform any drilling or milling operations as required by the part design.
5. Quality Control
– CHECKING: After machining, check the dimensional accuracy of the part using tools such as calipers, micrometers, or a coordinate measuring machine (CMM).
– Deburring: Remove any sharp edges or burrs formed during machining to ensure that the finish of the part meets specifications.
6. Finishing Process
– Surface Treatment: Apply surface treatment such as anodizing, painting, or powder coating to improve corrosion resistance, surface hardness, and aesthetics.
– Polishing: If a high gloss is required, polish the part to achieve the desired luster.
7. Assembly and Testing
– ASSEMBLY: If the part is part of a larger assembly, connect it to other parts as specified.
– Test: Perform functional tests to ensure that the part meets all operational requirements.
By following these steps, you can effectively and efficiently machine high-quality aluminum parts using CNC technology.
Why is Aluminum Good for CNC Machining?
Aluminum is an excellent material choice for CNC machining due to several key advantages:
High machinability
– Aluminum is softer and more fragile, making it easier to cut and machine than other metals.
– Aluminum’s softness reduces tool wear and extends tool life, resulting in lower tool costs.
– Aluminum’s dimensional stability allows for the cutting of large amounts of material while maintaining tight tolerances.
Lightweight and Strong
– Aluminum has an excellent strength-to-weight ratio, providing good mechanical properties at a fraction of the weight of steel.
– This makes aluminum ideal for applications such as the aerospace and automotive industries that require lightweight, durable parts.
Corrosion Resistance
– Aluminum naturally forms an oxide layer that gives it good corrosion resistance in many environments.
– The corrosion resistance of aluminum can be further enhanced by anodizing it for more demanding applications.
Cost-effective
– Aluminum is typically less expensive than other metals such as steel or titanium.
– Due to its high machinability, aluminum takes less time and costs less to machine than harder metals.
– Aluminum parts are often faster and more economical to produce than other materials.
Versatility
– Aluminum alloys offer a wide range of mechanical properties for different applications by alloying with elements such as copper, silicon and magnesium.
– Common alloys such as 6061, 7075 and 2024 provide a good balance of strength, corrosion resistance and machinability for CNC machining.
In summary, aluminum’s excellent machinability, strength-to-weight ratio, corrosion resistance, cost-effectiveness, and versatility in a wide range of alloys make it an ideal material for the efficient and economical production of high-quality parts in a variety of industries.
What’s the Best Way to Cut Aluminum?
The best way to cut aluminum depends on the thickness, quantity, and desired finish quality. Here are some recommended methods:
For thin sheet and bar stock (up to 1/4″ thick)
Use a miter saw or circular saw with a fine-tooth carbide blade designed for non-ferrous metals. Hold the workpiece securely and apply a lubricant like WD-40 to the saw blade to ensure a clean cut. For thin aluminum sheets, tin snips will also provide a clean cut.
For thicker aluminum sheets (over 1/4″ thick)
Band saws with bi-metal blades are ideally suited for this type of work and produce less scrap than circular saws. Modern band saws can cut aluminum sheets at optimum speeds with a clean cut. It is also good to use dry or cold cutting saws equipped with carbide blades, which run at slower speeds, prevent overheating and provide very clean cuts.
For high volume production or fine machining
CNC mills and lathes are ideal for high precision machining of aluminum parts and assemblies. Plasma cutters are capable of cutting long straight cuts in thick aluminum sheets by melting the metal with a jet of ionising gas.
Other options for small production runs
For cutting tubes or bars, a hacksaw can be used; for cutting pipes, a router can be used; and as a last resort, an angle grinder with a cut-off wheel can also come in handy. Whichever tool is used, holding the workpiece securely and using the right blade or disc designed for aluminum is essential for a clean cut.
Which Aluminum is Best for Machining?
6061 aluminium alloy
- One of the most versatile alloys for machining.
- Excellent machinability, allowing complex geometries to be machined to tight tolerances.
- Good corrosion resistance and weldability.
- Ideal for structural components, aircraft parts and electronics.
2024 aluminium alloy
- High strength-to-weight ratio and good fatigue resistance.
- Machinability is fair to good and produces uniform chips.
- Commonly used in the aerospace and transport industries where high strength is required.
- Prone to chipping during heavy cutting and therefore requires optimised toolpaths.
7050 Aluminum Alloy
- High toughness and mechanical strength, even at sub-zero temperatures.
- Machinability is better than 7075 alloy with less burr formation.
- Commonly used for aerospace components and thick plates.
7075 aluminium alloy
- Very high strength and hardness.
- It has an excellent surface finish and is suitable for precision machining.
- Typically used in applications requiring high strength and wear resistance, such as aerospace and military equipment.
Alloys 6061 and 2024 are the most commonly recommended alloys for machining due to their excellent machinability, desirable strength and corrosion resistance. Alloy 7050 is noted for its excellent machinability and less burr formation than 7075, although 7075 has a better surface finish.
Other factors such as cost, heat treatability and specific application requirements should also be considered when selecting the best machined aluminum alloy. For example, 6061 alloy is often used for a variety of general applications due to its good all-round properties and relatively low cost. Alloys 2024 and 7075 are more suitable for high strength and performance requirements. Consider all these factors to select the best aluminum alloy for your specific needs.
Where Can I Order Custom Aluminum CNC Milled Parts?
For high-quality custom aluminum CNC milled parts, you can confidently turn to RALLY. We specializes in CNC aluminum machining services, and provides tailor-made solutions based on your specific design requirements. We are equipped with advanced machinery and have extensive experience in handling a variety of aluminum alloys, ensuring precision and efficiency in every project.
Why choose RALLY for your aluminum CNC milling needs?
– Customisation: From simple parts to complex assemblies, RALLY specialises in producing parts that meet our customers’ exact specifications.
– Quality and Accuracy: With state-of-the-art CNC machines and skilled technicians, RALLY consistently delivers high precision, high finish parts.
– Wide range of aluminum alloys: Whether you need the high strength of 7075 or the superior corrosion resistance of 5051, RALLY offers a wide range of aluminum alloys.
– Competitive Pricing: Thanks to efficient processes and professional management, RALLY offers competitive pricing without compromising quality.
– Fast turnaround: RALLY recognises the importance of timely delivery and is committed to meeting tight deadlines while ensuring top quality.
To learn more about our services or to place an order for custom aluminum CNC milled parts, whether your project is big or small, RALLY is ready to meet your CNC machining needs with professionalism and precision.
Contact RALLY for Your Custom CNC Aluminum Needs
Request a quote for aluminum CNC machining today! No minimum order quantity and free samples available!