Aluminum CNC Machining Services
Expertly machined aluminum components for aerospace, automotive and electronics.
Trusted Aluminum CNC Machining Partner - RALLY
RALLY is an experienced CNC machining service provider specialising in aluminum CNC machining. With strong R&D capabilities, we are able to provide high quality, customised aluminum parts to a wide range of industries including aerospace, automotive, medical devices, consumer electronics and more.
Our products are exported to markets such as the US, Canada, and Europe, and meet stringent quality requirements worldwide. We offer flexible and efficient solutions for both prototyping and mass production.
Key Strengths:
- Over 20 years of experience in CNC machining industry
- Specialised in high precision, customised aluminum parts machining
- Advanced equipment and technical team to ensure high quality production
- No minimum order quantity requirement, suitable for small and large scale production
- Fast production cycles and global logistics support
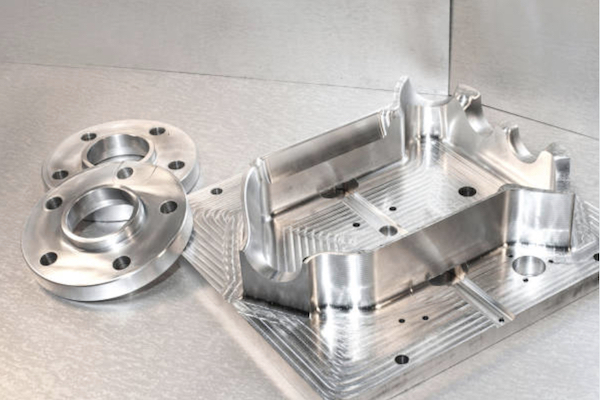
Our Capabilities
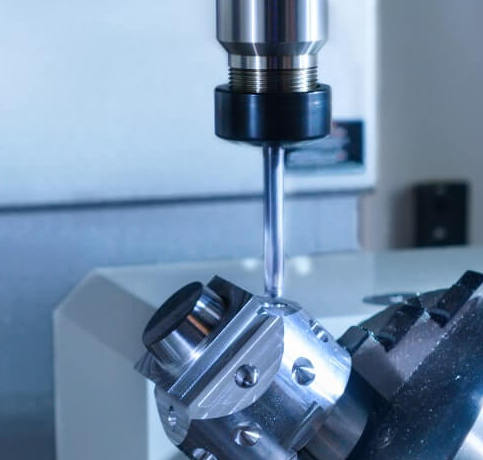
Aluminum CNC Milling
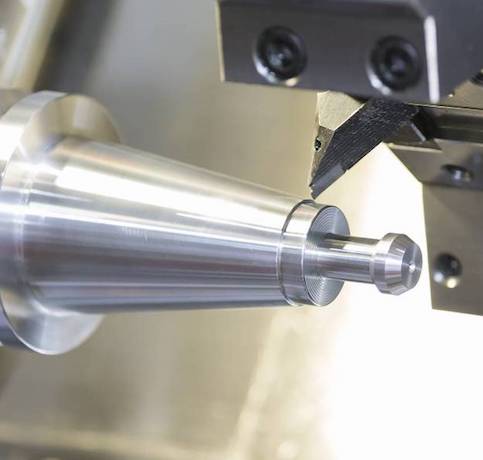
Aluminum CNC Turning
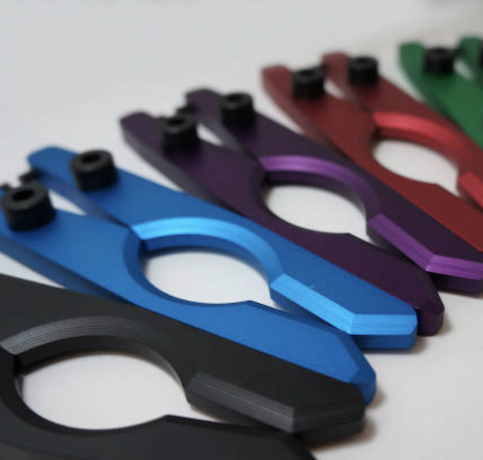
Aluminum Parts Surface Finishing
CNC Aluminum Parts We Offer
At RALLY, we provide a wide range of CNC aluminum parts, including custom components for aerospace, automotive, and electronics industries. Our state-of-the-art CNC technology ensures precision, durability, and perfect alignment with your project requirements.
Camera Lock Finger Grip
Quick Release Plate
Mounting Frame
Waveguide Component
Aluminum Air Inlet Flange
6061 Aluminum Hinge
Aluminum Waveguide Shim
Waveguide Choke Flange
Electronic Enclosure
CNC Aluminum Enclosure
CNC Aluminum Bike Stem
CNC Bicycle Aluminum Parts
Get a Quick Quote for Free Samples
Request a quick quote now and receive free samples of our precision CNC aluminum parts tailored to your specifications!
Surface Finishes For CNC Machined Aluminum Parts
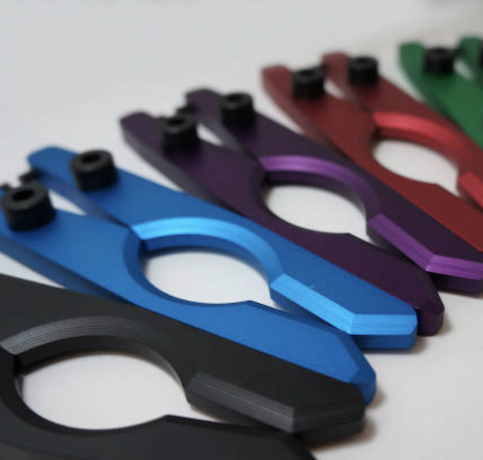
Anodizing
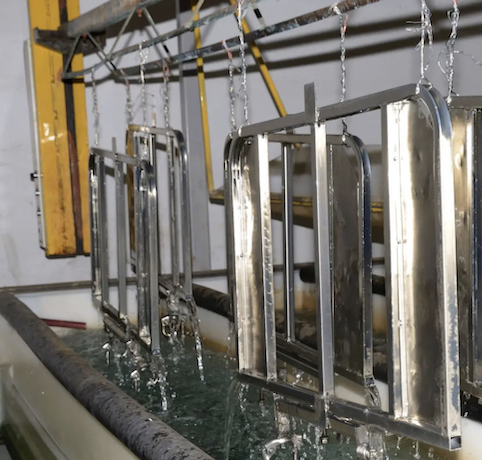
Electroplating
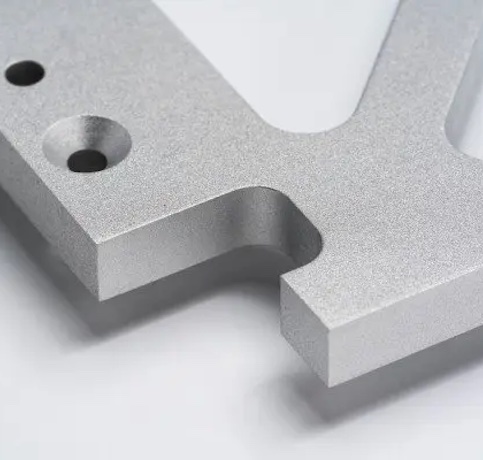
Sandblasting
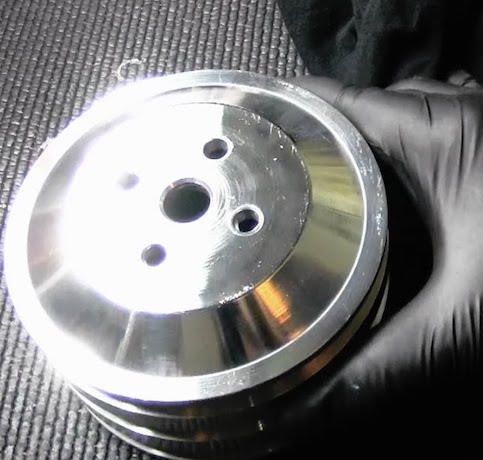
Polishing
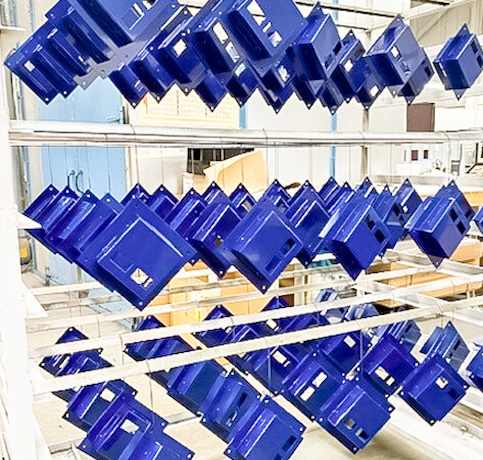
Coating
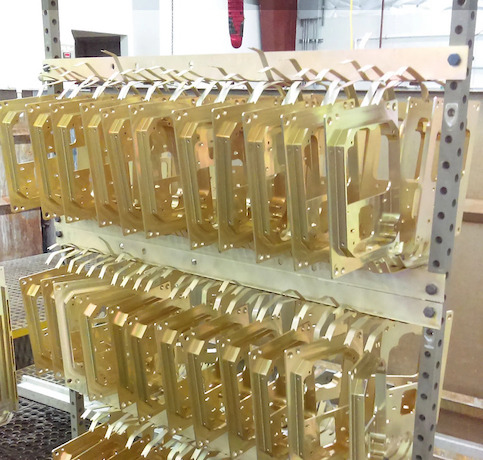
Chemical Conversion Coating
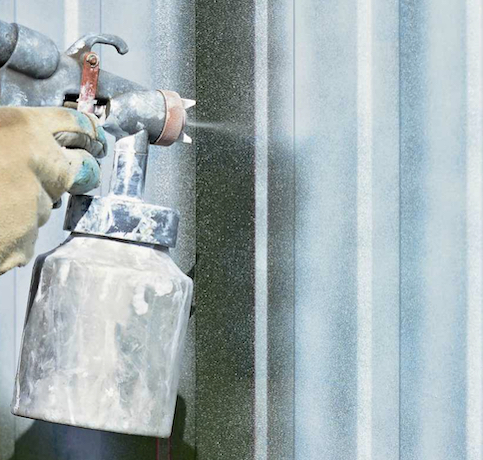
Painting
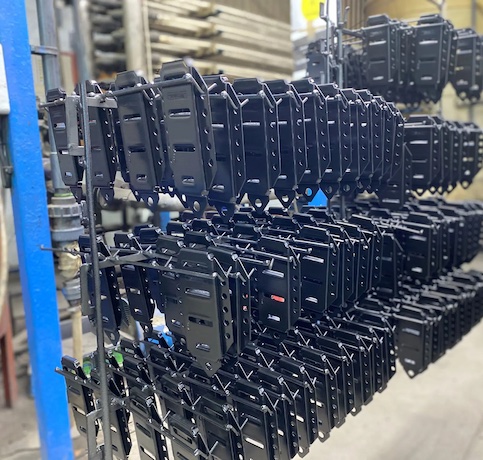
Electrophoretic Coating
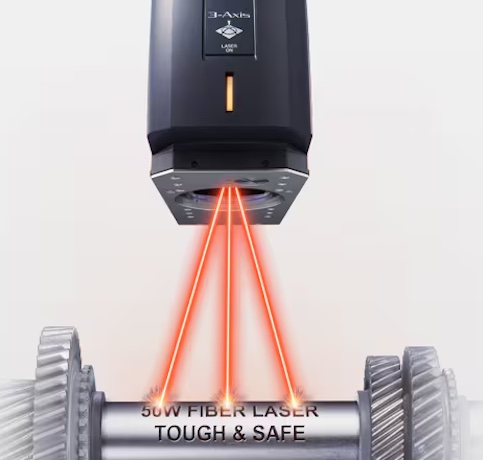
Laser Marking
Choosing the Right Surface Finish For CNC Aluminum Parts
Selecting the appropriate surface finish for your CNC machined aluminum parts depends on the specific requirements of your application, including aesthetics, corrosion resistance, wear resistance, and functionality. At RALLY, we offer a wide range of surface finishes to meet your needs, ensuring that your parts not only perform well but also look great. Our expertise in surface treatments guarantees high-quality results that enhance the durability and appearance of your aluminum components.
FAQ for Aluminum CNC Machining Services
1. What types of aluminum alloys can you machine?
2. What quality control measures do you have in place?
3. What is the minimum order quantity (MOQ) for aluminum parts?
4. What is your typical lead time?
5. Do you offer custom machining services?
6. How do you ensure precision in aluminum part machining?
7. Do you offer surface finishing services?
8. Which countries do you export to?
Get in Touch
Ready to get started? Contact us today for a free quote!
Metal Material
Aluminum, Brass, Stainless Steel, Carbon Steel, Copper, Titanium, etc.
Plastic Material
Acetal (Delrin), PTFE (Teflon), Acrylic (PMMA), PEEK, Nylon, ABS, PC, PP, POM, HDPE, PVC.
Surface Finishing
Anodizing, Powder Coating, Plating, Passivation, Bead Basting, Polishing, etc.
Inquiry Form
Let’s Start A New Project Today, Get Free Samples!
All You Need To Know About Aluminum CNC Machining
Table of Contents
Properties of aluminum
Lightweight:
Aluminum is significantly lighter than many other metals, making it ideal for applications requiring weight reduction, such as aerospace and automotive, where improved performance and fuel efficiency are crucial.
High Strength-to-Weight Ratio:
Aluminum offers an excellent strength-to-weight ratio, providing substantial strength without adding excessive weight. This property is essential for creating robust and durable parts in demanding applications.
Corrosion Resistance:
Aluminum naturally forms a protective oxide layer, enhancing its resistance to corrosion. This makes it suitable for use in harsh environments, such as marine and outdoor applications, reducing the need for additional coatings.
Excellent Machinability:
Aluminum’s excellent machinability allows for easy and efficient cutting, shaping, and finishing using CNC techniques. Its softness compared to other metals enables faster machining speeds and longer tool life, reducing production costs.
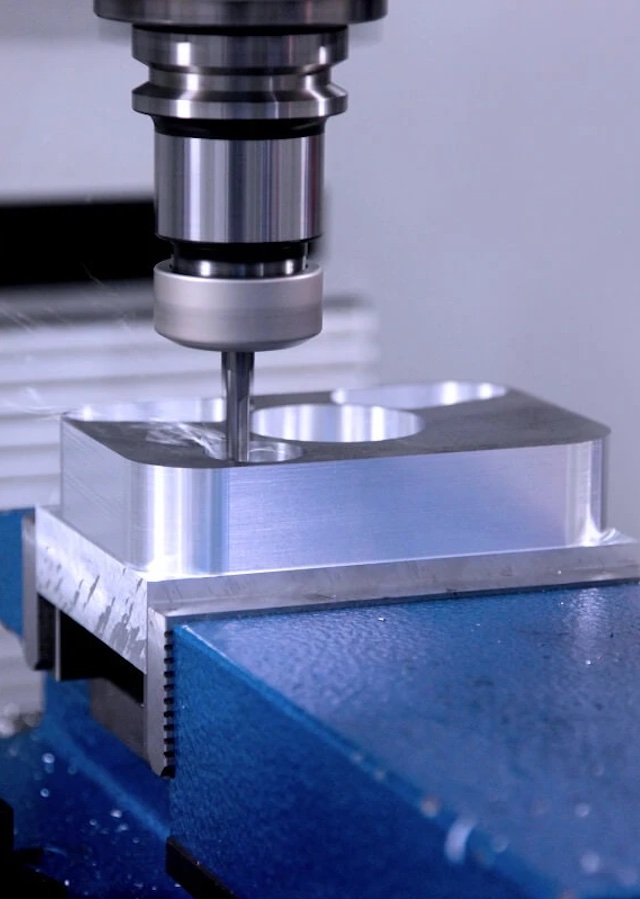
Aluminum CNC Machining Applications
Aluminum CNC machining offers versatility and precision, making it suitable for various industries. Below is a detailed breakdown of common application areas and examples:
Industry | Application Examples | Description |
---|---|---|
Aerospace | Structural components, brackets, housings, heat sinks | Lightweight yet durable aluminum parts for aircraft interiors and cooling systems. |
Automotive | Engine components, transmission housings, wheels, brackets | Precision parts for engines and chassis, contributing to fuel efficiency. |
Electronics | Device enclosures, heat sinks, connectors | Excellent thermal conductivity for cooling systems in electronic devices. |
Medical Devices | Equipment frames, housings, surgical instruments | Non-corrosive and lightweight parts for diagnostic tools and operating equipment. |
Robotics | Frames, joints, gear housings, sensor mounts | Aluminum parts ensure structural stability and precise movement. |
Consumer Goods | Bicycle frames, sports equipment, household appliances | Lightweight and corrosion-resistant materials for enhanced performance and durability. |
Aluminum’s lightweight, corrosion-resistant, and thermally conductive properties make it ideal for various industries. Whether in aerospace, automotive, or medical fields, RALLY’s CNC aluminum machining services ensure high precision and reliability to meet demanding project requirements.
What is the easiest machinable aluminum?
The easiest machinable aluminum alloy is 6061 aluminum. This alloy is highly popular in CNC machining due to its excellent balance of strength, corrosion resistance, and workability. It is also easy to machine, making it ideal for creating precision parts in various industries such as aerospace, automotive, and consumer electronics.
6061 aluminum’s moderate strength, good thermal conductivity, and ability to be anodized for better surface finish further enhance its machinability, making it a preferred choice for many machining projects.
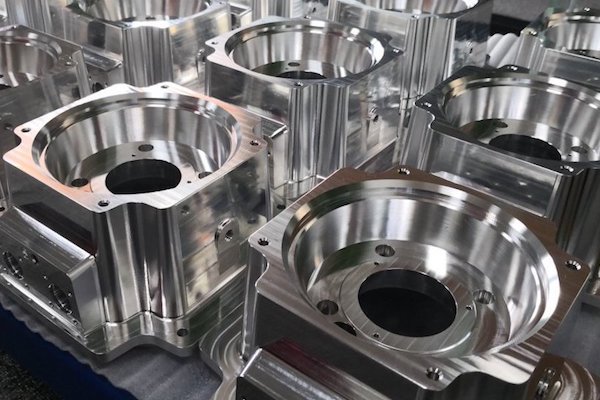
Aluminum Alloy 6061
- Machinability: Excellent, with a machinability rate of approximately 270%.
- Characteristics: This alloy is versatile, has good corrosion resistance, and is widely used in various applications including automotive parts and structural components.
- Applications: Commonly found in CNC machining shops, it is ideal for general engineering and fabrication tasks due to its balance of strength and ease of machining.
What is the difference between CNC 7075 and 6061?
The differences between CNC 7075 and 6061 aluminum are significant, particularly regarding their mechanical properties, machinability, corrosion resistance, and typical applications. Here’s a detailed comparison:
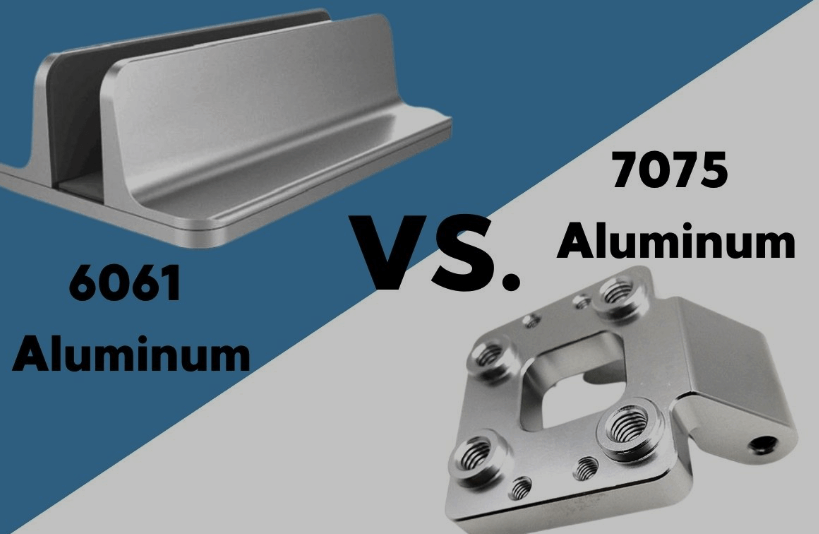
Key Differences Between CNC 7075 and 6061 Aluminum:
Category | 6061 Aluminum | 7075 Aluminum |
---|---|---|
Chemical Composition | Primarily alloyed with silicon (0.6%-0.7%) and magnesium (0.9%-1.2%), part of the 6000 series. | Alloyed mainly with zinc (5.6%) and copper (1.6%), part of the 7000 series. |
Strength | Tensile strength of approximately 276 MPa (T6 condition). | Nearly double the strength of 6061, with a tensile strength of approximately 503 MPa (T6 condition). |
Hardness | Brinell hardness of around 95, softer and more deformable. | Higher Brinell hardness of around 150, more resistant to wear and deformation. |
Machinability | Excellent machinability, easier to cut and shape, ideal for complex parts. | Fair machinability; harder and stronger, leading to more tool wear during machining. |
Corrosion Resistance | Better corrosion resistance due to higher silicon content, suitable for moisture-exposed environments. | Lower corrosion resistance due to higher copper content, making it more susceptible to oxidation. |
Weldability | Excellent weldability, compatible with TIG and MIG welding methods. | Poor weldability unless annealed; welding can reduce strength in heat-affected zones. |
Applications | Used in automotive parts, structural components, marine applications, and general manufacturing. | Primarily used in aerospace, military, and high-stress applications where strength is critical. |
Summary Table
Property | 6061 Aluminum | 7075 Aluminum |
---|---|---|
Alloy Series | 6000 | 7000 |
Main Alloying Elements | Silicon & Magnesium | Zinc & Copper |
Tensile Strength (MPa) | ~276 | ~503 |
Hardness (Brinell) | ~95 | ~150 |
Corrosion Resistance | Better | Lower |
Machinability | Good | Fair |
Weldability | Excellent | Poor |
Common Applications | Automotive, structural | Aerospace, military |
In conclusion, the choice between CNC machining with 7075 or 6061 aluminum should be based on the specific requirements of your project—whether you prioritize strength (favoring 7075) or machinability and corrosion resistance (favoring 6061).
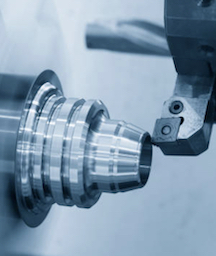
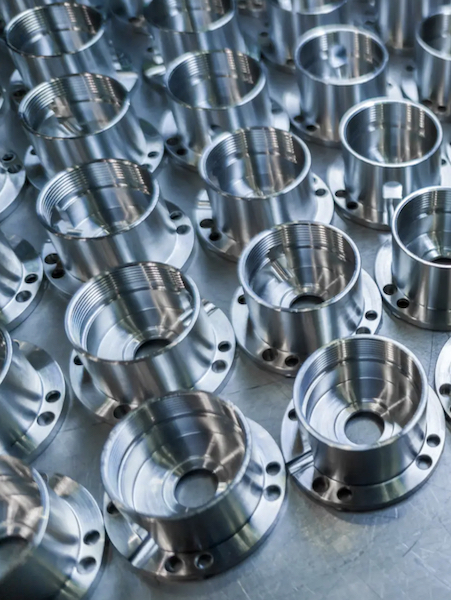
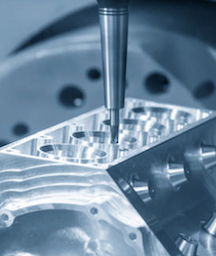
What is the best aluminum for CNC machining?
The best choice of aluminum depends on the specific requirements of the project. However, the most common and versatile aluminum alloys for CNC machining include:
6061 Aluminum
6061 aluminum is highly versatile and offers excellent machinability, good strength, and corrosion resistance. It is ideal for a wide range of applications, including automotive parts, aerospace components, industrial machinery, and consumer electronics, making it a go-to choice.
7075 Aluminum
7075 aluminum is known for its exceptional strength and fatigue resistance. It is suitable for high-stress applications such as aerospace structures, military equipment, and performance automotive parts, where superior mechanical properties and durability are crucial.
6082 Aluminum
6082 aluminum offers good machinability and corrosion resistance with medium strength. It is commonly used in structural applications, such as bridges, cranes, and transportation systems, where durability and resistance to environmental factors are essential.
2024 Aluminum
2024 aluminum is recognized for its high strength and excellent fatigue resistance. It is frequently used in aerospace applications, including aircraft structures and high-stress components, where these properties are critical for performance and safety.
Can you CNC 6061 aluminum?
Yes, 6061 aluminum is perfect for CNC machining. In particular, the 6061-T6 variant, which is one of the most commonly used aluminum alloys for CNC machining. This alloy is favoured for its excellent properties, which include:
1. Good machinability: 6061-T6 is known for its ease of machining, allowing for precise cuts and shapes. It can achieve tight tolerances, making it suitable for machining complex parts.
2. Corrosion resistance: This alloy has good corrosion resistance, making it ideal for use in a variety of environments, including harsh or wet environments.
3. Strength and Durability: Although 6061-T6 is not the strongest aluminum alloy (e.g. 7075), it offers a good balance of strength and weight, making it suitable for structural applications.
4. Weldability: 6061-T6 is easy to weld, which facilitates the manufacture of complex assemblies.
In CNC machining, both milling and turning processes can be used to machine 6061 aluminum into the required components. This versatility makes it a popular choice for industries such as aerospace, automotive and general manufacturing.
In short, 6061 aluminum combines machinability, strength and corrosion resistance, making it an excellent choice for CNC machining.
Which aluminum is stronger 5052 or 6061?
When comparing the strength of aluminum alloys 5052 and 6061, 6061 aluminum is generally stronger than 5052. This distinction arises from several key mechanical properties:
Property | 5052 Aluminum | 6061 Aluminum | Explanation |
---|---|---|---|
Yield Strength | 193 MPa (28,000 psi) | 276 MPa (40,000 psi) | 6061 can withstand more stress before permanent deformation occurs. |
Ultimate Tensile Strength | 228 MPa (33,000 psi) | 310 MPa (45,000 psi) | 6061 offers superior tensile strength, making it ideal for heavy loads. |
Fatigue Strength | 117 MPa | 96.5 MPa | 5052 performs better under repetitive stress cycles, offering greater fatigue resistance. |
Best Use Case | Applications requiring fatigue resistance and forming | Applications requiring high structural strength and heavy load-bearing | Choose 5052 for applications involving frequent stress cycles; choose 6061 for structural strength. |
Summary
- 6061 aluminum is preferred for applications that demand high structural strength and the ability to handle significant loads due to its superior yield and tensile strength.
- 5052 aluminum, although less strong initially, performs better under repetitive stress cycles due to its higher fatigue strength, making it more suitable for applications that involve constant or repeated stress.
Ultimately, the choice between these two alloys depends on the specific requirements of your project. If structural strength is critical, 6061 is the better option. However, for forming or applications with repeated stress, 5052 may be the more appropriate choice。
What is the difference between forged aluminum and machined aluminum?
The difference between forged aluminum and machined aluminum primarily lies in their manufacturing processes, properties, and applications. Here’s a detailed comparison:
Manufacturing Processes: Forged Aluminum vs. Machined Aluminum
Process | Forged Aluminum | Machined Aluminum |
---|---|---|
Description | Involves heating aluminum and shaping it under high pressure. | Produced by cutting a solid aluminum block (billet) using CNC machines. |
Strength & Durability | Aligns the internal grain structure, enhancing strength and durability. | Offers excellent mechanical properties with precise shaping capabilities. |
Production Method | Forged parts are produced from a single mold, suitable for mass production. | Allows for tight tolerances and complex geometries not achievable with forging. |
Cost Efficiency | Cost-effective for mass production due to reusable molds. | Higher costs due to material waste and machining time. |
Common Alloys | Typically uses alloys like 6061 or 7075 for structural parts. | 6061-T6 and 7075-T6 are frequently used for their corrosion resistance and strength. |
Best Use Case | Ideal for parts requiring high strength and durability, such as automotive or aerospace components. | Suitable for intricate, high-precision parts in aerospace, medical devices, and electronics. |
Applications:
- Forged Aluminum: Typically used in applications where strength and durability are critical, such as in aerospace components, automotive parts (e.g., wheels and suspension parts), and high-stress industrial equipment.
- Machined Aluminum: Preferred for complex, precision parts that require tight tolerances and detailed features, such as prototypes, enclosures, medical devices, and electronic housings.
Cost:
- Forged Aluminum: Usually more expensive due to the intensive process and tooling required for forging.
- Machined Aluminum: Generally more cost-effective for small production runs, as it allows for greater flexibility in design without needing specialized forging dies.
Choosing between forged and machined aluminum depends on the specific requirements of a project, including desired strength, precision, complexity of design, and budget constraints. Each method offers distinct advantages suited to different applications.
Is 6061 aluminum stronger than cast aluminum?
To determine whether 6061 aluminum is stronger than cast aluminum, we need to look at the specific properties of these materials, as “cast aluminum” can refer to various alloys, such as A380 or MIC-6.
Strength Comparison
6061 Aluminum
6061 aluminum is a precipitation-hardened alloy primarily composed of magnesium and silicon. It is known for its:
- High strength-to-weight ratio: 6061-T6, a common temper of this alloy, has a yield strength of approximately 275 MPa and tensile strength around 310 MPa.
- Excellent weldability: This makes it suitable for applications requiring strong joints.
- Corrosion resistance: It performs well in various environments, which is crucial for many structural applications.
6061 aluminum is often used in construction, automotive, aerospace, and marine applications due to its versatility and mechanical properties.
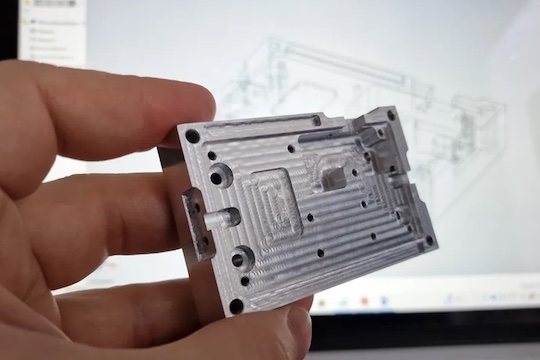
Cast Aluminum
Cast aluminum typically refers to alloys like A380 or MIC-6, which are produced through casting processes. Their properties include:
- A380 Aluminum: Known for its good casting performance, A380 has a yield strength of about 160 MPa and tensile strength around 310 MPa. It offers excellent fluidity and is often used in die casting for complex shapes.
- MIC-6 Aluminum: This alloy is designed for precision machining with excellent dimensional stability. While it has good mechanical properties, it generally does not match the strength of 6061-T6.
Comparison Table
Property | 6061 Aluminum (T6) | A380 Cast Aluminum | MIC-6 Cast Aluminum |
---|---|---|---|
Yield Strength (MPa) | ~275 | ~160 | ~250 |
Tensile Strength (MPa) | ~310 | ~310 | ~300 |
Weldability | Excellent | Limited | Moderate |
Corrosion Resistance | Excellent | Good | Good |
In general, 6061 aluminum (especially in the T6 temper) is stronger than typical cast aluminum alloys like A380, particularly in terms of yield strength. It also has superior weldability and corrosion resistance. However, when comparing it to MIC-6 cast aluminum, the strengths are closer, with MIC-6 being more suited for precision applications rather than structural ones.
Thus, if your application requires high strength and weldability, 6061 aluminum would be the preferred choice over most cast aluminum options.
What is the application of Aluminum 7075?
Aluminum 7075 is a high-strength alloy known for its excellent mechanical properties, corrosion resistance, and lightweight nature. It is widely used in industries where strength, toughness, and fatigue resistance are critical. Below are some of the primary applications:
Industry | Application Examples | Reason for Use |
---|---|---|
Aerospace | Structural components, aircraft wings, fuselage parts | High strength-to-weight ratio and corrosion resistance. |
Automotive | Suspension systems, gears, driveshafts | Durable under high stress and impact; reduces vehicle weight for efficiency. |
Defense & Military | Firearms, military-grade equipment | Toughness and fatigue resistance in extreme conditions. |
Sports Equipment | Bicycle frames, rock climbing gear, golf clubs | Lightweight yet strong for enhanced performance and durability. |
Marine | Boat fittings, propellers, and high-performance hulls | Corrosion resistance in marine environments. |
Robotics & Drones | Structural frames, joints, motor mounts | Lightweight for better maneuverability with high mechanical strength. |
Medical Devices | Prosthetics, surgical instruments | Combines durability, lightweight design, and corrosion resistance. |
Aluminum 7075 is favored in industries requiring high performance under stress. It is particularly well-suited for aerospace, automotive, and sports equipment, where weight savings and mechanical strength are essential.
Work with RALLY for Aluminum CNC Machining
Request a quote for new project today! No minimum order quantity and free samples available!