ABS Machining Services
Precision CNC Machining for Durable and Impact-Resistant ABS Parts.
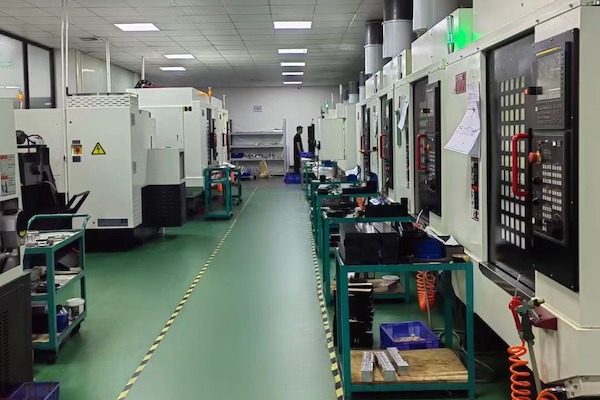
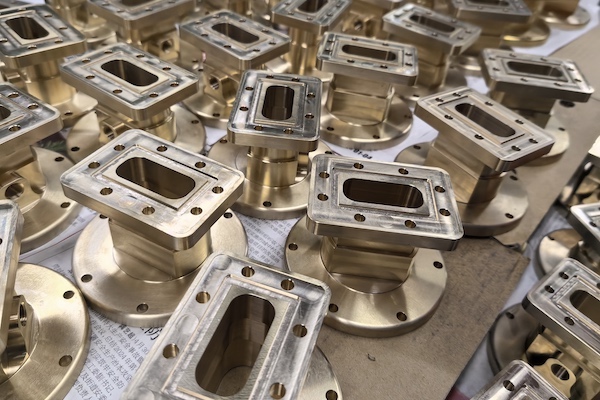
Precision ABS Parts Machining
At RALLY, we specialize in providing high-precision ABS parts machining services, catering to a wide range of industries. ABS is known for its excellent strength, impact resistance, and superior machinability, making it an ideal material for both prototyping and mass production.
With our advanced CNC machining equipment and skilled technical team, we ensure every ABS part meets the highest standards of precision and consistency, suitable for applications in automotive, electronics, medical devices, and more.
Whether you require small batch customization or large-scale production, we offer flexible and efficient solutions to meet your needs. From design drawings to final product delivery, we handle every step of the process, ensuring that your products meet the required performance, quality, and delivery timelines.
Machining Capabilities for ABS
High precision and complex geometry
At RALLY, we leverage advanced CNC equipment to precisely machine ABS materials, ensuring high accuracy and the ability to handle complex geometries. Our multi-axis CNC machining centers achieve tight tolerances of up to ±0.01mm, enabling us to easily produce even the most intricate designs. With cutting-edge CNC technology, we can handle complex surfaces, precise hole drilling, and multi-angle cuts, addressing the most demanding machining tasks.
Whether for prototype development or mass production of complex ABS parts, we guarantee that every part meets stringent technical requirements. Our experienced technical team is adept at optimizing the machining process to ensure the final product not only looks excellent but also meets the highest industry standards in terms of performance.
Surface Finishing Options for ABS:
We provide a variety of surface finishing options to enhance the appearance and functionality of ABS parts, ensuring they meet your final product’s aesthetic and performance requirements. Our surface treatments include:
Painting: We provide high-quality spray painting in a wide range of colors and finishes, allowing you to achieve the desired visual effect, whether matte, glossy, or textured.
Polishing: For applications requiring a smooth and reflective finish, our polishing services ensure a clean, flawless surface, ideal for cosmetic or functional parts.
Plating: We offer various plating options, including chrome plating and other metallic coatings, which can enhance durability, wear resistance, and give the parts a metallic look while maintaining the lightweight nature of ABS.
These surface treatments ensure that your ABS parts not only perform well but also meet the highest standards of visual appeal, durability, and functionality.
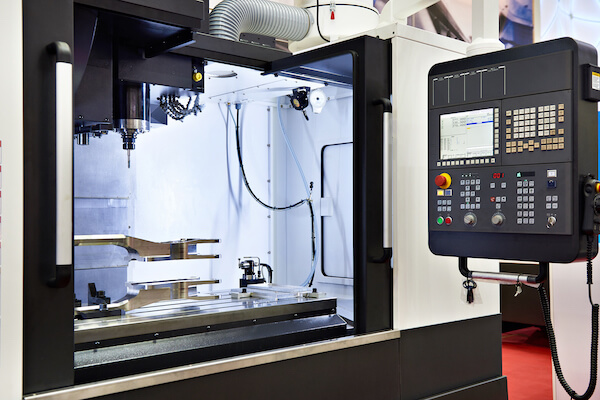
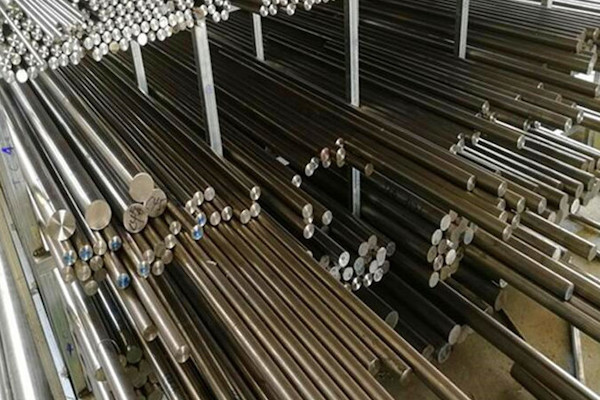
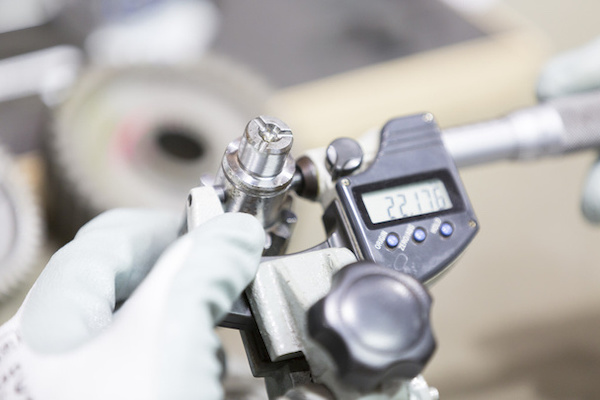
General Properties of ABS
Acrylonitrile Butadiene Styrene (ABS) is a widely utilized thermoplastic polymer known for its excellent mechanical properties, versatility, and ease of processing. It is a terpolymer composed of three monomers: acrylonitrile, butadiene, and styrene, each contributing distinct characteristics to the material.
Physical Properties
Impact Resistance: ABS is renowned for its excellent impact strength, making it suitable for applications requiring durability.
Tensile Strength: Typically ranges from 35 to 50 MPa, allowing it to withstand significant pulling forces without breaking.
Flexibility: Offers a balance of rigidity and flexibility, enabling it to endure moderate deformation without cracking.
Thermal Stability: ABS can maintain structural integrity within a temperature range of -20 to 80 °C (-4 to 176 °F), but begins to deform at temperatures above 80-85 °C (176-185 °F).
Electrical Insulation: It serves as an excellent electrical insulator, making it ideal for electronic applications.
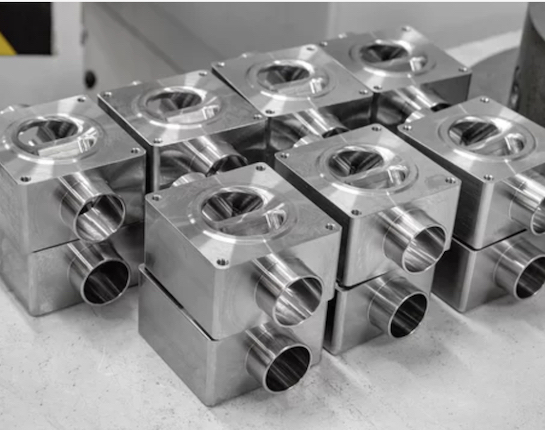
Applications of ABS Parts
ABS parts are widely used across various industries due to their excellent mechanical properties and versatility. Common application areas include:
Automotive Manufacturing:
ABS is frequently used in interior components, dashboards, armrests, and other plastic parts in vehicles. These parts require high strength, impact resistance, and a quality surface finish, making ABS the perfect material for such applications.
Consumer Electronics:
ABS is employed in the housing, supports, and internal components of electronic devices. Its ease of processing and excellent surface finish make it ideal for producing durable, aesthetically pleasing parts in products such as smartphones, computers, and other electronics.
Medical Devices:
ABS is used in the enclosures and components of medical equipment. Its impact resistance, easy sterilization, and stable performance in high-use environments make it a suitable material for meeting the stringent requirements of the medical industry.
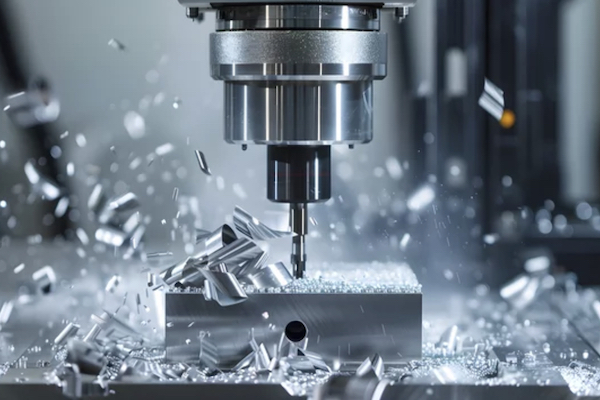
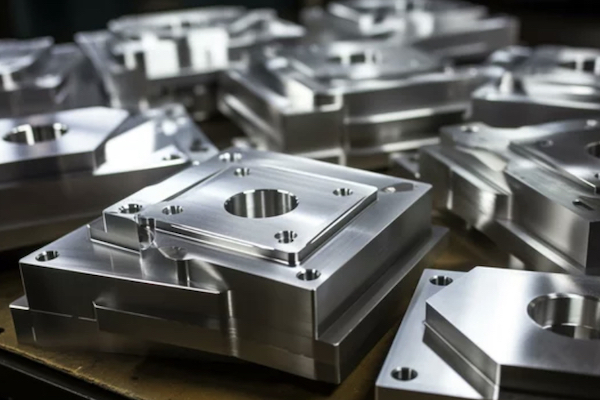
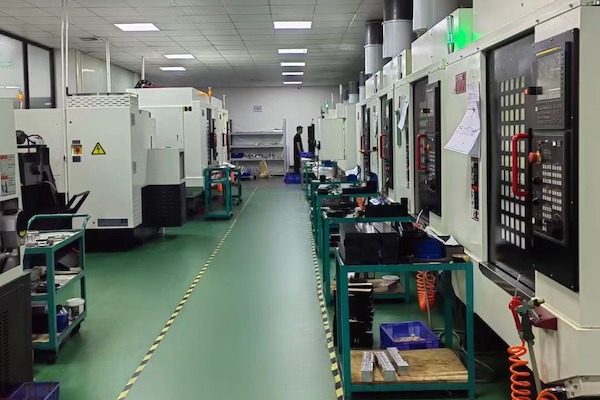
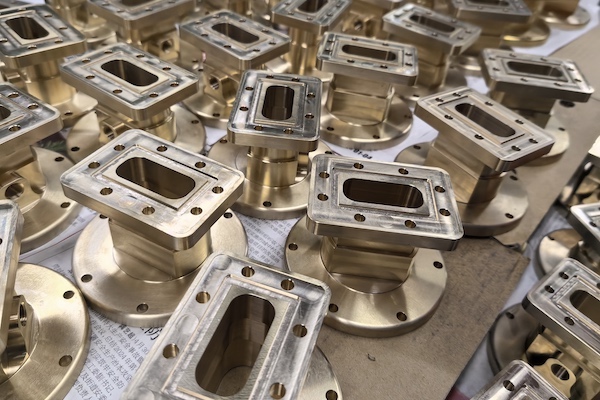
Benefits of Choosing ABS Parts from RALLY
Efficient Production:
At RALLY, we pride ourselves on our ability to deliver ABS parts quickly and efficiently. Our streamlined production processes allow us to meet tight deadlines, ensuring your projects stay on schedule without compromising on quality.
Flexible Customization:
We offer flexible customization options to meet your specific requirements. Whether you need ABS parts in unique shapes, sizes, or with complex geometries, our advanced CNC machining capabilities allow us to produce high-precision parts tailored to your exact needs.
Cost Advantage:
We provide competitive pricing while maintaining the highest quality standards. Our efficient manufacturing processes enable us to offer cost-effective solutions, ensuring you receive premium ABS parts at an excellent value.
Get a Quick Quote for Free Samples
Request a quick quote now and receive free samples of our precision CNC machining parts tailored to your specifications!
FAQ for ABS Machining Parts Services
1. Do you have any minimum order requirements for ABS parts?
2. What level of precision can you offer when machining ABS parts?
3. What is the typical lead time for ABS parts production?
4. Can you produce custom ABS parts based on my specific design?
5. What surface treatment options can you provide for ABS parts?
6. What quality control measures do you have in place for ABS parts?
7. What industries can benefit from your ABS CNC machined parts?
Get in Touch
Ready to get started? Contact us today for a free quote!
Metal Material
Aluminum, Brass, Stainless Steel, Carbon Steel, Copper, Titanium, etc.
Plastic Material
Acetal (Delrin), PTFE (Teflon), Acrylic (PMMA), PEEK, Nylon, ABS, PC, PP, POM, HDPE, PVC.
Surface Finishing
Anodizing, Powder Coating, Plating, Passivation, Bead Basting, Polishing, etc.
Inquiry Form
Let’s Start A New Project Today, Get Free Samples!
All You Need To Know About ABS Machining
Table of Contents
Why Choose ABS for CNC Machining?
ABS (Acrylonitrile Butadiene Styrene) is a preferred material for CNC machining due to its unique combination of properties and versatility. Here are some key reasons why ABS is an ideal choice:
High Strength and Impact Resistance: ABS offers excellent mechanical strength and toughness, making it suitable for parts that need to withstand stress or mechanical impact.
Ease of Machining: ABS is relatively easy to cut, drill, and shape, allowing for efficient machining of complex geometries while maintaining dimensional stability.
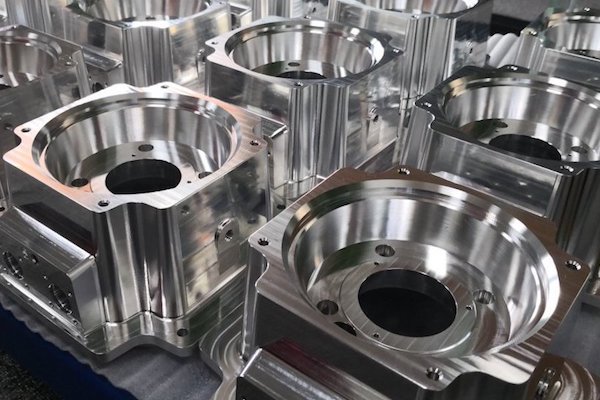
Cost-Effective for Prototyping and Production: ABS is affordable compared to other engineering plastics, making it an economical option for small-batch production and prototyping.
Good Surface Finish Properties: ABS supports a variety of surface treatments, including painting and plating, providing flexibility in achieving desired aesthetics and functional finishes.
Thermal and Chemical Stability: ABS maintains its shape and performance under moderate heat and chemical exposure, making it suitable for automotive and industrial applications.
These characteristics make ABS an excellent material for CNC machining, offering a balance of durability, machinability, and cost-effectiveness across a wide range of applications.
How to Avoid Surface Quality Issues in ABS Machining?
To achieve high-quality surface finishes in ABS CNC machining, it’s essential to follow best practices throughout the machining process. Below are key strategies to avoid surface defects:
1. Use Sharp and High-Quality Tools
- Dull tools can cause rough surfaces, tearing, or melting. Ensure cutting tools are sharp and appropriate for plastic machining to prevent surface imperfections.
- Carbide or diamond-coated tools are recommended for smooth cutting and extended tool life.
2. Optimize Cutting Parameters
- Set optimal feed rates and cutting speeds to minimize heat buildup, which can cause melting or surface roughness.
- Slower feed rates and moderate spindle speeds are ideal for machining ABS to maintain dimensional accuracy and surface quality.
3. Control Temperature and Heat Dissipation
- Excess heat can lead to material deformation, melting, or warping. Use coolants or compressed air during machining to control the temperature and reduce heat accumulation.
- Avoid excessive cutting depth, as deeper cuts generate more heat.
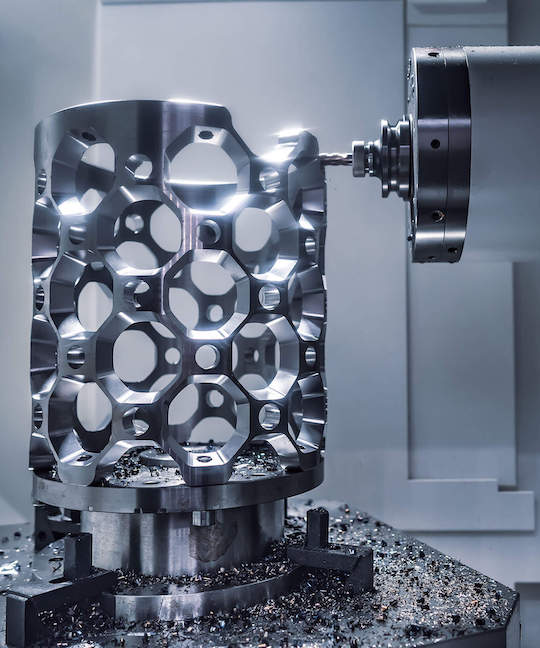
4. Minimize Tool Marks with Proper Toolpaths
- Use finishing toolpaths for the final passes to smooth out tool marks and enhance surface finish.
- Employ climb milling (instead of conventional milling) to reduce surface chatter and achieve a finer finish.
5. Ensure Proper Clamping and Fixturing
- Inadequate clamping can cause vibration, resulting in poor surface quality. Use appropriate fixtures to securely hold ABS parts in place during machining.
By following these guidelines, you can significantly reduce the risk of surface quality issues during ABS CNC machining, ensuring smooth, precise, and aesthetically pleasing parts that meet both functional and cosmetic requirements.
What Surface Finishes are Available for ABS Parts?
ABS parts can be treated with a variety of surface finishes to enhance both appearance and functionality. Below are some of the most commonly used surface finishing options, along with their descriptions and typical applications:
Surface Finish | Description | Typical Applications |
---|---|---|
Painting | Spray painting in various colors and finishes (matte, gloss, textured). | Used for aesthetic purposes, such as in consumer electronics. |
Polishing | Removes minor surface imperfections to achieve a smooth, shiny surface. | Ideal for cosmetic parts or components requiring a reflective finish. |
Chrome Plating | Applies a metallic coating to enhance appearance and durability. | Common in automotive and decorative components. |
Textured Finishing | Creates patterns or textures on the surface for grip or design elements. | Used in tool handles, electronics housings, or control panels. |
Vapor Smoothing | Smooths the surface using chemical vapor to remove minor imperfections. | Used in medical devices and prototypes for improved aesthetics. |
Sanding | Manual or machine sanding to prepare the surface for painting or bonding. | Prepares parts for subsequent coatings or adhesives. |
These surface finishes not only improve the aesthetics of ABS parts but also enhance their performance, providing additional functionality such as improved grip, increased durability, or chemical resistance. Depending on the product’s end-use, a combination of these finishes can be applied to achieve optimal results.
What Tolerances Can Be Achieved with ABS Machining?
At RALLY, we understand that precision is critical for many industries. Our advanced CNC machining equipment allows us to achieve tight tolerances of ±0.01mm when machining ABS parts.
This level of accuracy ensures that the components meet exact design specifications, making them suitable for demanding applications in industries such as automotive, electronics, and medical devices.
Our multi-axis CNC machines are specifically calibrated to handle the unique properties of ABS, preventing deformation and ensuring dimensional stability.
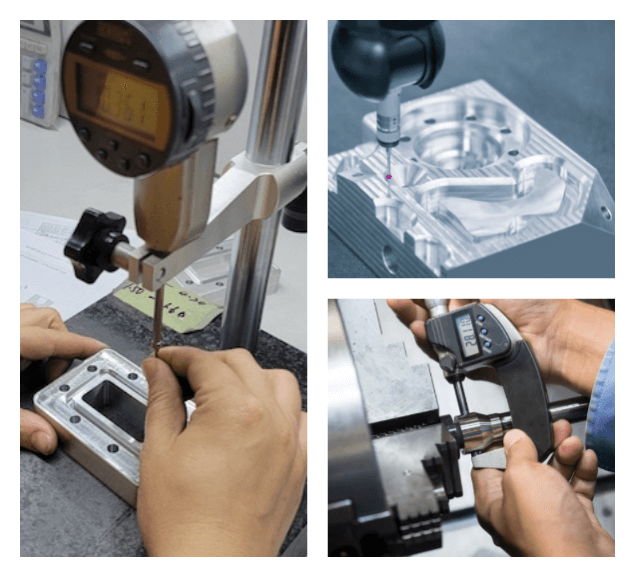
We also conduct thorough quality inspections at every stage of production, including in-process checks and final inspections, to ensure that each part meets your precise requirements.
With RALLY’s expertise, you can trust that your ABS components will be manufactured with the highest accuracy and consistency, helping you achieve reliable performance and seamless assembly.
What Applications are Suitable for ABS Machining?
ABS CNC machining is widely used across various industries due to ABS’s unique combination of strength, impact resistance, and ease of processing. Below are some of the key application areas where ABS CNC machined parts excel:
1. Automotive Industry
- Interior Components: Dashboards, air vents, and armrests.
- Prototypes: Concept parts for testing and design iterations before mass production.
- Exterior Accessories: Lightweight brackets and covers.
ABS parts provide durability and a smooth finish, making them perfect for both functional components and aesthetic interior parts.
2. Consumer Electronics
- Device Housings: Smartphone and tablet enclosures.
- Mounts and Supports: Internal supports for electronic circuits.
ABS’s excellent surface finish capabilities and impact resistance make it a top choice for consumer electronics.
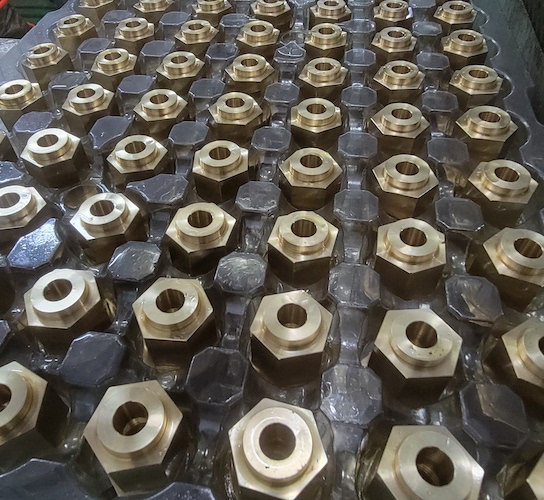
3. Medical Devices
- Equipment Casings: Enclosures for diagnostic tools and devices.
- Components: Handles, connectors, and buttons.
ABS parts meet the need for durability, easy cleaning, and sterilization, making them well-suited for medical environments.
4. Prototyping and Product Development
- Concept Models: ABS is frequently used for visual and functional prototypes.
- Design Validation: Components for testing fit, function, and durability.
ABS’s affordability and ease of machining make it ideal for quick design iterations during the prototyping phase.
5. Industrial Applications
- Machine Components: Lightweight, durable parts for equipment.
- Control Panels: ABS parts offer durability and the ability to integrate with electronics.
ABS’s strength and chemical resistance make it suitable for use in industrial environments.
Why is ABS preferred over other plastics for CNC machining?
ABS (Acrylonitrile Butadiene Styrene) is favored for CNC machining because of its ideal mix of mechanical properties, ease of processing, and affordability. Here’s a brief overview of why ABS stands out:
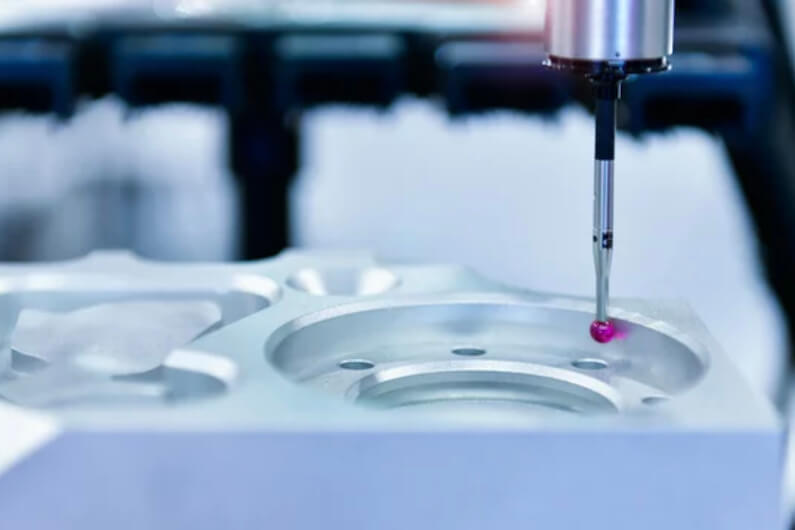
Key Benefits
- Impact Resistance: Durable enough to withstand shocks, making it perfect for automotive and electronics applications.
- Dimensional Stability: Maintains precise shapes over time, ensuring parts meet tight tolerances.
- Tensile Strength: Provides a strong yet rigid structure suitable for many applications.
Processing Advantages
- Easy to Machine: Cuts and shapes easily, reducing machining time and costs.
- Cost-Effective: Ideal for low- to medium-volume production without needing expensive molds.
- Rapid Prototyping: Affordable and quick to process, enabling fast design iterations.
In short, ABS offers an excellent combination of durability, precision, flexibility, and affordability, making it a top choice for CNC machining across various industries.
How Does ABS Compare with Other Plastics for CNC Machining?
Property | ABS | PEEK | Nylon (PA) |
---|---|---|---|
Strength & Toughness | High strength, good impact resistance | Extremely high strength and durability | High toughness, excellent wear resistance |
Ease of Machining | Easy to machine with minimal tool wear | More difficult due to hardness | Moderately easy, requires sharp tools |
Cost | Low cost, budget-friendly for prototypes | High cost, suitable for high-performance parts | Moderate cost, often used in mechanical components |
Temperature Resistance | Moderate (up to ~80°C) | Excellent (up to 260°C) | Good (up to ~120°C) |
Chemical Resistance | Resistant to mild chemicals, solvents | Excellent chemical resistance | Resistant to oils and chemicals |
Surface Finish Options | Supports painting, polishing, and plating | Limited due to hardness | Can be polished, but often textured |
Common Applications | Prototypes, consumer electronics, automotive | Aerospace, medical devices, industrial equipment | Gears, bearings, mechanical parts |
Summary
- ABS is ideal for applications that require affordability, ease of machining, and good surface finish options. It works well for prototypes, automotive interiors, and electronic housings.
- PEEK is best for high-performance applications due to its superior temperature resistance and chemical stability but comes at a higher cost.
- Nylon (PA) is suitable for mechanical components that require wear resistance and moderate temperature tolerance, commonly used in gears and bearings.
By understanding the specific needs of your project, you can select the material that offers the best balance of performance and cost for your application.
Work with RALLY for CNC Turning Parts
Request a quote for new project today! No minimum order quantity and free samples available!