CNC Machining Parts Supplier
Precision Manufacturing, Quality Assurance: Your Partner in CNC Solutions
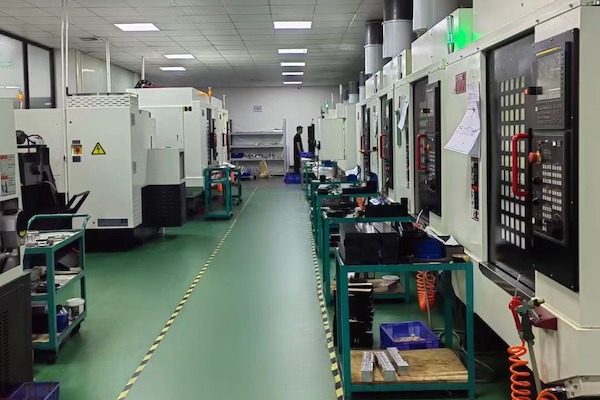
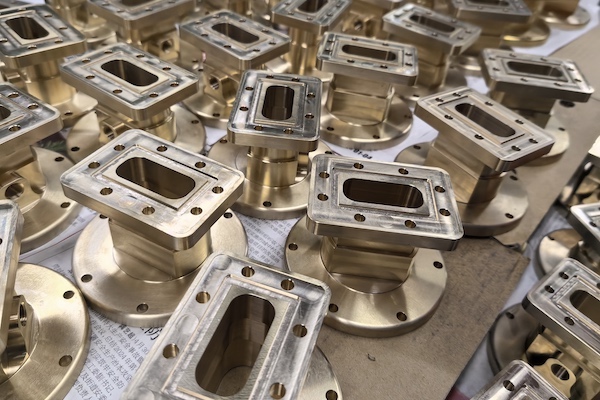
CNC Machining Parts Supplier
At RALLY, we understand the critical role that precision components play in the success of your industry. As a top CNC machined parts supplier, we provide a wide array of services tailored to your specific needs.
Whether you require prototyping or mass production, our advanced technology and expert team ensure each part meets the highest quality standards. Our proficiency in various materials, including metals and plastics, enables us to offer adaptable solutions that boost your products’ performance and reliability. With no minimum order requirements, we offer flexible customization to deliver precisely what you need.
RALLY specializes in creating custom solutions that address your unique challenges, whether it’s reducing lead times, enhancing part accuracy, or optimizing costs. Our dedication to quality assurance and ongoing improvement ensures that we deliver parts that adhere to strict industry standards. Partnering with RALLY means choosing a supplier focused on advancing your success through innovation, dependability, and exceptional service.
Our Capabilities
As a leading CNC machining parts supplier, our company has been at the forefront of precision manufacturing for over a decade. We pride ourselves on delivering high-quality components to clients across various industries, including automotive, aerospace, electronics, and healthcare. RALLY’s mission is to provide our customers with the best products and services by leveraging cutting-edge technology and a dedicated team of experts.
Advanced CNC Technology:
Utilizing the latest CNC machines and software to ensure accuracy and efficiency.
Material Expertise:
Working with a wide range of materials, including metals (aluminum, titanium, stainless steel) and plastics (ABS, PEEK, nylon).
Customization and Flexibility:
Offering tailored solutions to meet specific client requirements, from prototyping to large-scale production.
Quality Assurance:
Implementing rigorous quality control measures to ensure every product meets industry standards.
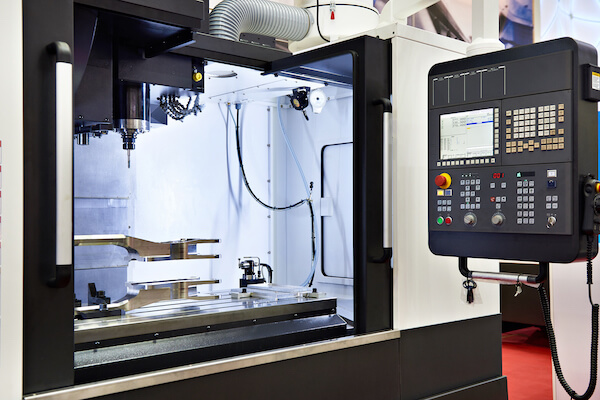
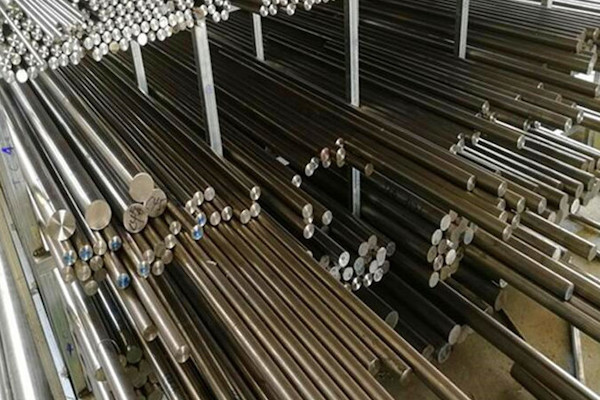
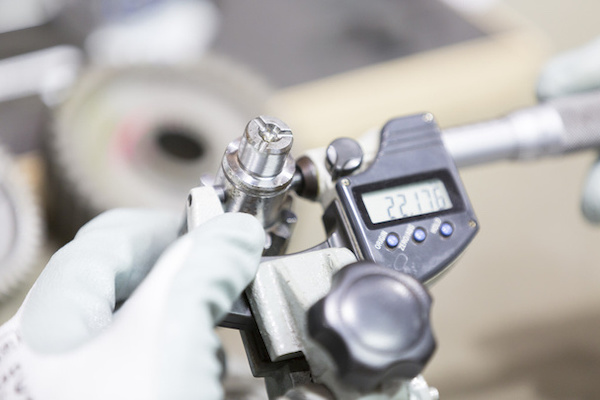
Product Categories
Metal CNC Parts:
Precision-engineered components crafted from high-quality metals like aluminum, brass, and titanium, designed to meet rigorous industry standards and applications.
Plastic CNC Parts:
Durable and versatile parts made from premium plastics such as PEEK, PTFE, and nylon, ideal for diverse industrial and commercial uses.
Custom Machining Solutions:
Tailored manufacturing processes that accommodate unique specifications and design requirements, ensuring optimal performance and functionality for your specific projects.
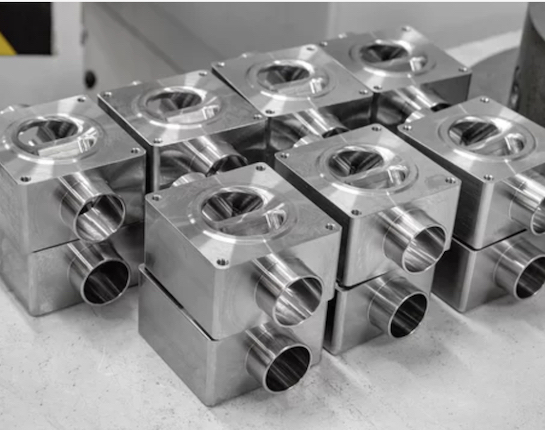
Service Offerings
Prototyping:
Our rapid prototyping services bring your ideas to life with precision and speed, allowing for design testing and refinement before committing to full-scale production, saving time and resources.
Small Batch Production:
Offer flexible small batch production solutions that cater to your specific needs, ensuring high-quality results for limited quantities without compromising efficiency or increasing costs.
Mass Production:
Scalable mass production services provide consistent quality and on-time delivery, utilising advanced CNC technology and stringent quality control processes to support high volume production requirements.
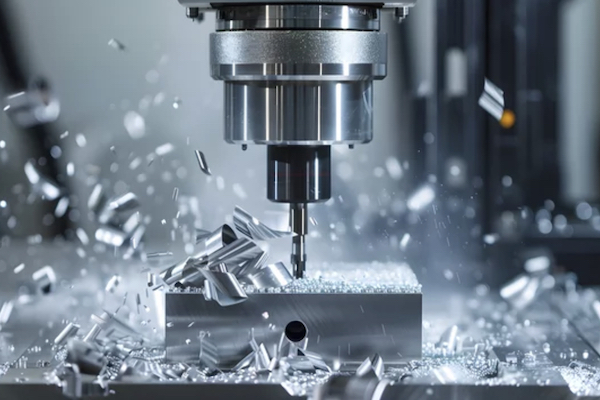
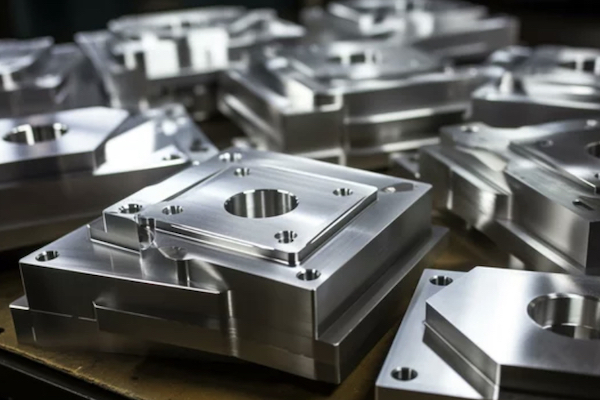
Get a Quick Quote for Free Samples
Request a quick quote now and receive free samples of our precision CNC machining parts tailored to your specifications!
FAQ for CNC Turning Services
1. What is the typical lead time for orders?
2. How do you ensure the quality of your CNC machined parts?
3. What materials can you work with for CNC machining?
4. Can you assist with design optimization for manufacturing?
5. What are your logistics and shipping arrangements?
6. Is there a minimum order quantity requirement?
Get in Touch
Ready to get started? Contact us today for a free quote!
Metal Material
Aluminum, Brass, Stainless Steel, Carbon Steel, Copper, Titanium, etc.
Plastic Material
Acetal (Delrin), PTFE (Teflon), Acrylic (PMMA), PEEK, Nylon, ABS, PC, PP, POM, HDPE, PVC.
Surface Finishing
Anodizing, Powder Coating, Plating, Passivation, Bead Basting, Polishing, etc.
Inquiry Form
Let’s Start A New Project Today, Get Free Samples!
All You Need To Know About CNC Machining Parts
Table of Contents
What are the advantages of CNC machined parts?
CNC machining of parts has many advantages, which makes it a very popular method of machining in modern manufacturing. Here are some of the main advantages:
High Accuracy
CNC machining is able to cut accurately at the micron level, ensuring that parts meet tight tolerances. This high level of precision makes CNC machining suitable for industries such as aerospace, medical and automotive, enabling the manufacture of parts with complex shapes and details.
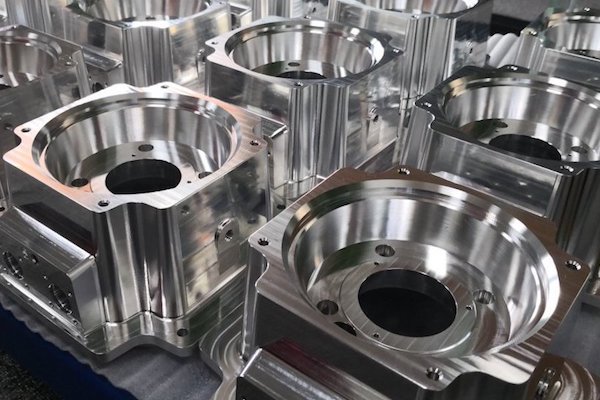
Efficient production
CNC machining is highly automated and capable of working 24/7, which significantly increases productivity. CNC machining allows parts to be produced faster and with shorter lead times than traditional machining methods.
Flexibility and Complex Geometry Machining
CNC machines can handle complex designs and geometries, and support multiple axes simultaneously, making it easy to respond to complex machining requirements. This flexibility allows manufacturers to respond faster to design changes.
Material Versatility
CNC machining is suitable for a wide range of materials, including metals (e.g. aluminum, steel, stainless steel, copper, etc.) and plastics (e.g. ABS, nylon, PTFE, etc.), to meet the needs of different industries and applications.
What is the process of CNC machining?
1. Design Stage
- Product Design: Create detailed 3D models or 2D drawings using computer-aided design (CAD) software. These designs include all necessary dimensions, geometries, and tolerances.
2. Programming Stage
- CNC Programming: Convert the CAD model into a CNC program (G-code) using computer-aided manufacturing (CAM) software to generate machining paths. The program includes tool paths, feed rates, cutting speeds, and other machining parameters.
3. Preparation Stage
Material Preparation: Select and prepare the raw materials needed for machining, cutting them to the appropriate size based on the design drawings.
Machine Setup: Install and adjust the necessary tools and fixtures on the CNC machine to ensure it is in optimal working condition.
4. Machining Stage
First Article Inspection: Perform a trial cut to verify the program’s accuracy and the machine’s setup, ensuring the part meets design requirements.
Batch Production: Once the first article passes inspection, begin batch production. The machine automatically executes the CNC program to perform cutting, milling, drilling, and other operations on the material.
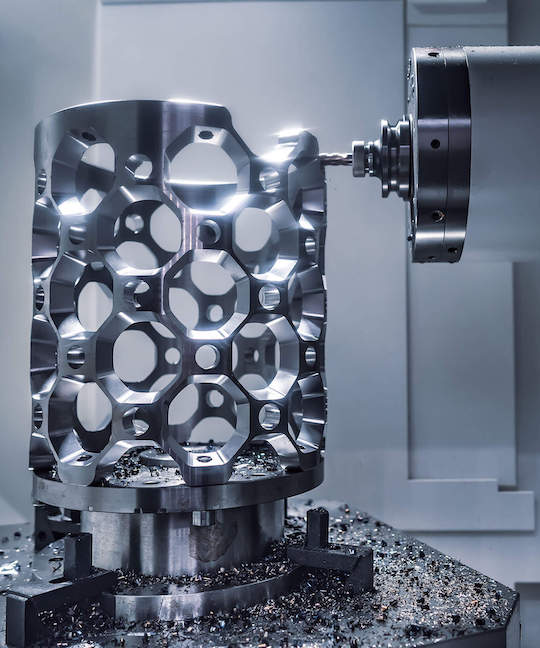
5. Quality Control
Process Monitoring: Continuously monitor machine operations and machining precision during the process, adjusting parameters to ensure quality.
In-Process Inspection: Conduct intermediate inspections on partially completed parts to check dimensions and tolerances.
6. Post-Processing Stage
Deburring and Cleaning: After machining, deburr and clean the parts to remove any burrs and impurities generated during the process.
Surface Treatment: Perform surface treatments such as polishing, painting, or plating as required by the design to enhance the part’s appearance and performance.
7. Final Inspection
- Quality Check: Use precision measuring tools to thoroughly inspect the final product, ensuring all dimensions and tolerances meet design specifications.
How to choose the right material for CNC machining?
There are several key factors to consider when selecting materials for CNC machining.
Strength and hardness:
Choose materials with sufficient strength and hardness to withstand the stresses and wear of the machining process. Aluminium alloys, stainless steel and titanium are commonly used.
Corrosion resistance:
If the end product is to be used in a corrosive environment, it is important to select a material that is corrosion resistant, such as stainless steel.
Thermal conductivity:
The thermal conductivity of a material affects the distribution of heat during the cutting process. Aluminium alloys have good thermal conductivity.
Machinability Assessment:
Evaluate the cutting performance of the material in CNC machining. Factors such as hardness, toughness, and ductility can affect the difficulty of machining. For example, aluminum is easy to machine, while titanium and stainless steel may require harder tools and longer machining times.
Surface Quality:
Some materials are easier to achieve a high-quality surface finish after machining, which can reduce the need for subsequent polishing or surface treatments. For instance, aluminum often results in a smoother finish, whereas harder materials might require additional finishing steps.
Material Cost:
Select materials that fit within your budget. Consider the cumulative effect of material costs in large-scale production. Low-cost materials (such as certain plastics) may be more suitable in specific conditions.
Machining Cost:
The difficulty of machining a material affects the overall machining cost. More challenging materials may require specialized equipment or tools, which can increase production costs.
Prototyping:
Before full-scale production, create a small number of samples or prototypes using the selected material to assess its performance in actual machining and application scenarios.
Performance Validation:
Test the prototype for mechanical properties, chemical stability, and machining effects to ensure the material meets design and application requirements.
How to ensure the quality of CNC machined parts?
Ensuring the quality of CNC machined parts is a multifaceted process that involves all aspects of the process, from design to production. Here are some key strategies and best practices to ensure high quality CNC machined parts:
1. Use High-Quality Raw Materials
- Material Selection: Ensure that high-quality raw materials meeting specifications and performance requirements are used.
- Supplier Evaluation: Choose reliable material suppliers and regularly audit their product quality and delivery capabilities.
2. Advanced Equipment and Technology
- Equipment Maintenance: Regularly maintain and calibrate CNC machines to ensure they are in optimal working condition.
- Technology Upgrades: Utilize the latest machining technologies and software to improve precision and efficiency.
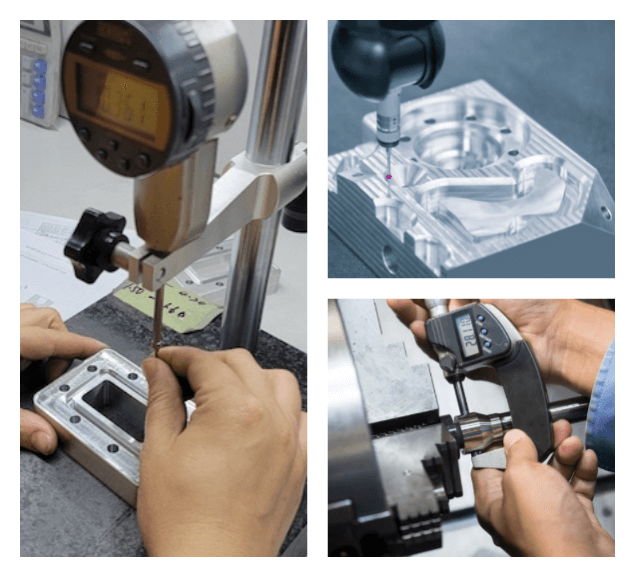
3. Precise Process Control
- Programming Accuracy: Ensure the accuracy of CNC programs to avoid machining deviations due to programming errors.
- Process Monitoring: Monitor key parameters in real-time during machining, such as cutting speed, feed rate, and tool wear, to ensure process stability.
4. Rigorous Quality Inspection
- First Article Inspection: Conduct detailed inspections on the first piece produced in each batch to verify the correctness of machining parameters and process settings.
- In-Process Inspection: Regularly inspect parts during machining to ensure continuous compliance with quality standards.
- Final Inspection: Use precision measurement tools (such as coordinate measuring machines) to thoroughly inspect the final product, ensuring its dimensions and tolerances meet requirements.
5. Training and Management
- Employee Training: Enhance the skills of operators and quality inspectors to ensure they can identify and correct machining issues.
- Quality Management System: Establish and maintain a quality management system that complies with international standards such as ISO to systematically manage and improve quality control processes.
By implementing these steps, you can significantly enhance the quality of CNC machined parts, ensuring that the products meet customer expectations and market demands.
How is the Lead Time for CNC Machining Determined?
The lead time for CNC machining is influenced by several key factors:
Complexity of the Design: Intricate designs with tight tolerances or multi-step processes typically require more time to machine.
Material Availability: The availability of the chosen material can impact how quickly the project can begin. If special or rare materials are required, lead time may increase.
Production Volume: Larger batch sizes or mass production runs generally take longer compared to prototyping or small batch orders.
Current Production Schedule: The supplier’s existing workload and production capacity also affect the turnaround time.
Post-Processing Requirements: If additional processes like heat treatment, surface finishing, or assembly are needed, these will add to the total lead time.
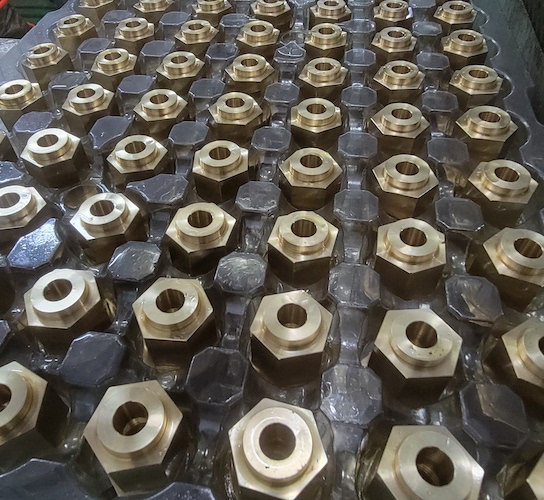
What is the Tolerance Range for CNC Machined Parts?
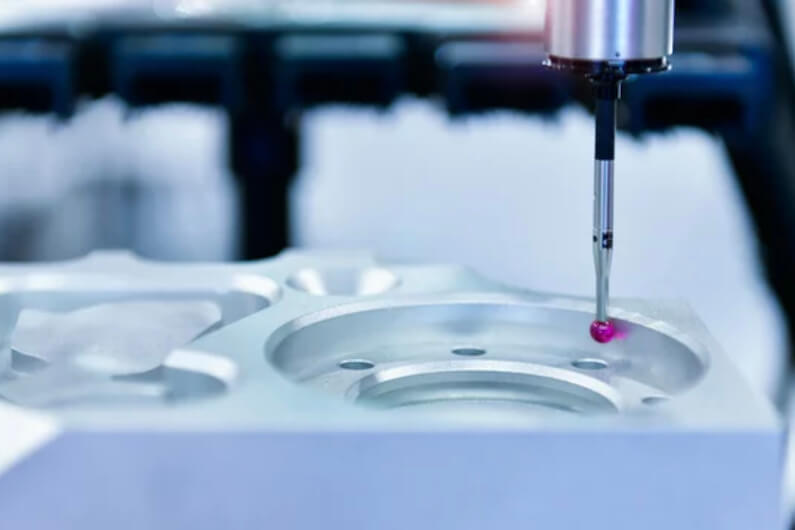
The tolerance range for CNC machined parts can vary depending on several factors:
Material Type:
Different materials, such as metals or plastics, have varying machinability, which can affect the achievable tolerance.
Part Complexity:
More complex designs with intricate features may require tighter tolerances, which can be more challenging to achieve.
Machine Capability:
The precision of the CNC machine itself plays a critical role. High-precision machines can achieve tighter tolerances, often within ±0.001 inches (±0.025 mm) or better.
Application Requirements:
The specific needs of the application, such as those in aerospace or medical industries, might demand stricter tolerances.
Post-Processing:
Additional processes like heat treatment or surface finishing can affect the final tolerance, so these must be factored in during the planning stage.
By understanding these factors, you can better determine the appropriate tolerance for your CNC machined parts and ensure they meet the necessary specifications.
How to Handle Potential Issues During CNC Machining?
Addressing issues during CNC machining is crucial to ensure the quality and precision of the final parts. Here’s how potential problems can be managed:
Regular Monitoring and Inspection:
Continuous monitoring during machining and regular inspections help identify issues early, such as tool wear or machine misalignment, allowing for quick adjustments.
Material Selection:
Choosing the right material for the part is essential. Improper material selection can lead to machining difficulties, such as excessive tool wear or part deformation. Working closely with suppliers can help ensure the correct material is used.
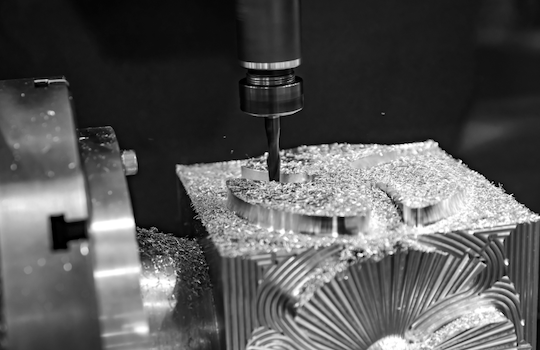
Tooling and Fixture Optimization:
Using the appropriate tools and fixtures can prevent problems like part movement, vibration, or poor surface finish. Ensuring tools are sharp and well-maintained is also key.
Programming Accuracy:
CNC programming errors can lead to dimensional inaccuracies or surface defects. Careful review and simulation of CNC programs before actual machining can help avoid such issues.
Addressing Heat and Stress:
Excessive heat generation during machining can cause material distortion or warping. Managing cutting speeds, feeds, and cooling techniques is important to mitigate these effects.
By implementing these strategies, potential issues during CNC machining can be effectively managed, ensuring high-quality results and minimizing production delays.
Work with RALLY for CNC Turning Parts
Request a quote for new project today! No minimum order quantity and free samples available!