PEEK Machining Services
Custom production, free samples, and fast delivery to meet your specific needs.
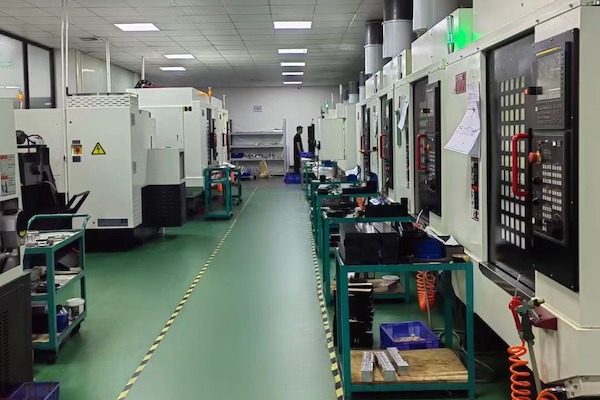
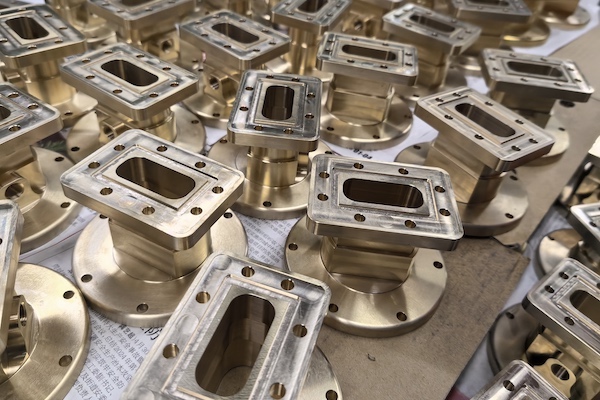
CNC Machining Parts Supplier
At RALLY, we understand the critical role that precision components play in the success of your industry. As a top CNC machined parts supplier, we provide a wide array of services tailored to your specific needs.
Whether you require prototyping or mass production, our advanced technology and expert team ensure each part meets the highest quality standards. Our proficiency in various materials, including metals and plastics, enables us to offer adaptable solutions that boost your products’ performance and reliability. With no minimum order requirements, we offer flexible customization to deliver precisely what you need.
RALLY specializes in creating custom solutions that address your unique challenges, whether it’s reducing lead times, enhancing part accuracy, or optimizing costs. Our dedication to quality assurance and ongoing improvement ensures that we deliver parts that adhere to strict industry standards. Partnering with RALLY means choosing a supplier focused on advancing your success through innovation, dependability, and exceptional service.
Our PEEK Machining Services:
RALLY Precision Machinery is a professional manufacturer specializing in CNC machining services for both metals and high-performance plastics. With years of expertise, we are committed to providing top-quality machined components to meet industry demands.
Precision CNC Machining:
Specialized PEEK machining that ensures tight tolerances and smooth surface finishes.
Custom Production:
We manufacture components based on your designs and technical drawings to meet exact requirements.
Quality Assurance:
All materials and processes meet international standards, including FDA and ISO certifications.
Flexible Quantities:
No minimum order quantities; we support prototypes, small batches, and mass production.
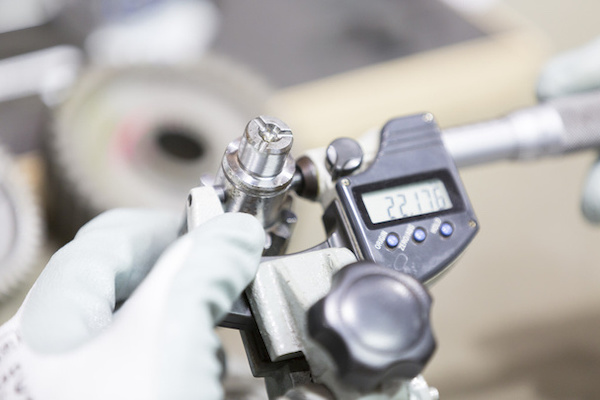
Product Categories
Metal CNC Parts:
Precision-engineered components crafted from high-quality metals like aluminum, brass, and titanium, designed to meet rigorous industry standards and applications.
Plastic CNC Parts:
Durable and versatile parts made from premium plastics such as PEEK, PTFE, and nylon, ideal for diverse industrial and commercial uses.
Custom Machining Solutions:
Tailored manufacturing processes that accommodate unique specifications and design requirements, ensuring optimal performance and functionality for your specific projects.
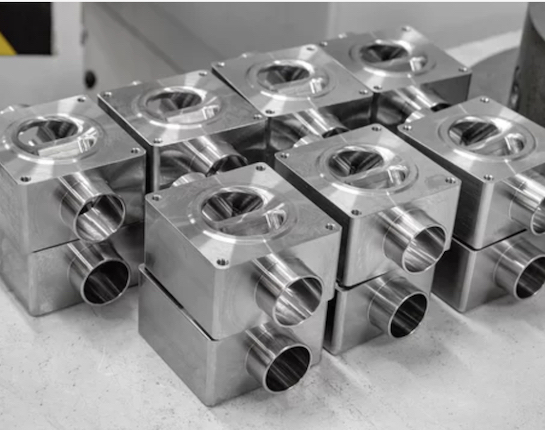
Service Offerings
Prototyping:
Our rapid prototyping services bring your ideas to life with precision and speed, allowing for design testing and refinement before committing to full-scale production, saving time and resources.
Small Batch Production:
Offer flexible small batch production solutions that cater to your specific needs, ensuring high-quality results for limited quantities without compromising efficiency or increasing costs.
Mass Production:
Scalable mass production services provide consistent quality and on-time delivery, utilising advanced CNC technology and stringent quality control processes to support high volume production requirements.
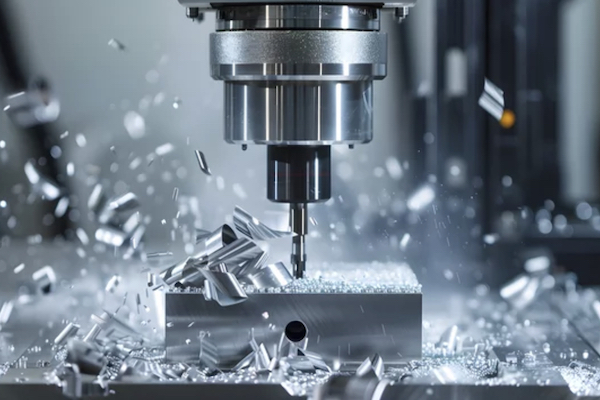
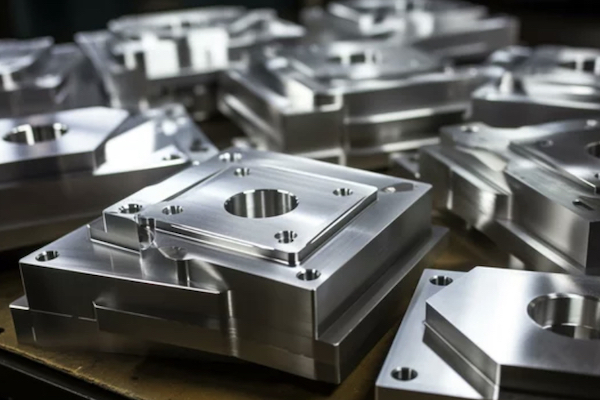
Get a Quick Quote for Free Samples
Request a quick quote now and receive free samples of our precision CNC machining parts tailored to your specifications!
FAQ for PEEK Machining
1. How does RALLY ensure the precision and quality of PEEK parts?
2. Do you provide PEEK materials with FDA or ISO certification?
3. What is the production lead time for PEEK CNC parts?
4. Is there a minimum order quantity (MOQ) for PEEK machining?
5. Do you offer design consultation or technical support?
6. How to Get a Quote for PEEK Machined Parts?
7. Does RALLY offer design support and prototyping for PEEK parts?
Get in Touch
Ready to get started? Contact us today for a free quote!
Metal Material
Aluminum, Brass, Stainless Steel, Carbon Steel, Copper, Titanium, etc.
Plastic Material
Acetal (Delrin), PTFE (Teflon), Acrylic (PMMA), PEEK, Nylon, ABS, PC, PP, POM, HDPE, PVC.
Surface Finishing
Anodizing, Powder Coating, Plating, Passivation, Bead Basting, Polishing, etc.
Inquiry Form
Let’s Start A New Project Today, Get Free Samples!
All You Need To Know About PEEK Machining
Table of Contents
Properties of PEEK Material
PEEK (Polyether Ether Ketone) offers excellent mechanical strength, high fatigue resistance, and durability, making it ideal for demanding applications. It withstands continuous use at temperatures up to 250°C (482°F) and provides exceptional chemical resistance against acids, solvents, and salts.
Additionally, PEEK’s low friction and wear properties make it suitable for precision components, while its biocompatibility allows for use in medical implants and devices. These features make PEEK a preferred material across industries such as aerospace, automotive, and healthcare.
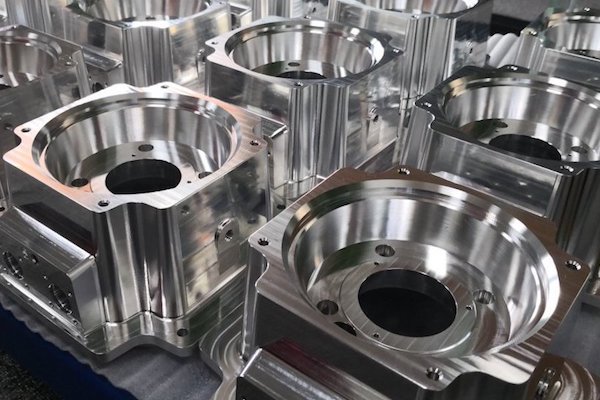
Quality Control and Inspection Process in PEEK Machining
1. Material Verification and Certification
- We start by sourcing PEEK materials from certified suppliers, ensuring they meet FDA, ISO, or other industry-specific standards. Each batch is inspected for authenticity, chemical composition, and mechanical properties to guarantee material consistency.
2. In-Process Monitoring and Dimensional Control
- Throughout machining, we conduct real-time measurements to maintain strict tolerances. CNC machines are calibrated regularly, and key parameters like temperature and surface finish are closely monitored to avoid defects or deformation during production.
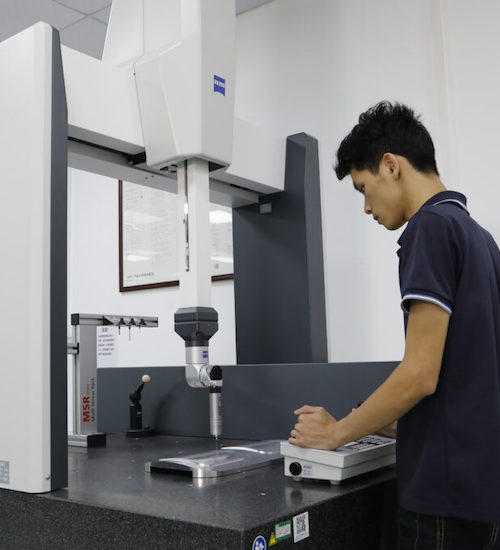
3. Post-Production Inspection
- After machining, each part undergoes detailed dimensional inspection using tools such as coordinate measuring machines (CMM). We also perform visual inspections to check for surface quality, ensuring parts are free of scratches, burrs, or irregularities.
4. Performance and Final Compliance Testing
- For specialized applications, parts are tested for thermal resistance, chemical stability, or wear performance based on customer requirements. A final inspection report is issued, documenting all quality control results, including material certification and dimensional accuracy, ensuring full traceability.
Industries and Applications of PEEK
PEEK (Polyether Ether Ketone) is widely used across several industries due to its excellent mechanical, thermal, and chemical properties.
PEEK is used in lightweight, high-performance components such as valve components, seals, and cable insulation. It withstands extreme temperatures and harsh environments, ensuring long-term reliability in aircraft systems.
In automotive applications, PEEK is ideal for bearings, bushings, gaskets, and seals. Its resistance to wear, chemicals, and heat helps improve vehicle efficiency and reduce maintenance needs.
PEEK’s biocompatibility and sterilization capability make it suitable for implants, surgical instruments, and dental devices. It offers a lightweight, metal-free solution for medical applications requiring durability and safety.
PEEK is used as electrical insulation material, connectors, and wafer holders due to its high temperature resistance, electrical insulation properties, and chemical stability, ensuring reliability in precision electronics manufacturing.
Is PEEK Suitable for Medical Applications?
Yes, PEEK (Polyether Ether Ketone) is highly suitable for medical applications due to its outstanding biocompatibility and excellent mechanical properties.
It is widely used in surgical instruments, implants, and dental devices, providing a lightweight, non-metal alternative for medical applications that require durability and precision. PEEK’s chemical resistance allows it to withstand exposure to bodily fluids, disinfectants, and sterilization methods, including high-temperature autoclaving, without degrading.
Its low friction and wear resistance make it ideal for implants such as spinal cages and joint replacements, ensuring long-term performance.
Additionally, PEEK is radiolucent, meaning it does not interfere with imaging techniques like X-rays or MRI scans, making it advantageous for diagnostic applications.
These features make PEEK an excellent material for both temporary and permanent medical solutions.
Differences Between PEEK Grades
PEEK comes in various grades, each tailored for specific performance requirements and applications. Selecting the right grade depends on the mechanical, chemical, and thermal demands of the intended use.
PEEK Grade | Key Features | Common Applications |
---|---|---|
Unfilled PEEK | Excellent mechanical properties, chemical resistance, thermal stability | Medical implants, electrical insulation, general-purpose components |
Glass-Fiber Reinforced PEEK | Enhanced strength, stiffness, dimensional stability | Structural parts in aerospace and automotive industries |
Carbon-Fiber Reinforced PEEK | Superior strength, wear resistance, thermal conductivity | High-performance bearings, bushings, load-bearing components |
PTFE-Filled PEEK | Excellent wear resistance, low friction | Seals, gaskets, sliding components in industrial machinery |
What surface treatments are available for PEEK parts?
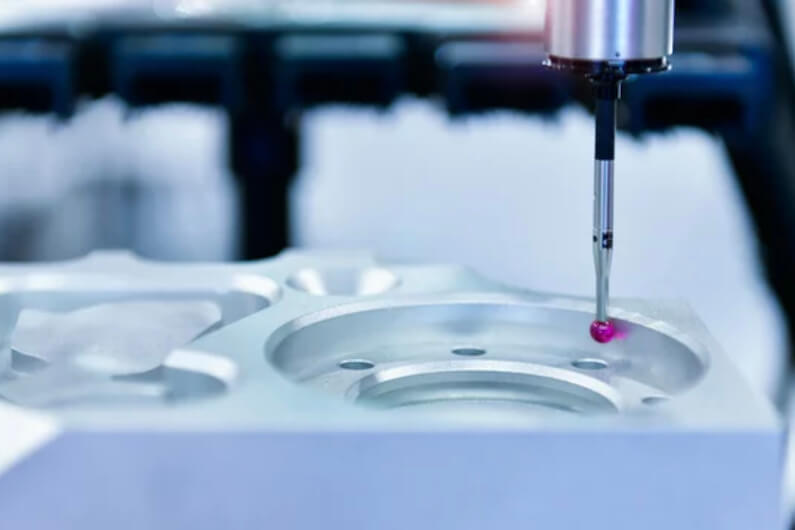
Polishing: Improves surface smoothness and reduces friction.
Annealing: Relieves internal stress to prevent warping during use.
Protective Coatings: PTFE or other coatings enhance wear resistance and chemical stability.
Plasma or Chemical Treatments: Improve bonding strength for adhesives or overmolding.
Surface Texturing: Custom textures for better grip or aesthetic purposes if required.
PEEK Machined Parts Applications in Submarine Industry
RALLY has extensive experience in manufacturing high-precision PEEK components tailored for the demanding needs of the submarine industry. Below are key applications where our PEEK machined parts provide superior performance:
Seals and Gaskets
PEEK’s excellent high-temperature, chemical, and pressure resistance makes it ideal for seals and gaskets.
These components maintain airtightness and safety under extreme underwater conditions, ensuring the long-term reliability of submarine systems.
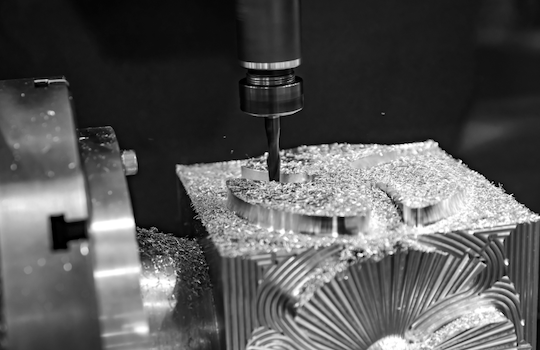
Bearings and Sliding Components
- With a low friction coefficient and high wear resistance, PEEK is perfect for bearings and sliding parts used in submarine systems. These components perform reliably even in low-lubrication environments, reducing maintenance needs and increasing operational efficiency.
Electrical Insulation Materials
- PEEK offers exceptional electrical insulation, making it suitable for critical submarine electrical systems. RALLY produces PEEK-based cable sheaths, insulating plates, and connectors that perform reliably in high-moisture environments, ensuring system stability.
Our expertise and advanced machining capabilities allow us to deliver high-quality PEEK parts that meet the stringent requirements of the submarine industry, ensuring durability and performance in challenging underwater environments.
Work with RALLY for PEEK Machining Parts
Request a quote for new project today! No minimum order quantity and free samples available!