Introduction:
In the world of precision machining, aluminum stands out as a top choice for countless CNC projects, celebrated for its versatility and strength. Yet, with so many options, how do you make sure you’re partnering with the right CNC service for your unique aluminum projects? This guide dives deep into the essentials of aluminum CNC projects, unraveling why aluminum has earned its place in the industry and providing you with practical tips to pinpoint a CNC machining service that truly aligns with your goals.
1. What Are Aluminum CNC Projects?
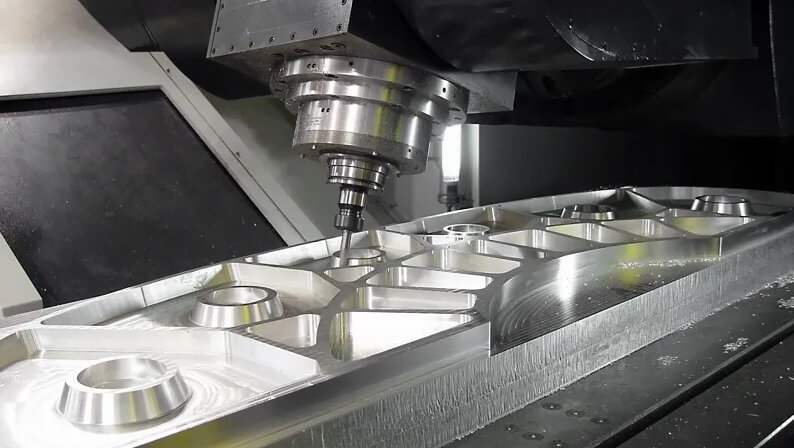
Aluminum CNC projects encompass the meticulous crafting of custom parts, prototypes, and components, all brought to life through the precise control of CNC machinery. This process sculpts aluminum with pinpoint accuracy, breathing life into designs tailored for industries as demanding as automotive, aerospace, and medical.
Known for its lightweight structure, impressive durability, and remarkable adaptability, aluminum has become a cornerstone material across various fields, meeting both functional demands and design complexities with ease. These projects aren’t just valued—they’re essential, enabling innovation and excellence in high-stakes industries.
Common examples include:
Industry | Common Aluminum CNC Parts | Description |
---|---|---|
Automotive | Engine parts, housings, brackets | Aluminum CNC machining is ideal for automotive parts due to its strength-to-weight ratio. Engine parts, housings, and brackets benefit from aluminum’s lightweight and durable properties, improving vehicle performance and fuel efficiency. |
Aerospace | Structural components, frames | The aerospace industry values aluminum CNC parts for their light weight and high strength. Structural components and frames made from aluminum reduce overall aircraft weight, enhancing fuel efficiency and maneuverability. |
Consumer Electronics | Heat sinks, enclosures | Aluminum’s excellent heat dissipation properties make it ideal for heat sinks in electronics. Additionally, CNC-machined aluminum enclosures provide durability and a sleek, modern finish for electronic devices. |
Medical Devices | Precision surgical tools, implants | Aluminum CNC parts are essential in medical devices, where precision is critical. Surgical tools and implants benefit from aluminum’s lightweight, biocompatible, and corrosion-resistant properties, ensuring reliability and safety. |
2. Why choose aluminum CNC machining project?
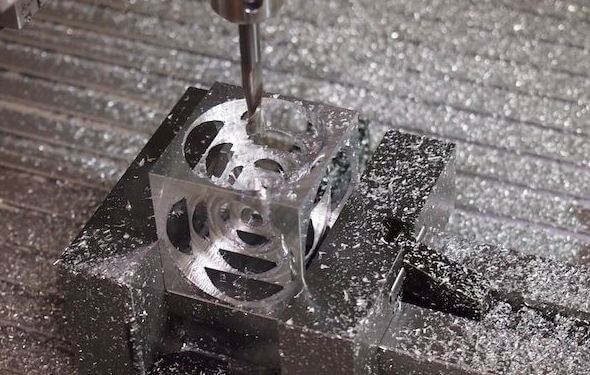
Opting for aluminum in your CNC project opens up a world of benefits. Here’s why this versatile metal is so often the top choice:
Lightweight Strength: Aluminum boasts an impressive strength-to-weight ratio, delivering durability without the bulk—a perfect match for components that demand robustness without the burden of extra weight.
Superb Machinability: Known for its exceptional machinability, aluminum responds beautifully to CNC processes, enabling precision cuts, intricate shapes, and reduced risk of flaws. Its adaptability saves time and boosts production efficiency.
Natural Corrosion Resistance: Aluminum’s natural resistance to corrosion makes it a reliable option for parts exposed to tough conditions, enhancing longevity even in challenging environments.
Cost-Effective Efficiency: Though not as low-cost as some plastics, aluminum’s durability and efficient machinability make it a smart, budget-friendly investment for projects demanding long-lasting, high-quality parts.
With all these advantages, it’s clear why aluminum continues to be a material of choice across industries.
3. Key Success Factors for Aluminum CNC Projects
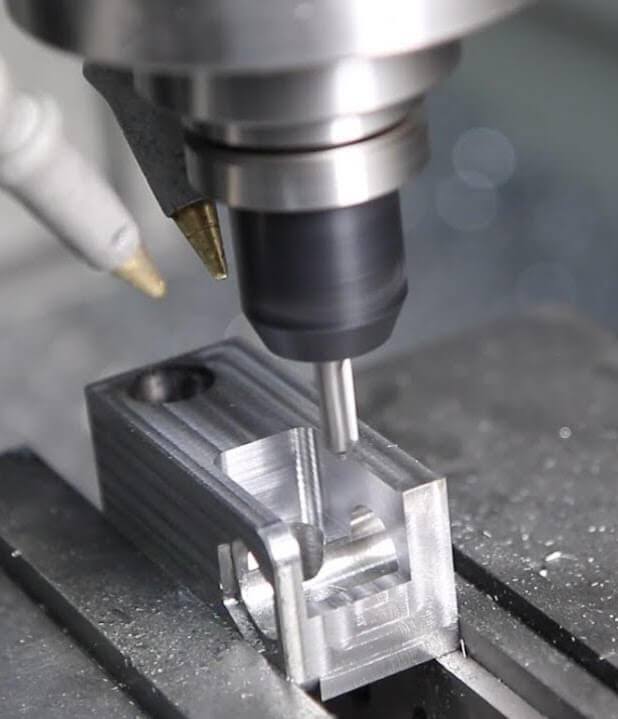
To achieve top results in your aluminum CNC project, keep these crucial factors front and center:
Selecting the Right Alloy: The aluminum alloy you choose makes all the difference. Opt for 6061 for a balance of strength and workability or 7075 when toughness is paramount. Each alloy brings unique properties tailored to specific applications—choose wisely.
Navigating Design Complexity: Not all providers are equipped for intricate designs. Ensure yours can handle the level of detail your project requires without compromising on quality or precision.
Meeting Precision Standards: Precision is everything in CNC machining. Confirm that your provider can meet the tight tolerances your project demands, especially if high-precision parts are non-negotiable.
Choosing the Perfect Surface Finish: Aesthetics and functionality go hand-in-hand. Whether it’s anodizing for durability or powder coating for a refined look, discuss finish options early to align with both visual and practical objectives.
Managing Lead Times: Timing matters. From prototype to final production, make sure your provider can match your project timeline, ensuring that each phase aligns seamlessly with your broader schedule.
Keeping these factors in check can elevate your CNC project from good to exceptional.
Get Your CNC Parts Into Production Today
Your Global Partner for Quality CNC Machining Services in China!
4. How to Choose a Reliable CNC Service Provider
Selecting the perfect CNC machining partner is vital for aluminum CNC projects. The outcome—whether in quality, precision, or efficiency—hinges on the provider’s specialized expertise in aluminum. Here’s what we prioritize to drive your project toward success:
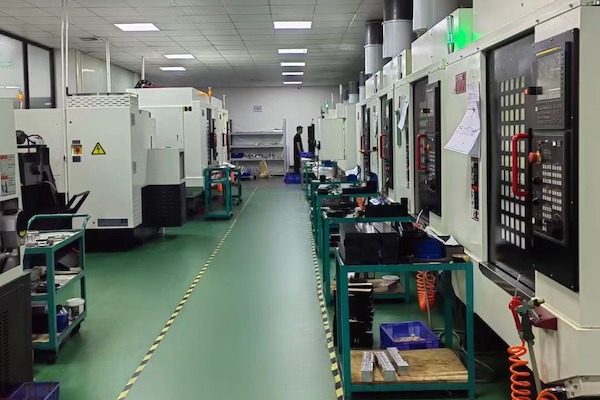
- Experience with Aluminum Alloy Choices
Look for a provider experienced in working with different aluminum alloy choices, such as 6061 and 7075. Each alloy has unique properties, and a knowledgeable provider can guide you in selecting the right material based on your project’s needs. - State-of-the-Art CNC Machining Services
Advanced CNC machining services are essential for achieving precise tolerances and high-quality finishes. Providers with up-to-date CNC machines can handle even the most complex designs with accuracy. - Robust Quality Control
Quality control is critical in aluminum CNC machining. A reliable service provider conducts thorough checks at every stage, ensuring each part meets your specifications. - Clear Communication and Support
Throughout the project, clear communication is key. Your CNC machining service provider should offer consistent updates and be responsive to any questions, helping your project stay on track. - Client Reviews and Feedback
Finally, check for client feedback. A provider with positive reviews from other aluminum CNC projects is more likely to deliver high-quality results and reliable service.
By following these guidelines, you’ll be well on your way to a successful aluminum CNC project with precision and quality you can trust
5. Popular Applications of Aluminum CNC Projects
Aluminum CNC projects are widely used across various industries due to aluminum’s strength, lightweight, and corrosion resistance. Here are some of the most common applications:
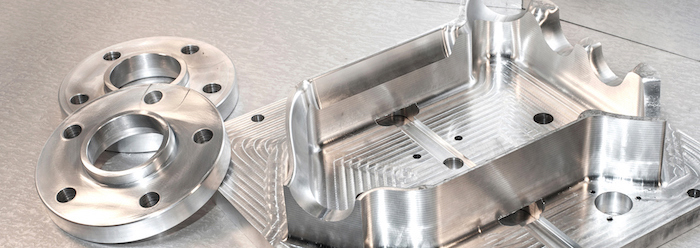
Common Aluminum CNC Projects | Applications |
---|---|
Aerospace Components | Used for aircraft structures, housings, and brackets due to aluminum’s high strength-to-weight ratio. |
Automotive Parts | Applied in engine parts, frames, wheels, and transmission components to reduce vehicle weight and improve fuel efficiency. |
Medical Devices | Utilized in surgical instruments, imaging equipment, and diagnostic machines due to aluminum’s durability and ease of sterilization. |
Consumer Electronics | Popular in smartphone cases, laptop frames, and other electronics for durability, corrosion resistance, and high-quality finishes. |
Industrial Equipment | Essential for machinery and equipment parts requiring precision, strength, and lightweight construction for industrial applications. |
These applications showcase the versatility of aluminum CNC projects, meeting the diverse needs of industries requiring high-performance, custom-engineered components.
6. Surface Treatment Options for Aluminum CNC Projects
Applying the right surface treatment transforms aluminum CNC parts, boosting both their visual appeal and functional resilience. Here are some popular treatments and the unique advantages they bring to various industries:
Anodizing
- Industry Applications: Aerospace, Automotive, Consumer Electronics
- Advantages: Anodizing adds a protective oxide layer to aluminum parts, improving corrosion resistance and wear durability. In aerospace, anodizing is essential to withstand harsh environmental conditions. In consumer electronics, it provides a sleek, matte finish while protecting against scratches.
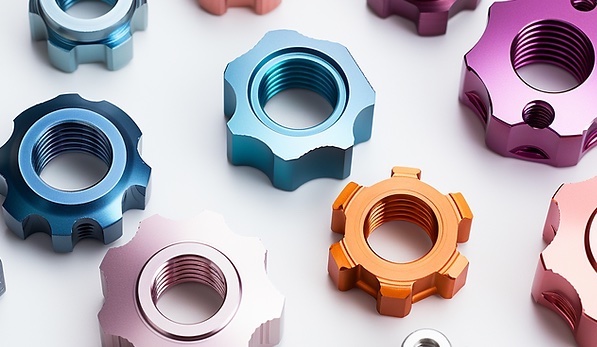
Polishing
- Industry Applications: Medical Devices, Automotive, Consumer Goods
- Advantages: Polishing creates a smooth, mirror-like finish, which is ideal for parts that require high aesthetic appeal or hygiene standards. Medical devices benefit from polished aluminum due to its easy-to-clean surface, essential for maintaining sterile environments. Automotive parts, such as trim and accents, also use polishing to achieve a premium look.
Powder Coating
- Industry Applications: Industrial Equipment, Outdoor Products, Home Appliances
- Advantages: Powder coating offers a durable, colorful finish that resists chipping, scratching, and fading. In industrial equipment, powder-coated aluminum withstands heavy usage and exposure to harsh environments. Outdoor products, such as patio furniture or lighting fixtures, benefit from powder coating due to its weather-resistant properties.
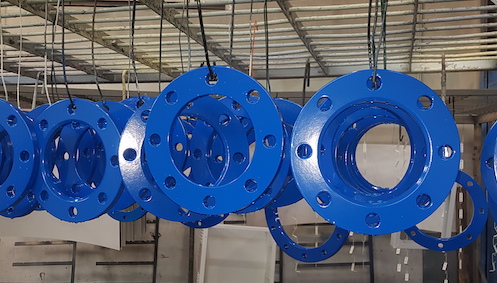
Sandblasting
- Industry Applications: Electronics, Industrial Machinery, Architectural Components
- Advantages: Sandblasting provides a matte, textured finish, enhancing grip and reducing glare. In electronics, sandblasted aluminum enclosures help reduce fingerprints and scratches. Industrial machinery often uses sandblasting to create surfaces that are less reflective, improving safety and usability in high-glare settings.
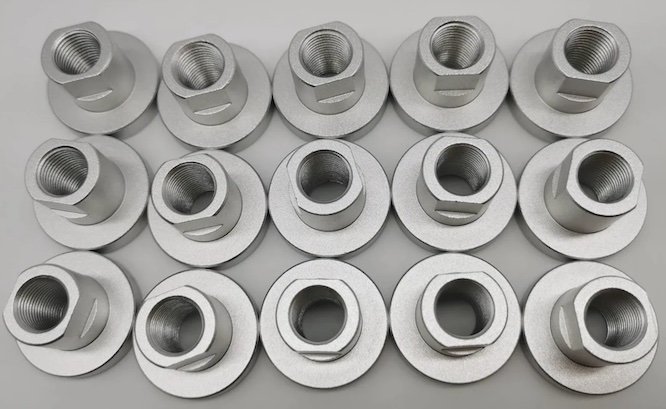
Selecting an industry-specific surface treatment elevates both performance and aesthetics of aluminum CNC parts. These examples reveal how surface treatments serve not merely as cosmetic upgrades but as essential enhancements tailored to meet demanding applications.
Get Your CNC Parts Into Production Today
Your Global Partner for Quality CNC Machining Services in China!
7. Steps to Ensure a Smooth Aluminum CNC Project
Aluminum CNC projects require precision and expertise to achieve top-quality parts. From selecting the right material to choosing a reliable provider, here’s everything you need to ensure project success.
1)Define Project Requirements Clearly – Start by outlining specific requirements for dimensions, tolerances, material type, and any surface finishes. A clear plan helps ensure the machining service understands your expectations and can meet them accurately.
2)Select a Reliable CNC Service Provider – Research potential CNC providers, focusing on their experience with aluminum projects, equipment quality, and customer reviews. Choose one with proven expertise to handle your project with precision.
3)Double-Check Design Specifications – Before production begins, review design files for accuracy. Ensure that technical drawings or CAD files align with your intended specifications to avoid errors during machining.
4)Request a Prototype for Testing – For complex or high-value parts, consider requesting a prototype. Testing a sample allows you to verify fit, function, and finish, reducing the risk of issues in the final production run.
5)Maintain Open Communication – Keep regular contact with your CNC provider throughout the project. This communication helps address any challenges promptly, keeping the project on track for a successful, timely completion.
By following these guidelines, you’ll be well on your way to a successful aluminum CNC project with precision and quality you can trust.
Work with RALLY for CNC Machining Parts
Request a quote for new project today! No minimum order quantity and free samples available!